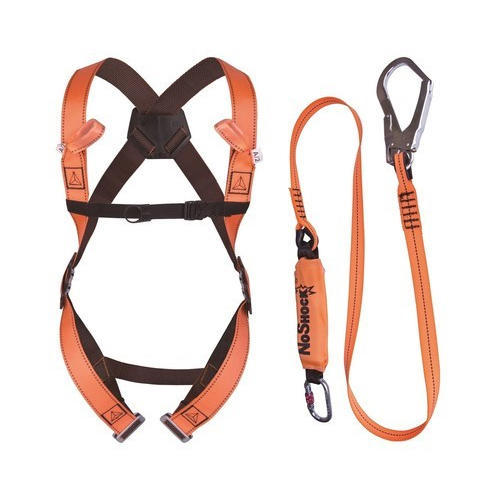
It is important to manage change in project management. But it can be difficult. It can take time and drain resources. It is best to think of change management as a continuous evaluation and process. Spreadsheets can be used to help teams track their processes. If the change is significant, it should be managed like a project. Change management can improve communication, knowledge and overall organizational performance.
Change management is the application a systematic process and set o tools for leading people through change
Project management includes the management of the people aspect of change. Projects that are not managed effectively will face difficulties and may fall apart. Change management is an important aspect of project management. It should be closely integrated with project management. Its goal is to create a smooth transition and minimize stress for stakeholders.
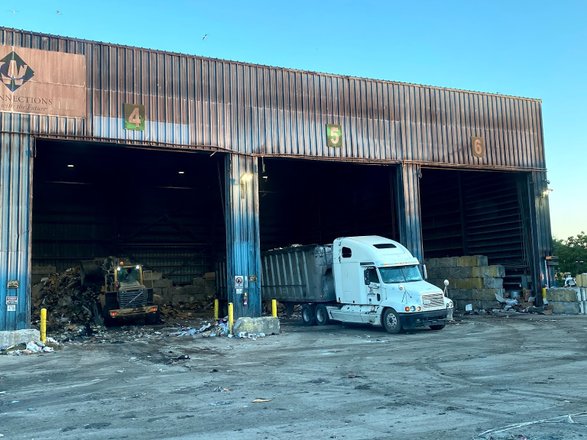
It improves communication and knowledge within the project
A successful project will be one that improves communication and knowledge in the process of project management. Ineffective communications are the root of many failed projects. Ineffective communication can result in companies spending $135million per project, according to research. Inefficient communication increases these costs by $75M. Ineffective communication can be a major problem that companies need to address on an organizational level. Project teams communicate via email and spreadsheets. This can lead to communication gaps. Team members might also need to manually modify spreadsheets or boards to communicate with clients.
It improves organizational success
In digital transformation, the role of managing change is crucial. The process involves a wide range of projects, and many of these have an impact on the overall organization. The role of change management is critical for managing these projects, as they often involve many different people. Identifying and addressing the factors that affect change is an important first step. This process involves considering the impact of change on the people, culture, systems, and structures of an organization. In the process, the organization is better positioned for future success.
It reduces motivational force toward change
This article describes the factors that lead project managers to be impatient and resist change. These factors are interrelated, and can be addressed together. Each factor can be improved by improving one. One example is that increasing motivation in one area will result in increased motivation in all three. This research is important for project management because it can improve the performance and efficiency of the entire group.
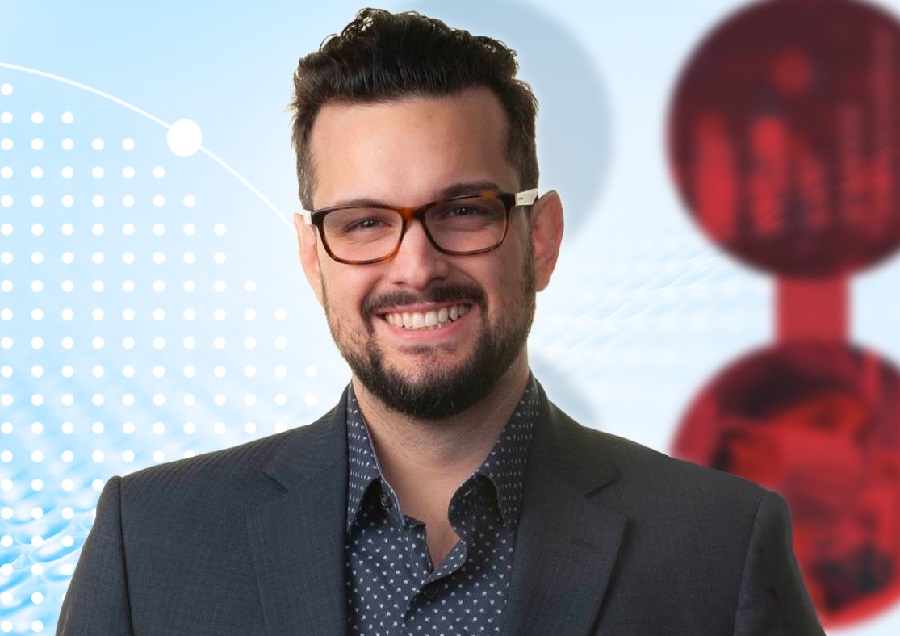
It improves communication
Good communication is the key to successfully managing change in project leadership. Communication is key to managing change, fostering cooperation, belonging and improving team morale. This will ensure that the team is fully informed about the project's goals and can meet the challenge. Listening and asking questions will help you to gain a better understanding of the opinions and concerns of team members. You will also be able to better understand the goals and objectives of your project by communicating.
