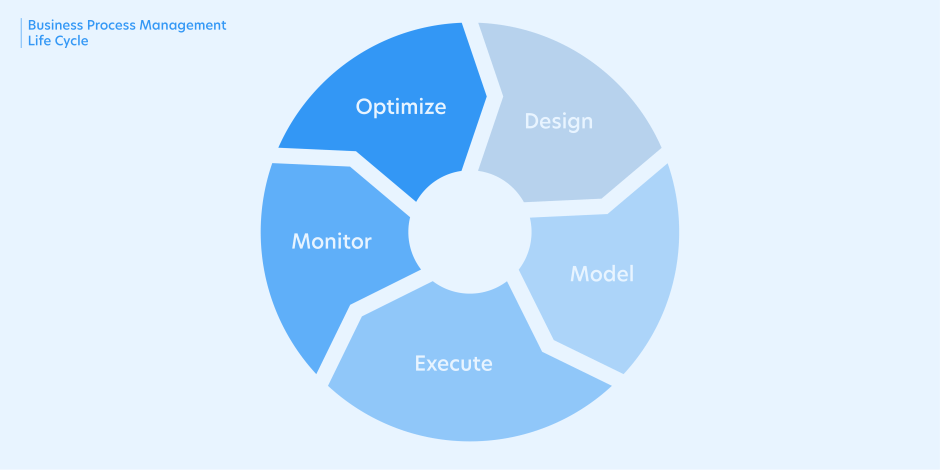
A ISO document has a number rules that are essential for understanding. A document ISO must contain abbreviations that are precise and clear. You should avoid certain types of punctuation. These include symbols for quantities or forms of language. These guidelines make it easier for readers to understand the ISO document and its contents.
Formulas
Implementing electronic ISO document forms can boost your company's quality processes, regulatory compliance, and customer satisfaction. Remember to keep these forms simple, break them down into data types, and ensure they are part or a larger process. Agile development is key. It is helpful to collect user requirements early on. User testing can also be useful as it can uncover issues you did not anticipate. In addition, you should provide all users with software-specific training.
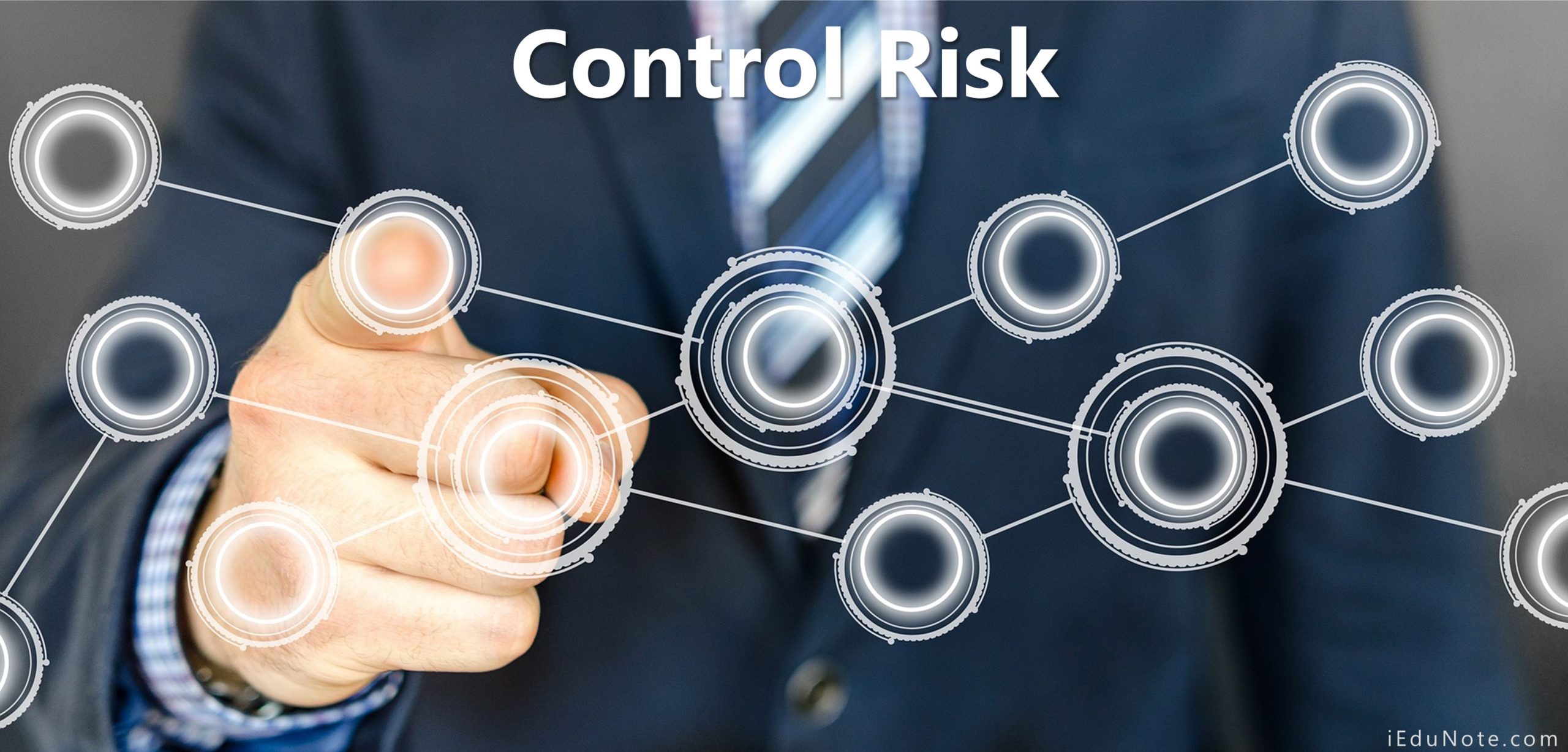
Symbols for quantities
The symbols used to represent quantities in ISO documents are abbreviated terms. These symbols are commonly abbreviated terms. They are typically written in italics unlike numbers and words that are written in lowercase. Some abbreviations may also have special meanings. The standard also provides guidelines for the types of symbols that can be used to indicate quantities.
Acronyms
You've probably come across some common acronyms if you read ISO documents often. The first acronym is CAR (Corrective Action Request). The corrective action (CA) refers to the activity that generates it. This is typically the investigation of a problem to identify its root cause, and prevent its recurrence. This can be used to describe the entire Corrective Action cycle.
Language
Language of ISO document is critical in ensuring the document is understood and understood by intended audience. The conventions that are used to define this language are listed below. Although abbreviations may be used in common usage, it is important that the first word of each term be capitalized. For radio frequency, however, it is not acceptable to use the abbreviation d.c.
