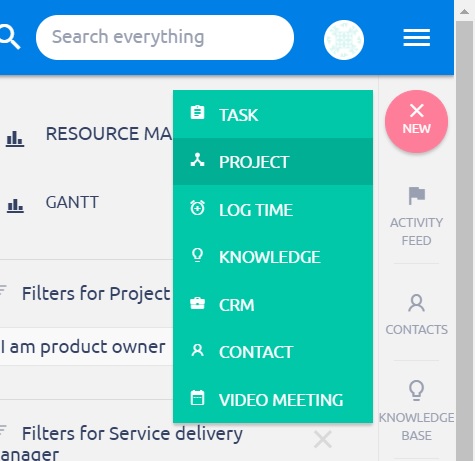
Here are some methods that you can use to reduce your carbon footprint as well as lower emissions in your supply chain. These include: Engaging stakeholders and managing sustainable procurement. This will allow you to create a more sustainable, predictable supply chain.
Engagement of stakeholders
Successful engagement with stakeholders is vital to the success of any company's sustainability efforts. Engaging stakeholders will help you speed up your sustainability journey. Companies can create a culture of collaboration and work effectively with multiple stakeholders by using robust engagement strategies. Engaging stakeholders will not only improve supply chain efficiency, but it will also help companies gain valuable insights regarding risks and opportunities.
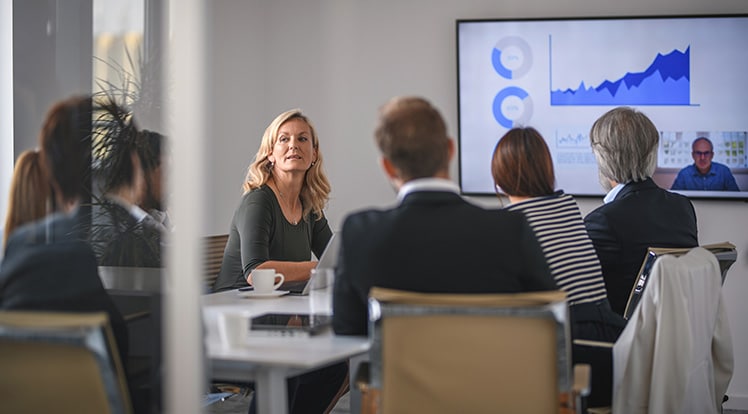
In order to engage stakeholders in a sustainable supply chain, companies should carefully select the metrics they are interested in tracking. When choosing metrics, it is important to consider the environmental and social aspects of a company. Environmental and social metrics can be difficult to measure for any company. Engagement can be difficult because many stakeholders might not know about the company's sustainability efforts.
Managing sustainable procurement
Any company must manage sustainable procurement. It is vital to ensure that the entire supply chain is transparent, and that tier 1 suppliers are held accountable for sustainable practices. Some organizations have difficulty implementing sustainable practices as they lack full visibility into the supply chain. A recent survey by EcoVadis revealed that only half of organizations had complete visibility into their supply chains, and that 28% did not have this kind of visibility at all. Although implementing sustainability measures can be difficult and take many years to implement, small wins such as auditing suppliers can help organizations get started.
In order to minimize risk and identify improvements, procurement teams should make sustainable procurement an integral part. They also need to ensure that customers are aware of the impacts of their purchases. However, to achieve true sustainability, organizations must go beyond the standard choices available to develop and implement new approaches to sustainable procurement. They must also work in new ways with suppliers, learn new skills, and ensure that they have the right data and information to achieve their goals.
Management of social responsibility
Every sustainable supply chain includes social responsibility (CSR). CSR principles need to be implemented at every stage in the supply chain. The environment must not be harmed by products and services provided by companies. This includes planning for the future, assessing product lifecycles, developing reuse strategies, and developing transportation capability. It is also important for companies to consider their customers' needs and to comply with government regulations.
