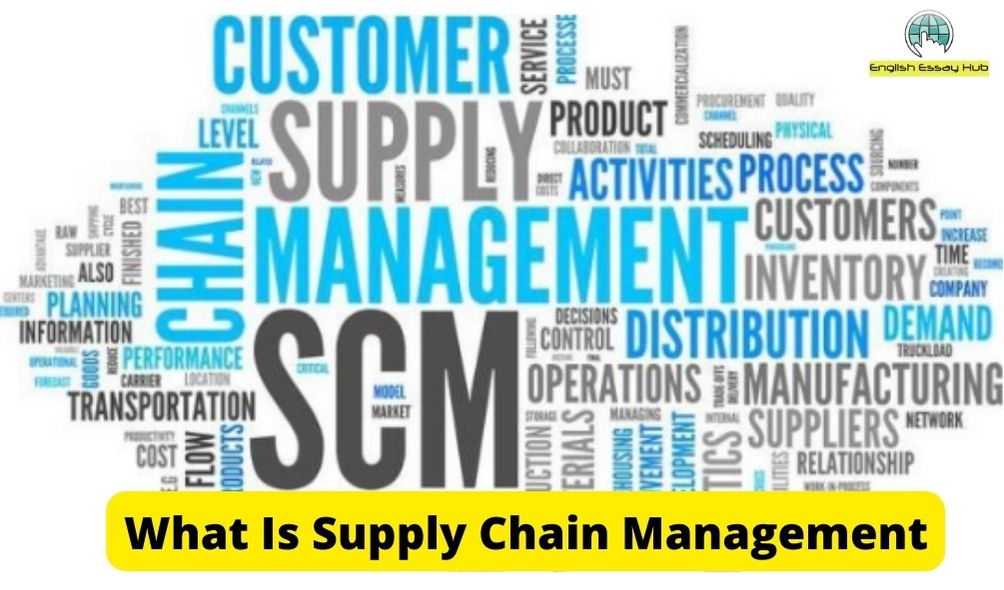
The inherent directionality of supply network networks is not captured by a business flow metric. A supply network is often composed of many levels and dependencies. A business flow metric does not capture the intrinsic directionality of information flows within a network. Understanding and considering these issues is key to the creation of a digital supply net.
Sustainability
Multinational corporations must ensure that supply networks are sustainable. Many companies have made sustainability a priority and committed to using sustainable suppliers. There are serious risks for businesses if lower-ranking suppliers do not comply with sustainability standards. This article examines three major MNCs' supply networks. The authors found some best practices that companies could adopt to counter this problem. These include setting long-term sustainability goals and including lower-tier suppliers in the sustainability strategy.
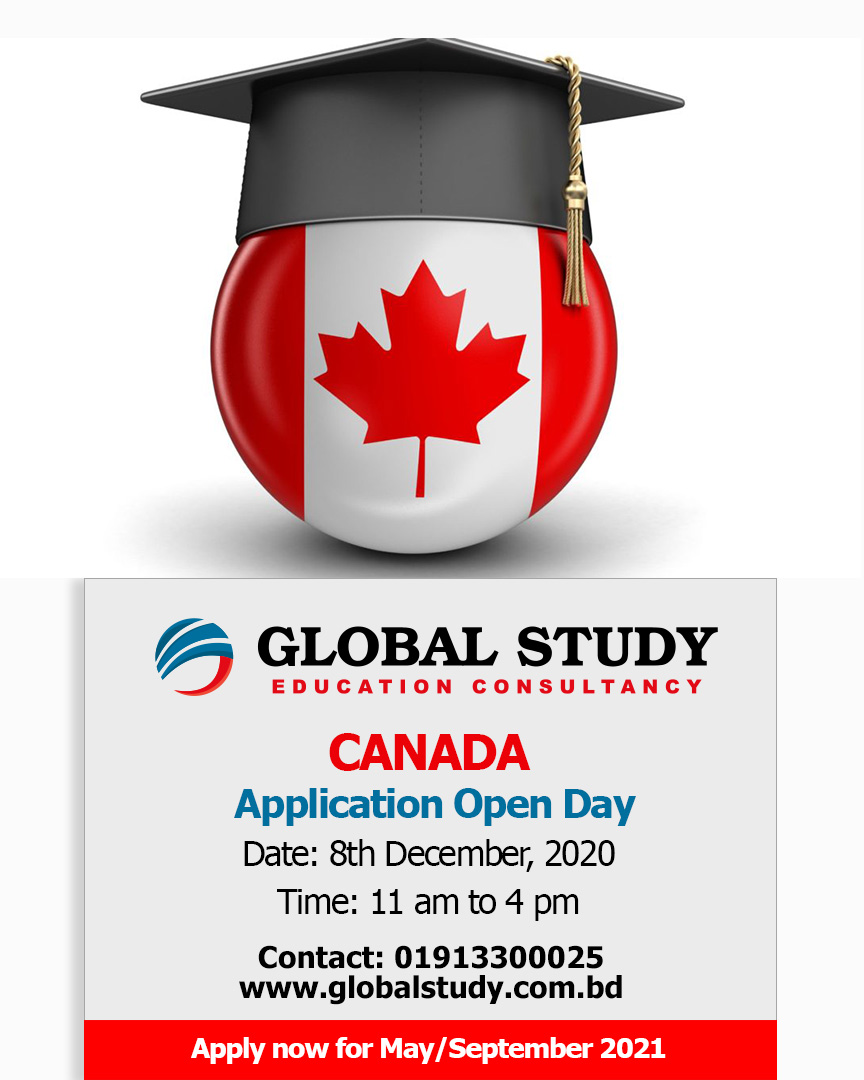
Companies must set targets and measure the progress they make in improving their supply chains. They should also be engaging all stakeholders, including internal staff and consumers. It is important to demonstrate the benefits of sustainable supply chains and to implement proper governance and organizational structures in order to make sustainability efforts a success.
Vertical disintegration supply chains
For firms, vertical disintegration of supply chain can have many negative consequences. This can result in higher costs and losses and may also cause changes to organisational structures and hierarchies. Companies may decide to reduce their involvement and participation in downstream or upstream activities in order to improve their overall competitiveness. This approach is not always the best and should be used only in certain circumstances.
