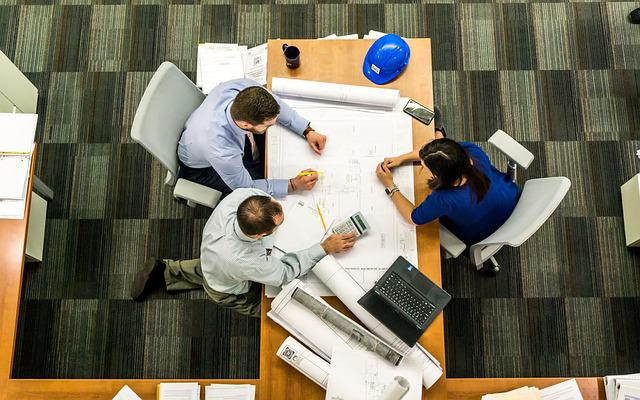
This article will cover the core activities of the value chains. These activities include the supply, sale and production of raw materials and the management or employees. All of these activities have a significant impact on any business. Each activity will be covered in greater detail in the next sections. You can learn more about each by reading the definitions. The purchase of raw material, such as wood or metal, for a firm's value chain is called procurement.
Operation
Operations is the transformation of inputs into finished goods. It is often associated with production, especially for industries that produce physical goods. However, it can also refer to services. Operations may, for example, require raw materials or labor in order manufacture a finished product. Operation may be required for service-based businesses. This could include maintaining inventory or providing administrative services. This phase has the primary purpose of creating value.
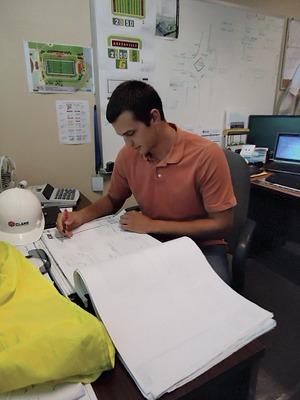
Sales
It is an essential part of a value chain. It involves both the selling and purchasing of a product. The company develops a product and then markets it. Finally, they close sales. The value chain includes all of these activities. For a company to succeed, sales and marketing are essential. These are vital for a company's success in increasing its market value and revenue as well as its profits. Identifying each activity and its raw materials is essential to assessing the value chain.
Marketing
After-sales is the most important aspect of a company's promotion and marketing. Customers can express dissatisfaction online about any product purchased via an e-commerce site or traditional manufacturer. The consequences can be severe. Therefore, a company must establish the right after-sales service practices. These activities include product adjustments, repair, maintenance, training, parts supply and installation.
Distribution
Distribution of goods, and services, is one of the key activities of a value chains. The value of a service or good can be affected by many factors. One of these factors is the price. Consumers are more willing to pay more for finished goods that they are for raw materials. Innovations and unique items can improve a company's perceived value. This perception can have a major impact on the margins and profitability of a product.
Infrastructure
Infrastructure is the core of a value-chain. It supports top-level business decisions like finance, compliance, quality control, and compliance. An effective strategic infrastructure combines these activities and provides the necessary coordination to effectively manage all aspects of the value chain. The following are some examples of strategic infrastructure. It can be a competitive advantage to invest in it. In addition to financial management, strategic infrastructure can also help a business reduce costs of technology.
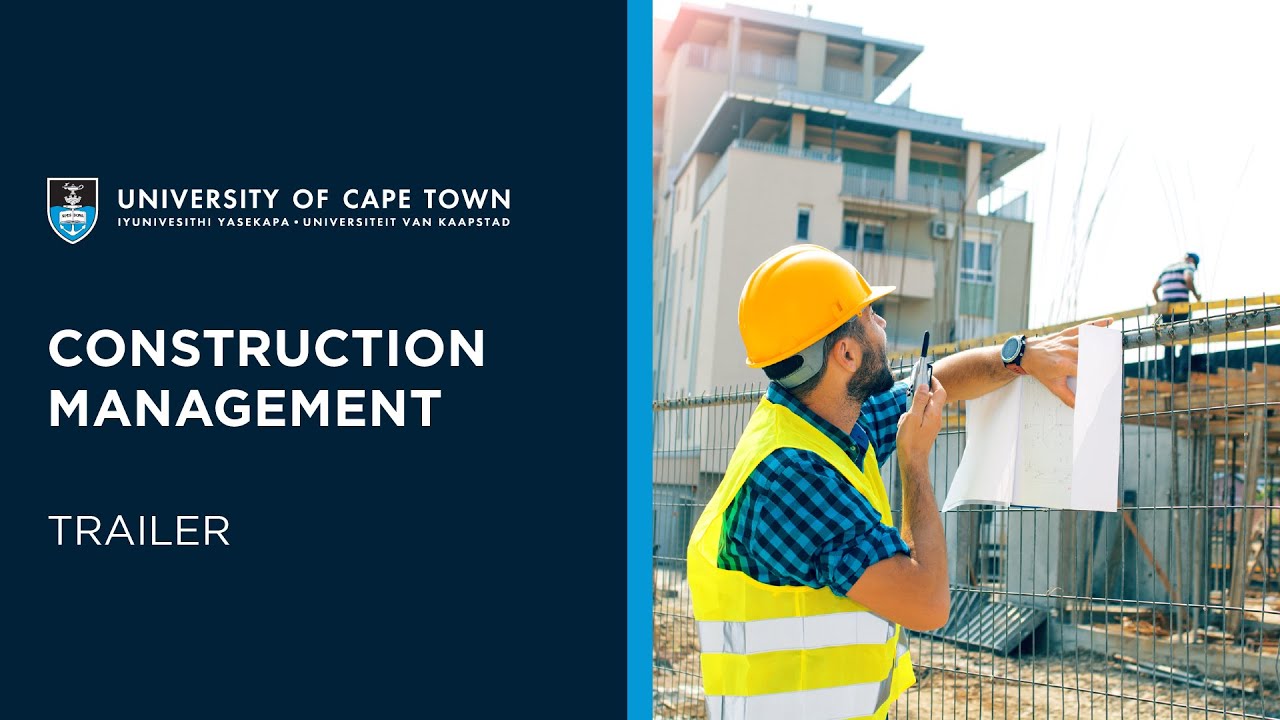
Customer service
Customer service is just the same as promotional activities for your products. If customers are unhappy with the products or services they receive, it is possible to be sure that other customers will also be complaining. The consequences could be severe. That's why it is important for any company to implement the right customer service practices. After-sales support activities include product adjustments and repair.