Formatting
Documentation is an essential aspect of ISO standards. However, some organizations overdocument, creating an inflexible system. To avoid this problem, ensure your documentation follows the correct structure and style.
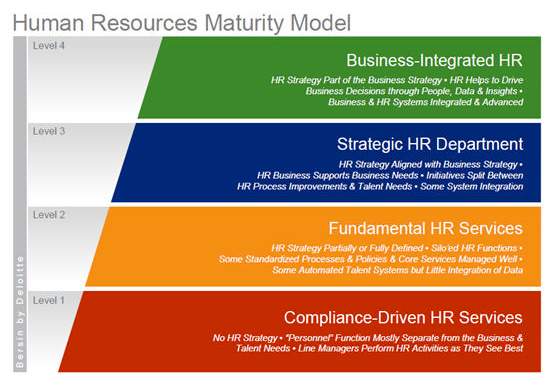
Publishing
ISO publishes documents in different formats. ISO documents are known as IEC standards and ISO standards. They were created by the American Society for Testing and Materials and ISO/IEC JTC 1. ISO standards can differ from ASTM standards. Some standards are not complete and are not published. This means that the publication title often does not include their name.
FAQ
What is a management tool to help with decision-making?
The decision matrix is a powerful tool that managers can use to help them make decisions. It allows them to consider all possible solutions.
A decision matrix represents alternatives in rows and columns. This allows you to easily see how each choice affects others.
This example shows four options, each represented by the boxes on either side of the matrix. Each box represents an option. The top row displays the current situation, and the bottom row shows what might happen if nothing is done.
The effect of Option 1 can be seen in the middle column. In this example, it would lead to an increase in sales of between $2 million and $3 million.
These are the results of selecting Options 2 or 3. These are both positive changes that increase sales by $1million and $500,000. These positive changes have their downsides. For instance, Option 2 increases cost by $100 thousand while Option 3 reduces profits by $200 thousand.
The final column shows results of choosing Option 4. This results in a decrease of sales by $1,000,000
The best part of using a decision-matrix is that it doesn't require you to know which numbers belong where. The best thing about a decision matrix is that you can simply look at the cells, and immediately know whether one option is better or not.
