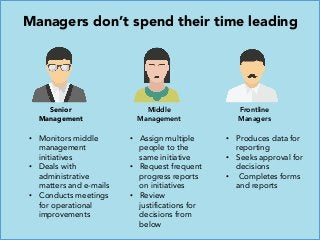
Employees should be involved in the change process. Ask employees for their input about the process and policy changes. Employees should be consulted about important decisions that affect their department or role. Employees get time to consider and evaluate new ideas. Employees will be more inclined to accept changes if they have a say in it. Involving employees in the development and implementation process of the new policy can also be beneficial. This article will describe the four phases of employee transition.
Four phases for employee change
The separation is the first phase of the process. This takes place within the first 0 to 3 months of the employee leaving the company. Either the employee, or the company, can initiate the separation process. The timing of the process can vary from company-to-company. Most companies require that employees inform them at least two week in advance of the intention to depart. This way, the company can prepare itself to handle the situation.
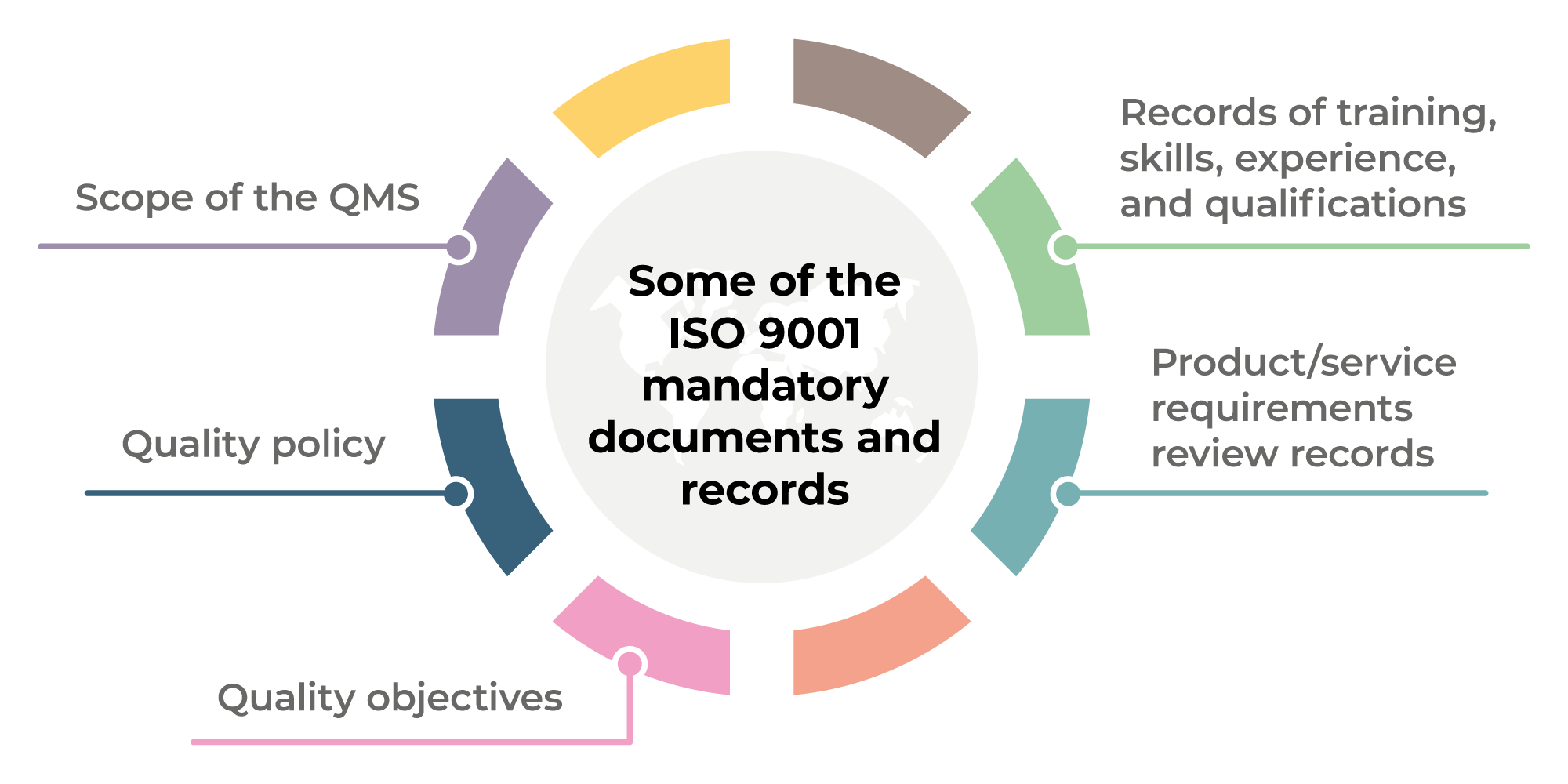
Communication
Communication of employee changes is an essential part of a successful management of change. It is important to communicate changes in a manner that will encourage employees to embrace new ways of working. Understanding the needs of your employees and the changes must be the basis for communication. Communication should be two-way and involve frequent, consistent communication. To ensure you reach all people, it is important to communicate with diverse audiences.