FAQ
How does a manager motivate his/her employees?
Motivation is the desire to do well.
Enjoyable activities can motivate you.
Another way to get motivated is to see yourself as a contributor to the success of the company.
If you are a doctor and want to be one, it will likely be more rewarding to see patients than to read medical books every day.
Another source of motivation is within.
You might feel a strong sense for responsibility and want to help others.
Or you might enjoy working hard.
Ask yourself why you feel so motivated.
Then think about how you can make your life more motivating.
What are the 5 management processes?
The five stages of a business include planning, execution (monitoring), review, evaluation, and review.
Setting goals for the future is part of planning. Planning includes setting goals for the future.
Execution takes place when you actually implement the plans. You need to make sure they're followed by everyone involved.
Monitoring allows you to monitor your progress towards achieving your goals. Regular reviews of performance against targets, budgets, and other goals should be part.
Reviews take place at the end of each year. They give you an opportunity to review the year and assess how it went. If not, then it may be possible to make adjustments in order to improve performance next time.
Evaluation takes place after the annual review. It helps you identify the successes and failures. It also provides feedback regarding how people performed.
How do you define Six Sigma?
Six Sigma is well-known to those who have worked in operations research and statistics. However, anyone involved in any aspect of business can benefit from using it.
Because it requires a high level of commitment, only those with strong leadership skills will make an effort necessary to implement it successfully.
What is Kaizen?
Kaizen is a Japanese term meaning "continuous improvement." It is a philosophy that encourages employees to constantly look for ways to improve their work environment.
Kaizen is based upon the belief that each person should be capable of doing his or her job well.
How can a manager improve his/her managerial skills?
Through demonstrating good management skills at every opportunity
Managers must constantly monitor the performance of their subordinates.
You must quickly take action if your subordinate fails to perform.
You should be able to identify what needs improvement and how to improve things.
Statistics
- The profession is expected to grow 7% by 2028, a bit faster than the national average. (wgu.edu)
- Hire the top business lawyers and save up to 60% on legal fees (upcounsel.com)
- As of 2020, personal bankers or tellers make an average of $32,620 per year, according to the BLS. (wgu.edu)
- UpCounsel accepts only the top 5 percent of lawyers on its site. (upcounsel.com)
- The average salary for financial advisors in 2021 is around $60,000 per year, with the top 10% of the profession making more than $111,000 per year. (wgu.edu)
External Links
How To
How do you apply the Kaizen method to your life?
Kaizen means continuous improvement. This Japanese term refers to the Japanese philosophy of continuous improvement that emphasizes incremental improvements and constant improvement. It's a team effort to continuously improve processes.
Kaizen is one of Lean Manufacturing's most efficient methods. Kaizen is a concept where employees in charge of the production line are required to spot problems during the manufacturing process before they become major issues. This way, the quality of products increases, and the cost decreases.
Kaizen is about making everyone aware of the world around them. If something is wrong, it should be corrected immediately so that no problem occurs. If someone spots a problem while at work, they should immediately report it to their manager.
Kaizen is based on a few principles. We always start from the end product and move toward the beginning. To improve our factory, for example, we need to fix the machines that produce the final product. Then, we fix the machines that produce components and then the ones that produce raw materials. We then fix the workers that work with those machines.
This method, called 'kaizen', focuses on improving each and every step of the process. After we're done with the factory, it's time to go back and fix the problem.
It is important to understand how to measure the effectiveness and implementation of kaizen in your company. There are many methods to assess if kaizen works well. One of these ways is to check the number of defects found on the finished products. Another way is to check how much productivity has grown since kaizen was implemented.
A good way to determine whether kaizen has been implemented is to ask why. Did you do it because it was legal or to save money? You really believed it would make you successful?
Congratulations if you answered "yes" to any of the questions. You're ready to start kaizen.