The matrix already does all the work. It is as simple a matter of comparing all the numbers in each cell.
Here is an example of how a decision matrix might be used in your business.
It is up to you to decide whether to spend more money on advertising. This will allow you to increase your revenue by $5000 per month. However, this will mean that you'll have additional expenses of $10,000.
By looking at the cell just below "Advertising", the net result can be calculated as $15 thousand. Advertising is worth more than its cost.
What are the four major functions of Management?
Management is responsible for planning, organizing, directing, and controlling people and resources. It also includes developing policies and procedures and setting goals.
Management aids an organization in reaching its goals by providing direction and coordination, control, leadership motivation, supervision, training, evaluation, and leadership.
These are the four major functions of management:
Planning - Planning is about determining what must be done.
Organizing: Organizing refers to deciding how things should work.
Directing – This means to get people to follow directions.
Controlling – This refers to ensuring that tasks are carried out according to plan.
How do you define Six Sigma?
Six-sigma will be well-known to anyone who has worked in operations research or statistics. But anyone can benefit from it.
Because it requires a high level of commitment, only those with strong leadership skills will make an effort necessary to implement it successfully.
What is the difference between Six Sigma Six Sigma and TQM?
The major difference between the two tools for quality management is that six Sigma focuses on eliminating defect while total quality control (TQM), on improving processes and decreasing costs.
Six Sigma is a methodology for continuous improvement. It emphasizes the elimination of defects by using statistical methods such as control charts, p-charts, and Pareto analysis.
This method attempts to reduce variations in product output. This is achieved by identifying and addressing the root causes of problems.
Total quality management refers to the monitoring and measurement of all aspects in an organization. It also involves training employees to improve performance.
It is used to increase productivity.
What are the five management process?
Each business has five stages: planning, execution and monitoring.
Setting goals for the future is part of planning. Planning includes setting goals for the future.
Execution happens when you actually do the plan. You need to make sure they're followed by everyone involved.
Monitoring is the process of evaluating your progress toward achieving your objectives. Monitoring should include regular reviews of performance against goals and budgets.
At the end of every year, reviews take place. They give you an opportunity to review the year and assess how it went. If not then, you can make changes to improve your performance next year.
After the annual review, evaluation takes place. It helps to determine what worked and what didn’t. It also provides feedback regarding how people performed.
Statistics
- 100% of the courses are offered online, and no campus visits are required — a big time-saver for you. (online.uc.edu)
- As of 2020, personal bankers or tellers make an average of $32,620 per year, according to the BLS. (wgu.edu)
- Hire the top business lawyers and save up to 60% on legal fees (upcounsel.com)
- This field is expected to grow about 7% by 2028, a bit faster than the national average for job growth. (wgu.edu)
- Your choice in Step 5 may very likely be the same or similar to the alternative you placed at the top of your list at the end of Step 4. (umassd.edu)
External Links
How To
How does Lean Manufacturing work?
Lean Manufacturing processes are used to reduce waste and improve efficiency through structured methods. They were created in Japan by Toyota Motor Corporation during the 1980s. The goal was to produce quality products at lower cost. Lean manufacturing is about eliminating redundant steps and activities from the manufacturing process. It has five components: continuous improvement and pull systems; just-in time; continuous change; and kaizen (continuous innovation). The production of only what the customer needs without extra work is called pull systems. Continuous improvement means continuously improving on existing processes. Just-in-time is when components and other materials are delivered at their destination in a timely manner. Kaizen means continuous improvement, which is achieved by implementing small changes continuously. Fifth, the 5S stand for sort, set up in order to shine, standardize, maintain, and standardize. These five elements work together to produce the best results.
Lean Production System
Six key concepts form the foundation of the lean production system:
-
Flow is about moving material and information as near as customers can.
-
Value stream mapping - Break down each stage in a process into distinct tasks and create an overview of the whole process.
-
Five S’s - Sorted, In Order. Shine. Standardize. And Sustain.
-
Kanban: Use visual signals such stickers, colored tape, or any other visual cues, to keep track your inventory.
-
Theory of constraints: Identify bottlenecks and use lean tools such as kanban boards to eliminate them.
-
Just-in-time - deliver components and materials directly to the point of use;
-
Continuous improvement - make incremental improvements to the process rather than overhauling it all at once.