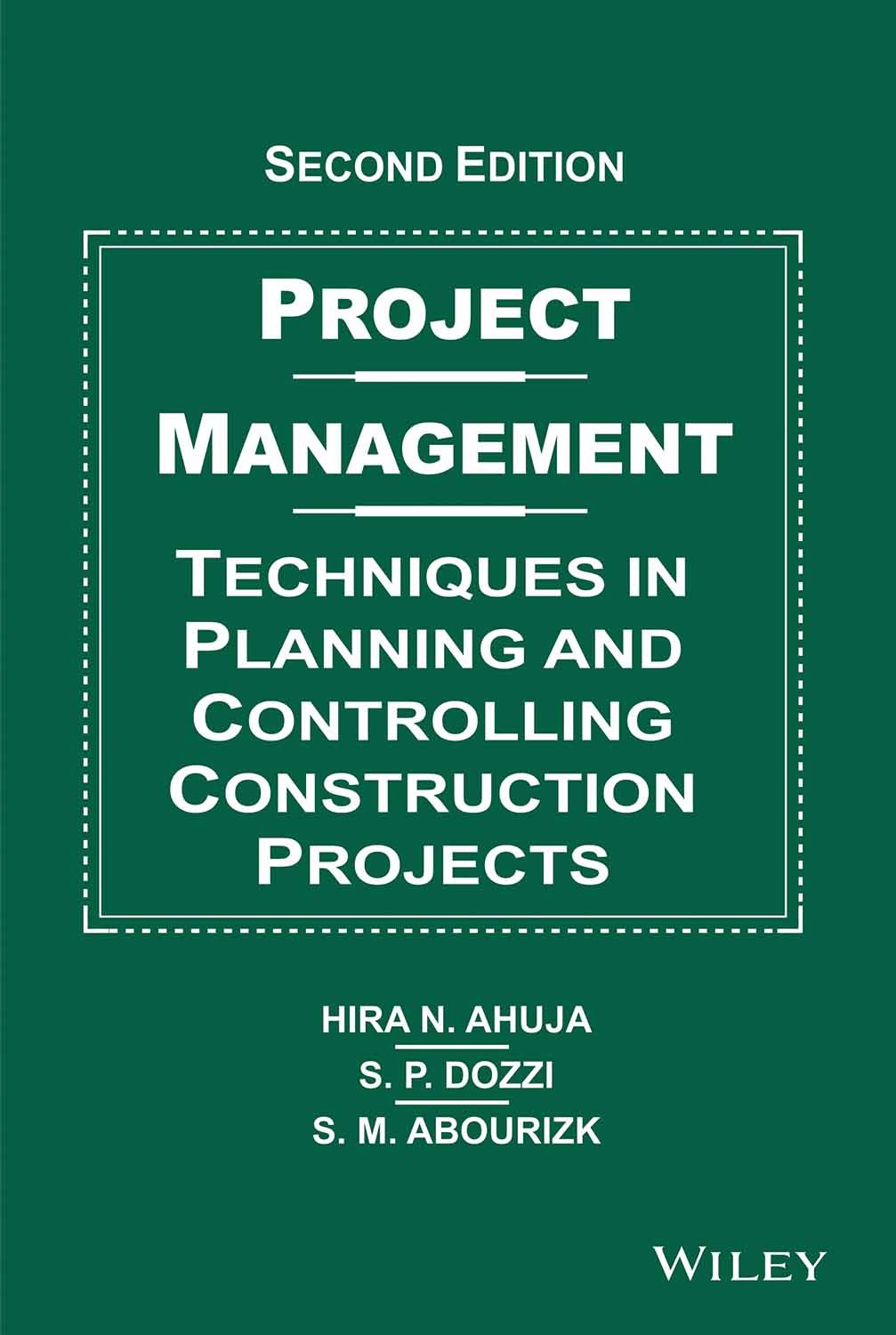
Inventory management involves the purchase, storage, use, packaging, and shipment of goods. It helps companies ensure they have enough finished goods to satisfy customer needs. It helps companies track buyer trends and improves time-to-market. Understanding how to use it effectively is key to inventory management success.
