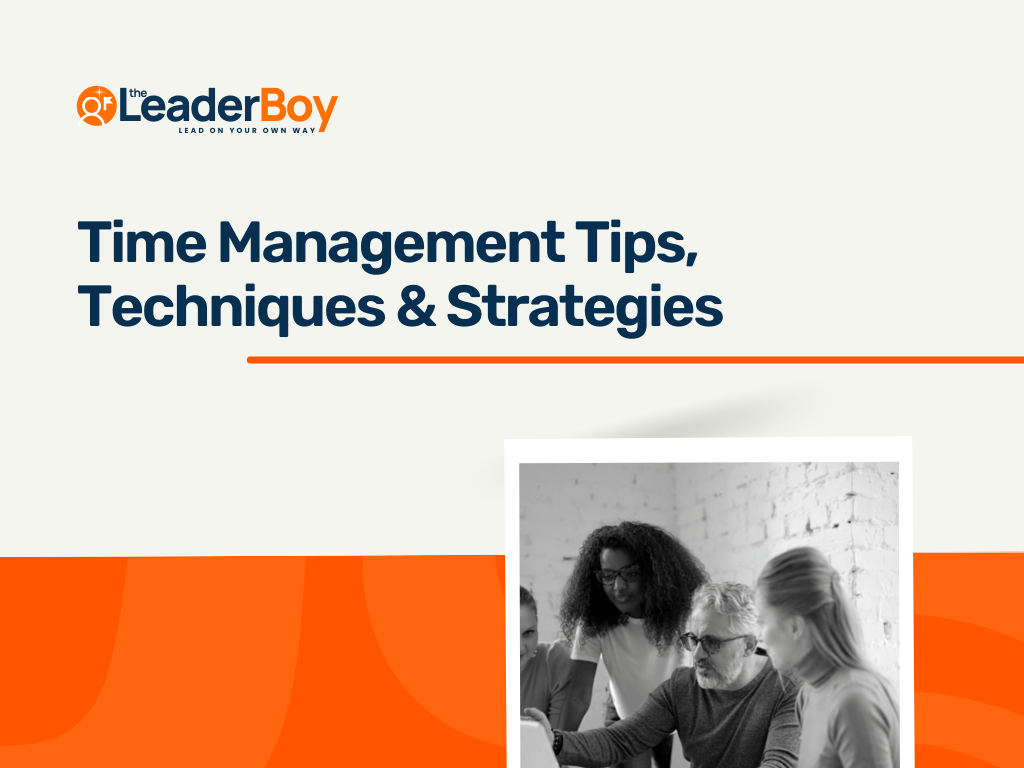
The Journal of Supply Chain Management is a leading scientific journal in supply chain research. Editors seek original contributions that will provide insight into complex operations networks. All research paradigms are welcome. The goal of the journal is to foster debate. The journal welcomes papers that use quantitative, qualitative, mixed-methods approaches. The journal can be found online or in print. You can find more information on the journal's website. The following are examples of research articles that have been published in the journal.
Journal of Supply Chain Management
The Journal of Supply Chain Management is an academic quarterly journal that is peer-reviewed. It was founded in 1965 and covers the areas of supply chain management, marketing, operations management, and strategic management. Wiley-Blackwell published the journal. James Wiley was the founder of this journal. He wanted to publish articles for supply chain managers. With an increasing readership and expanding topics, this academic journal continues growing.
The journal publishes original articles that are relevant to Supply Chain Management. It is an academic journal. The journal emphasizes operations management as well as global perspectives. However, articles must be grounded in PSM theory and methods and be methodologically sound. The journal hopes to foster debate between supply chain professionals and researchers. You can submit articles to Journal of Supply Chain Management, if your specialty is supply chain management.