Vertical integration has one major drawback: it restricts a company’s flexibility. Vertical integration forces a company to follow the trends in a specific segment. It may prove difficult for retailers to adopt new technology if their competition already uses it. If this were the case, the parent company would have to invest in the new technology to keep up with the competition. Rapidly changing technologies can make integration difficult. Companies face many challenges in integrating technologies from different parts their supply chains. This can lead to costly problems.
Performance implications of a digital supply network
Digital supply chains can have many benefits. They are more efficient, resilient, and cost-savings. However, they can also increase cybersecurity risk. However, there are many options companies have to minimize these risks. Let's take a look at some of them. These methods are based on data analytics. This technology allows businesses to understand customer expectations and can improve their products or services. Companies can also use shared data from different sources to predict possible problems and make better, informed decisions.
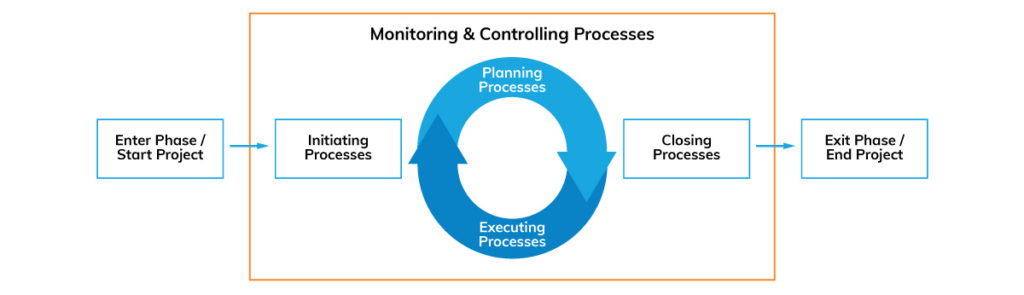
Assessing your existing supply chains is the first step to implementing digitalization. This will enable you to understand the risks and potential problems in your supply chain. You can then create an action plan to reduce any potential risks. Collaborating with your partners once you have a clear understanding of the goals that you are trying to achieve via the digital supply network is key. You will be able to make sure that everyone benefits from the new digital supply system.
FAQ
What is the difference in Six Sigma and TQM?
The major difference between the two tools for quality management is that six Sigma focuses on eliminating defect while total quality control (TQM), on improving processes and decreasing costs.
Six Sigma is a method for continuous improvement. This method emphasizes eliminating defects using statistical methods such p-charts, control charts, and Pareto analysis.