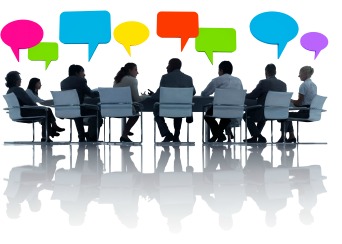
While sustainability refers to meeting current and future needs, it can also include economic, social, and environmental issues. Social responsibility is a commitment of a business to conduct business ethically, to benefit its workforce, local community, society, and the wider world.
FAQ
What role does a manager have in a company's success?
Managers' roles vary from industry to industry.
Managers generally oversee the day-today operations of a business.
He/she will ensure that the company fulfills its financial obligations.
He/she will ensure that employees follow all rules and regulations, and adhere to quality standards.
He/she plans and oversees marketing campaigns.
What are management concepts?
Management Concepts are the principles and practices managers use to manage people and resources. They cover topics like job descriptions (job descriptions), performance evaluations, training programmes, employee motivation and compensation systems.
What is TQM?
The industrial revolution was when companies realized that they couldn't compete on price alone. This is what sparked the quality movement. If they wanted to stay competitive, they needed to improve their quality and efficiency.
In response to this need for improvement, management developed Total Quality Management (TQM), which focused on improving all aspects of an organization's performance. It included continuous improvement and employee involvement as well as customer satisfaction.
How to effectively manage employees
Managing employees effectively means ensuring that they are happy and productive.
It also means having clear expectations of their behavior and keeping track of their performance.
Managers need to establish clear goals for their team and for themselves.
They need to communicate clearly and openly with staff members. They should also ensure that they both reward high performers and discipline those who are not performing to their standards.
They will also need to keep records about their team's activities. These include:
-
What was the result?
-
How much work was done?
-
Who did it and why?
-
Was it done?
-
Why?
This information can help you monitor your performance and to evaluate your results.
Statistics
- The average salary for financial advisors in 2021 is around $60,000 per year, with the top 10% of the profession making more than $111,000 per year. (wgu.edu)
- 100% of the courses are offered online, and no campus visits are required — a big time-saver for you. (online.uc.edu)
- Your choice in Step 5 may very likely be the same or similar to the alternative you placed at the top of your list at the end of Step 4. (umassd.edu)
- Hire the top business lawyers and save up to 60% on legal fees (upcounsel.com)
- This field is expected to grow about 7% by 2028, a bit faster than the national average for job growth. (wgu.edu)
External Links
How To
How is Lean Manufacturing done?
Lean Manufacturing techniques are used to reduce waste while increasing efficiency by using structured methods. They were developed in Japan by Toyota Motor Corporation (in the 1980s). It was designed to produce high-quality products at lower prices while maintaining their quality. Lean manufacturing focuses on eliminating unnecessary steps and activities from the production process. It is made up of five elements: continuous improvement, continuous improvement, just in-time, continuous change, and 5S. Pull systems involve producing only what the customer wants without any extra work. Continuous improvement involves constantly improving upon existing processes. Just-in time refers to components and materials being delivered right at the place they are needed. Kaizen means continuous improvement, which is achieved by implementing small changes continuously. The 5S acronym stands for sort in order, shine standardize and maintain. These five elements are combined to give you the best possible results.
Lean Production System
Six key concepts make up the lean manufacturing system.
-
Flow is about moving material and information as near as customers can.
-
Value stream mapping: This is a way to break down each stage into separate tasks and create a flowchart for the entire process.
-
Five S's, Sort, Set in Order, Shine. Standardize. and Sustain.
-
Kanban is a visual system that uses visual cues like stickers, colored tape or stickers to keep track and monitor inventory.
-
Theory of constraints - identify bottlenecks in the process and eliminate them using lean tools like kanban boards;
-
Just-in time - Get components and materials delivered right at the point of usage;
-
Continuous improvement is making incremental improvements to your process, rather than trying to overhaul it all at once.