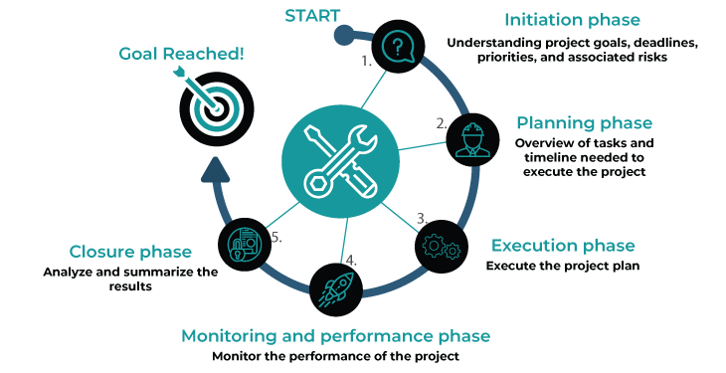
JSCM
The Journal of Supply Chain Management is a peer-reviewed online journal dedicated to supply chain management and related disciplines. Its content focuses on manufacturing, warehousing, and reverse supply chains, and includes a variety of articles that examine key business issues and provide practical guidance. The Journal also publishes recent research on various topics. It is a valuable resource that professionals can use to find out more about supply chains management.
The SCM Journal ListTM is an index of supply chain research output that has been published in top journals. This list includes research on supply chains topics. It also includes research in the analytical and empirical arenas. The journal list also contains the most cited research papers. The journal's "impact factor" is calculated based on how many citations an article has received. The SCM Journal List, which includes articles relevant to academics, practitioners, supply chain experts, is updated every year.
IJSOM
The Journal of Supply Chain Management offers research articles on the subject of supply chain management. The journal publishes original research as well as high-quality articles. This journal has published articles on many aspects of supply chain management in its 51st consecutive year of publication. In addition to articles, the Journal also publishes case studies and other research related to supply chain management.
The mission of the Journal of Supply Chain Management is to promote the science of supply chain management. It focuses on both the global aspect of supply chain management as well as the operational policies and methods. It also offers a forum to discuss and debate research issues. It was recently ranked number one among the 159 journals related to Economics, Finance, Information Technology and Operations. Its content is focused on the global supply chain management industry, and its content is constantly evolving.
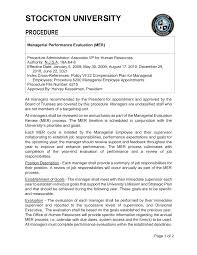
SCM 4 ECR
EDI, a common technology in journal supply chain management, is an example of a shared technology. EDI aims increase the value of consumer products via better supply chains. ECR can help manufacturers make more from less raw material by integrating EDI within their supply chain management. ECR is a good option for manufacturers producing consumer goods as it can improve quality and speed to market.
The ECR Model is a collaborative business process that retailers and manufacturers use to manage the supply chain. It aims to improve the flow in goods through the supply chains. The program uses a variety of technologies to assist retailers and manufacturers in improving their efficiency. The ECR program uses a variety of technologies including Barcode/Scanners, Electric Data interchanges, Cross docking and Action Based costs. The objective of this program is to facilitate the replacement of products in stores. It increases the product's reliability and decreases inventory costs.
FAQ
What is a basic management tool used in decision-making?
A decision matrix is an easy but powerful tool to aid managers in making informed decisions. It allows them to think through all possible options.
A decision matrix can be used to show alternative options as rows or columns. This makes it easy for you to see how each option affects other options.
This example shows four options, each represented by the boxes on either side of the matrix. Each box represents an option. The top row depicts the current status quo, while the bottom row represents what would happen if no action was taken.
The effect of choosing Option 1 can be seen in column middle. In this example, it would lead to an increase in sales of between $2 million and $3 million.
The effects of options 2 and 3 are shown in the next columns. These are both positive changes that increase sales by $1million and $500,000. However, these also involve negative consequences. Option 2 increases costs by $100 thousand, while Option 3 decreases profits to $200 thousand.
The final column shows results of choosing Option 4. This involves decreasing sales by $1 million.