Empowerment
The use of technology and team-building activities can help to develop employees and foster engagement. It will help you create a more collaborative atmosphere by showing appreciation and connection to your employees. Also, create mentoring groups, idea exchanges and other ways to interact with other departments. Employees who feel empowered are more likely to take initiative in solving problems and contribute to the success of the company. How can you encourage your employees to take part?
Communication up-front
Effective change management begins with up-front communication. Explain the change and how it will affect the employee. To make sure employees are on board with the new direction, they need to be clear about what is happening. Communicate the changes clearly and in a simple way to avoid misunderstandings. Different audiences will receive the same message. Communicate about your new leadership if you're changing department heads. Communication is essential when restructuring a business.
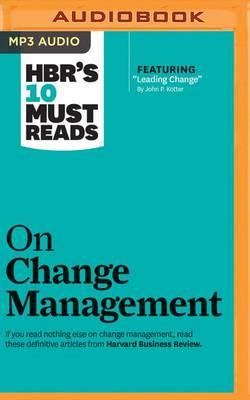
A supportive work environment
A supportive work environment is key to employee happiness. It can also increase the bottom line. Employees have human natures. Keeping them motivated can help them achieve their goals. On the other side, support is not just about motivation but also about the employee's overall health. Understanding what motivates people is crucial in order to support them.
FAQ
What is the meaning of "project management?"
This refers to managing all activities that are involved in a project's execution.
We include defining the scope of the project, identifying the requirements, preparing the budget, organizing the project team, scheduling the work, monitoring progress, evaluating results, and closing down the project.
What is the best way to motivate your employees as a manager?
Motivation is the desire for success.
Doing something that is enjoyable can help you get motivated.
Or you can get motivated by seeing yourself making a contribution to the success of the organization.
For example, if your goal is to become a physician, you will probably find it more motivational to see patients rather than to read a lot of medicine books.
Another type of motivation comes from within.
For example, you might have a strong sense of responsibility to help others.
You may even find it enjoyable to work hard.
Ask yourself why you feel so motivated.
You can then think of ways to improve your motivation.
How does Six Sigma function?
Six Sigma uses statistical analyses to locate problems, measure them, analyze root cause, fix problems and learn from the experience.
The first step is identifying the problem.
Next, data will be collected and analyzed to determine trends and patterns.
Next, corrective steps are taken to fix the problem.
The data are then reanalyzed to see if the problem is solved.
This continues until you solve the problem.
What kind people use Six Sigma?
People who have worked with statistics and operations research will usually be familiar with the concepts behind six sigma. It can be used by anyone in any business aspect.
Because it requires a high level of commitment, only those with strong leadership skills will make an effort necessary to implement it successfully.
Statistics
- As of 2020, personal bankers or tellers make an average of $32,620 per year, according to the BLS. (wgu.edu)
- Your choice in Step 5 may very likely be the same or similar to the alternative you placed at the top of your list at the end of Step 4. (umassd.edu)
- This field is expected to grow about 7% by 2028, a bit faster than the national average for job growth. (wgu.edu)
- 100% of the courses are offered online, and no campus visits are required — a big time-saver for you. (online.uc.edu)
- The profession is expected to grow 7% by 2028, a bit faster than the national average. (wgu.edu)
External Links
How To
How do you apply the Kaizen method to your life?
Kaizen means continuous improvement. The term was coined in the 1950s at Toyota Motor Corporation and refers to the Japanese philosophy emphasizing constant improvement through small incremental changes. It's a team effort to continuously improve processes.
Kaizen, a Lean Manufacturing method, is one of its most powerful. Kaizen is a concept where employees in charge of the production line are required to spot problems during the manufacturing process before they become major issues. This improves the quality of products, while reducing the cost.
Kaizen is the idea that every worker should be aware of what is going on around them. So that there is no problem, you should immediately correct it if something goes wrong. If someone is aware of a problem at work, he/she should inform his/her manager immediately.
Kaizen has a set of basic principles that we all follow. Start with the end product, and then move to the beginning. We can improve the factory by first fixing the machines that make it. First, we fix machines that produce components. Next, we fix machines that produce raw material. Then, we fix those who work directly with the machines.
This is why it's called "kaizen" because it works step-by-step to improve everything. Once we have finished fixing the factory, we return to the beginning and work until perfection.
Before you can implement kaizen into your business, it is necessary to learn how to measure its effectiveness. There are several ways that you can tell if your kaizen system is working. Another method is to see how many defects are found on the products. Another way to find out how productive your company has been since you implemented kaizen is to measure the increase in productivity.
Another way to know whether kaizen is working is to ask yourself why did you decide to implement kaizen. Did you do it because it was legal or to save money? You really believed it would make you successful?
If you answered yes to any one of these questions, congratulations! Now you're ready for kaizen.