Inventory management is the act of purchasing, storing, using and packaging goods for shipping.
The key to running a business is inventory management. It is essential to running a successful company as it can prevent financial problems. It can be difficult to manage inventory, especially if there are multiple locations. It is possible to have multiple warehouses. You need to monitor stock levels at each location. Managing inventory can be time-consuming, but it is vital for your business's success.
There are many methods for managing inventory. One method is economic order number (EOQ). This measure takes into account both the total cost and consumer demand in order to determine the appropriate amount of inventory a company needs. The EOQ is a tool that can be used to help businesses remain profitable and make more cash.
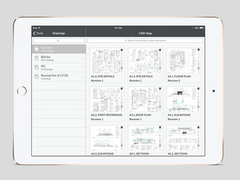
It assures that finished goods are always available
Companies that are able to manage their inventory effectively can be distinguished from their peers. It involves sorting out products and storing them according the demand. It may also involve cross docking or dropshipping. Software systems can be used to monitor inventory levels. With the right software system, a business can manage its stock levels so as to maximize inventory planning. Inventory management typically begins when customers place an order online or in-store.
Another type focuses on inventory management is the management of raw materials. These can either be purchased from another firm or made in house. This inventory can include products that are in the manufacturing process, such as nuts and screws, washers, or other parts. It may also include inventory in the process of manufacturing, such as parts needed for packaging finished goods or maintenance repairs. It can also include office supplies like paper or pencils.
It helps companies track buyer trends over the course of time.
Inventory management refers to the tracking of the stock items that a company has. This includes reviewing the data regularly to determine what stock to order and when to stock it. This is important because it helps companies identify patterns and trends in buyer behavior. This can also be used to identify shrinkage issues.
Inventory management also helps companies identify deadstock or obsolete products. These products are either no longer being purchased by customers or nearing their end of life. Inefficient warehouse organisation can also cause problems like inadequate signage, unsafe storage conditions, and insufficient walking space. An indicator of the frequency with which inventory is being replaced can be found in the inventory turnover ratio. The ITR will indicate how likely the company is sell its most inventory in a single cycle.
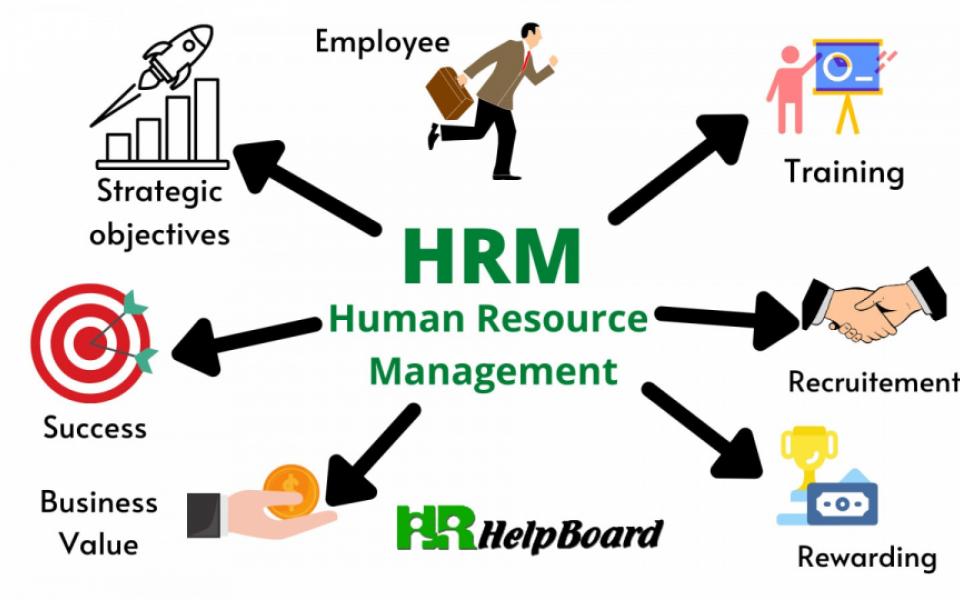
It speeds up the time it takes to get to market
Inventory management allows companies to ship items quicker and ensures that they have the right quantity at the right time. It reduces the possibility of missing stock items or cancelled orders. Stock outages can cause customers frustration. Inventory management can help prevent this.