The best thing about using a decision matrix is that you don't need to remember which numbers go where. You can just glance at the cells and see immediately if one given choice is better.
The matrix has already done all of the work. It's as easy as comparing numbers in the appropriate cells.
Here's an example of how you might use a decision matrix in your business.
You need to decide whether to invest in advertising. By doing so, you can increase your revenue by $5 000 per month. However, this will mean that you'll have additional expenses of $10,000.
The net result of advertising investment can be calculated by looking at the cell below that reads "Advertising." It is 15 thousand. Advertising is worth more than its cost.
What are the 4 main functions of management?
Management is responsible to plan, organize, direct, and control people and resources. This includes setting goals, developing policies and procedures, and creating procedures.
Management aids an organization in reaching its goals by providing direction and coordination, control, leadership motivation, supervision, training, evaluation, and leadership.
Management has four primary functions:
Planning - Planning refers to deciding what is needed.
Organizing – Organizing means deciding how to organize things.
Directing - Directing is when you get people to do what you ask.
Controlling – Controlling is the process of ensuring that tasks are completed according to plan.
It seems so difficult sometimes to make sound business decisions.
Complex business systems have many moving parts. They require people to manage multiple priorities and deal with uncertainty and complexity.
The key to making good decisions is to understand how these factors affect the system as a whole.
You need to be clear about the roles and responsibilities of each system. You then need to consider how those individual pieces interact with each other.
You need to ask yourself if your previous actions have led you to make unfounded assumptions. If you don't have any, it may be time to revisit them.
Asking for assistance from someone else is a good idea if you are still having trouble. They may see things differently from you and have insights that could help you find a solution.
How does a manager learn to manage?
By practicing good management skills at all times.
Managers should monitor the performance and progress of their subordinates.
You should immediately take action if you see that your subordinate is not performing as well as you would like.
You should be able pinpoint what needs to improve and how to fix it.
Statistics
- The BLS says that financial services jobs like banking are expected to grow 4% by 2030, about as fast as the national average. (wgu.edu)
- Your choice in Step 5 may very likely be the same or similar to the alternative you placed at the top of your list at the end of Step 4. (umassd.edu)
- As of 2020, personal bankers or tellers make an average of $32,620 per year, according to the BLS. (wgu.edu)
- 100% of the courses are offered online, and no campus visits are required — a big time-saver for you. (online.uc.edu)
- Our program is 100% engineered for your success. (online.uc.edu)
External Links
How To
How can Lean Manufacturing be done?
Lean Manufacturing uses structured methods to reduce waste, increase efficiency and reduce waste. They were created in Japan by Toyota Motor Corporation during the 1980s. The goal was to produce quality products at lower cost. Lean manufacturing eliminates unnecessary steps and activities from a production process. It has five components: continuous improvement and pull systems; just-in time; continuous change; and kaizen (continuous innovation). Pull systems allow customers to get exactly what they want without having to do extra work. Continuous improvement involves constantly improving upon existing processes. Just-in-time refers to when components and materials are delivered directly to the point where they are needed. Kaizen means continuous improvement. Kaizen involves making small changes and improving continuously. The 5S acronym stands for sort in order, shine standardize and maintain. To achieve the best results, these five elements must be used together.
Lean Production System
Six key concepts form the foundation of the lean production system:
-
Flow: The goal is to move material and information as close as possible from customers.
-
Value stream mapping is the ability to divide a process into smaller tasks, and then create a flowchart that shows the entire process.
-
Five S’s - Sorted, In Order. Shine. Standardize. And Sustain.
-
Kanban – visual signals like colored tape, stickers or other visual cues are used to keep track inventory.
-
Theory of constraints - identify bottlenecks in the process and eliminate them using lean tools like kanban boards;
-
Just-in-time - deliver components and materials directly to the point of use;
-
Continuous improvement - Make incremental improvements rather than overhauling the entire process.