This method has the goal to reduce variation of product output. This is achieved by identifying and addressing the root causes of problems.
Total quality management includes monitoring and measuring all aspects of an organization's performance. It also involves training employees to improve performance.
It is frequently used as an approach to increasing productivity.
What are some common mistakes managers make when managing people?
Managers can make their jobs more difficult than necessary.
They may not be able to delegate enough responsibility to staff or provide adequate support.
Many managers lack the communication skills to motivate and lead their employees.
Some managers set unrealistic expectations for their staff.
Managers might try to solve every problem by themselves rather than delegating the responsibility.
What is Six Sigma?
It's a method for quality improvement that focuses on customer service as well as continuous learning. The goal is to eliminate defects by using statistical techniques.
Motorola created Six Sigma as part of their efforts to improve manufacturing processes in 1986.
The idea spread quickly in the industry. Today many organizations use six-sigma techniques to improve product design.
What are the key management skills?
Business owners need to have management skills, no matter how small or large they may be. These skills include the ability of managing people, finances, time, space, and other factors.
These skills are necessary for setting goals and objectives as well as planning strategies, leading groups, motivating employees and solving problems.
You can see that there are many managerial duties.
What is Kaizen?
Kaizen is a Japanese term meaning "continuous improvement." It is a philosophy that encourages employees to constantly look for ways to improve their work environment.
Kaizen is based upon the belief that each person should be capable of doing his or her job well.
Statistics
- UpCounsel accepts only the top 5 percent of lawyers on its site. (upcounsel.com)
- Your choice in Step 5 may very likely be the same or similar to the alternative you placed at the top of your list at the end of Step 4. (umassd.edu)
- Hire the top business lawyers and save up to 60% on legal fees (upcounsel.com)
- 100% of the courses are offered online, and no campus visits are required — a big time-saver for you. (online.uc.edu)
- As of 2020, personal bankers or tellers make an average of $32,620 per year, according to the BLS. (wgu.edu)
External Links
How To
How do you implement a Quality Management Plan (QMP)?
QMP (Quality Management Plan), introduced in ISO 9001,2008, provides a systematic method for improving processes, products, or services through continuous improvement. It helps to improve customer satisfaction and product/service quality by continuously measuring, analyzing, controlling and improving.
QMP is a common method to ensure business performance. QMP's goal is to improve service delivery and production. QMPs should encompass all three components - Products and Services, as well as Processes. If the QMP only covers one aspect, it's called a "Process QMP". QMPs that focus on a Product/Service are known as "Product" QMPs. And when the QMP concentrates on Customer Relationships, it is called "Customer" QMP.
Scope, Strategy and the Implementation of a QMP are the two major elements. These are the following:
Scope is what the QMP covers and how long it will last. This scope can be used to determine activities for the first six-months of implementation of a QMP in your company.
Strategy: This is the description of the steps taken to achieve goals.
A typical QMP is composed of five phases: Planning Design, Development, Implementation and Maintenance. Each phase is described below:
Planning: This stage identifies and prioritizes the QMP's objectives. In order to fully understand and meet the needs of all stakeholders involved in this project, they are consulted. Next, you will need to identify the objectives and priorities. The strategy for achieving them is developed.
Design: The design stage involves the development of vision, mission strategies, tactics, and strategies that will allow for successful implementation. These strategies are then put into practice by creating detailed plans.
Development: This is where the development team works to build the capabilities and resources necessary for the successful implementation of the QMP.
Implementation: This is the actual implementation and use of the QMP's planned strategies.
Maintenance: The maintenance of the QMP is an ongoing task.
The QMP must also include several other items:
Stakeholder Engagement: It is crucial for the QMP to be a success. They need to be actively involved in the planning, design, development, implementation, and maintenance stages of the QMP.
Project Initiation. It is important to understand the problem and the solution in order to initiate any project. The initiator must know the reason they are doing something and the expected outcome.
Time Frame: The time frame of the QMP is very critical. The simplest version can be used if the QMP is only being implemented for a short time. If you are looking for a longer-term commitment, however, you might need more complex versions.
Cost Estimation. Cost estimation is another crucial component of QMP. Without knowing how much you will spend, planning is impossible. Therefore, cost estimation is essential before starting the QMP.
QMPs are not just a written document. They should be a living document. It can change as the company grows or changes. It should be reviewed on a regular basis to ensure that it is still meeting the company's needs.