Managing inventory is a critical component of any business, no matter its size. This complex process requires many decisions and considerations. Excel formulas might be used by small companies to keep track and determine reorder point stock. Enterprise resource planning software can be used for larger businesses. SaaS may also be a good option for large corporations.
FAQ
What does Six Sigma mean?
Six Sigma uses statistics to measure problems, find root causes, fix them, and learn from past mistakes.
The first step is to identify the problem.
The data is then analyzed and collected to identify trends.
Then corrective actions are taken to solve the problem.
The data are then reanalyzed to see if the problem is solved.
This continues until you solve the problem.
What are the 4 major functions of management
Management is responsible for planning, organizing, directing, and controlling people and resources. This includes setting goals, developing policies and procedures, and creating procedures.
Management is the ability to direct, coordinate, control, motivate, supervise, train, and evaluate an organization's efforts towards achieving its goals.
The four main functions of management are:
Planning - Planning is about determining what must be done.
Organizing - Organization involves deciding what should be done.
Directing - Directing is when you get people to do what you ask.
Controlling – Controlling is the process of ensuring that tasks are completed according to plan.
What are management principles?
Management concepts are the principles and practices used by managers to manage people, resources. These topics include job descriptions, performance evaluations and training programs. They also cover human resource policies, job description, job descriptions, job descriptions, employee motivation, compensation systems, organizational structures, and many other topics.
What are the 5 management processes?
The five stages of any business are planning, execution, monitoring, review, and evaluation.
Setting goals for the future is part of planning. Planning includes setting goals for the future.
Execution happens when you actually do the plan. It is important to ensure that everyone follows the plans.
Monitoring is checking on progress towards achieving your objectives. Regular reviews should be done of your performance against targets or budgets.
Each year, reviews are held at the end. They allow for an assessment of whether all went well throughout the year. If not then, you can make changes to improve your performance next year.
After each year's review, evaluation occurs. It helps identify what worked well and what didn't. It also provides feedback on the performance of people.
What is Six Sigma?
This is a method of quality improvement that emphasizes customer service, continuous learning, and customer service. This is an approach to quality improvement that uses statistical techniques to eliminate defects.
Motorola created Six Sigma as part of their efforts to improve manufacturing processes in 1986.
The idea spread quickly in the industry. Today many organizations use six-sigma techniques to improve product design.
Statistics
- Our program is 100% engineered for your success. (online.uc.edu)
- Hire the top business lawyers and save up to 60% on legal fees (upcounsel.com)
- The profession is expected to grow 7% by 2028, a bit faster than the national average. (wgu.edu)
- 100% of the courses are offered online, and no campus visits are required — a big time-saver for you. (online.uc.edu)
- This field is expected to grow about 7% by 2028, a bit faster than the national average for job growth. (wgu.edu)
External Links
How To
How do I get my Six Sigma license?
Six Sigma is a tool for quality management to improve processes and increase efficiency. It is a process that helps businesses achieve consistent results in their operations. Named after the Greek word for "sigmas", the name refers to the first two letters. Motorola developed this process in 1986. Motorola realized that it was important to standardize manufacturing processes so they could produce products quicker and cheaper. There were many people doing the work and they had difficulty achieving consistency. To overcome this problem they turned to statistical tools such control charts and Pareto analyses. They would then apply these techniques to all aspects of their operation. They would then be able make improvements where needed. There are three main steps to follow when trying to get your Six Sigma certification. To determine whether you are qualified, the first step is to verify your eligibility. You'll want to take some classes and pass them before you start taking any tests. Once you've passed those classes, you'll start taking the tests. You'll need to go back and review all the information you received in class. Then, you'll be ready to take the test. If you pass, then you will become certified. Finally, your certifications will be added to your resume.