FAQ
Why is Six Sigma so popular?
Six Sigma is easy and can deliver significant results. It can also be used to help companies identify and focus on the most important aspects of their business.
What is the main difference between Six Sigma Six Sigma TQM and Six Sigma Six Sigma?
The main difference between these two quality management tools is that six sigma focuses on eliminating defects while total quality management (TQM) focuses on improving processes and reducing costs.
Six Sigma is a methodology for continuous improvement. It emphasizes the elimination of defects by using statistical methods such as control charts, p-charts, and Pareto analysis.
This method seeks to decrease variation in product output. This is done by identifying and correcting the root causes of problems.
Total quality management is the measurement and monitoring of all aspects within an organization. It also includes training employees to improve performance.
It is often used to increase productivity.
How to effectively manage employees
Effectively managing employees requires that you ensure their happiness and productivity.
It also means having clear expectations of their behavior and keeping track of their performance.
Managers must set clear goals for their employees and themselves to achieve this goal.
They need to communicate clearly with staff members. They should also ensure that they both reward high performers and discipline those who are not performing to their standards.
They must also keep track of the activities of their team. These include:
-
What was the result?
-
How much work was put in?
-
Who did it?
-
What was the moment it was completed?
-
Why did it happen?
This information is useful for monitoring performance and evaluating the results.
What is the meaning of "project management?"
This refers to managing all activities that are involved in a project's execution.
This includes defining the scope, identifying the requirements and preparing the budget. We also organize the project team, schedule the work, monitor progress, evaluate results, and close the project.
Why does it sometimes seem so difficult to make good business decisions?
Complex business systems have many moving parts. People who manage them have to balance multiple priorities while dealing with complexity and uncertainty.
The key to making good decisions is to understand how these factors affect the system as a whole.
You need to be clear about the roles and responsibilities of each system. It's important to also consider how they interact with each other.
You should also ask yourself if there are any hidden assumptions behind how you've been doing things. If they don't, you may want to reconsider them.
You can always ask someone for help if you still have questions after all of this. You may be able to see things from a different perspective than you are and gain insight that can help you find a solution.
What are the 5 management processes?
Each business has five stages: planning, execution and monitoring.
Setting goals for the future is part of planning. This includes setting goals for the future and defining what you want.
Execution takes place when you actually implement the plans. These plans must be adhered to by everyone.
Monitoring is checking on progress towards achieving your objectives. Regular reviews of performance against targets, budgets, and other goals should be part.
Every year, there are reviews. These reviews allow you to evaluate whether the year was successful. If not, then it may be possible to make adjustments in order to improve performance next time.
After each year's review, evaluation occurs. It helps identify what worked well and what didn't. It also gives feedback on how well people did.
Statistics
- The average salary for financial advisors in 2021 is around $60,000 per year, with the top 10% of the profession making more than $111,000 per year. (wgu.edu)
- Our program is 100% engineered for your success. (online.uc.edu)
- Hire the top business lawyers and save up to 60% on legal fees (upcounsel.com)
- The profession is expected to grow 7% by 2028, a bit faster than the national average. (wgu.edu)
- As of 2020, personal bankers or tellers make an average of $32,620 per year, according to the BLS. (wgu.edu)
External Links
How To
What is Lean Manufacturing?
Lean Manufacturing processes are used to reduce waste and improve efficiency through structured methods. They were developed in Japan by Toyota Motor Corporation (in the 1980s). The main goal was to produce products at lower costs while maintaining quality. Lean manufacturing eliminates unnecessary steps and activities from a production process. It is composed of five fundamental elements: continuous improvement; pull systems, continuous improvements, just-in–time, kaizen, continuous change, and 5S. Pull systems are able to produce exactly what the customer requires without extra work. Continuous improvement is constantly improving upon existing processes. Just-intime refers the time components and materials arrive at the exact place where they are needed. Kaizen stands for continuous improvement. Kaizen can be described as a process of making small improvements continuously. Last but not least, 5S is for sort. These five elements can be combined to achieve the best possible results.
Lean Production System
Six key concepts make up the lean manufacturing system.
-
Flow - The focus is on moving information and material as close as possible to customers.
-
Value stream mapping is the ability to divide a process into smaller tasks, and then create a flowchart that shows the entire process.
-
Five S's: Sort, Shine Standardize, Sustain, Set In Order, Shine and Shine
-
Kanban: Use visual signals such stickers, colored tape, or any other visual cues, to keep track your inventory.
-
Theory of constraints - identify bottlenecks during the process and eliminate them with lean tools like Kanban boards.
-
Just-in-time delivery - Deliver components and materials right to your point of use.
-
Continuous improvement: Make incremental improvements to the process instead of overhauling it completely.