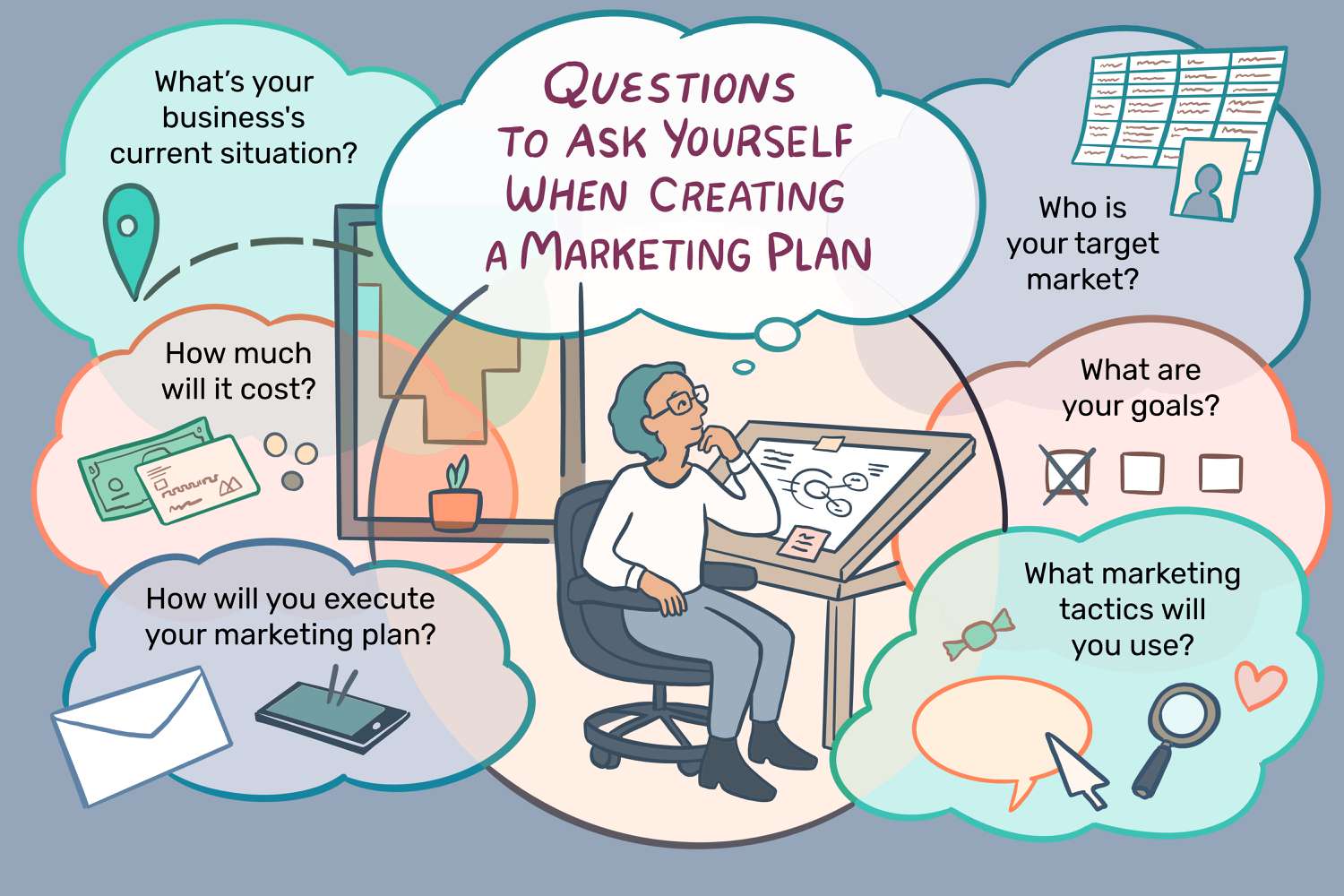
Good time management will help you break down your tasks into smaller pieces, prioritize them, and make them more manageable. You may have to modify or alter your strategy from time to time, just like any other strategy. Your strategies should be improved. There are always ways to improve your strategies, even if you run into roadblocks or limitations.
Pomodoro Technique
Pomodoro Technique may be a good option if you are looking for a better way to manage your time. Francesco Cirillo invented this method in the late 1980s. It breaks down work into 25 minutes intervals. This allows you to work for long periods and then take a quick break.
The Pomodoro Technique allows you to set a timer which will notify you when you need to take a break. It is a good way to prevent overworking. It allows you to prioritise tasks and breaks them into manageable segments.
Swiss Cheese Method
Swiss Cheese is a time-management technique that helps you break down big tasks into manageable pieces and gets things done. It's similar to cutting up a salami and breaking it into bite-sized pieces. People who are short on time might start by breaking up large projects into manageable pieces. This will help people manage their time better.
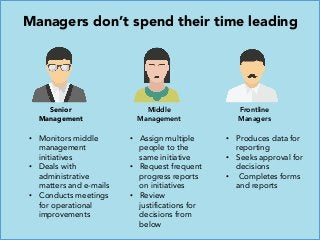
The Swiss Cheese method is great for large projects that are hard to manage. This method breaks down projects into smaller pieces, which allows you to map and plan your progress. You can mark off small successes to celebrate along the way. You can also keep track of the tasks and details you complete for the project.
80/20 rule
The 80/20 rule is a time management strategy that prioritizes your activities based only on the ones that will produce the best results. You shouldn't ignore tasks that produce less results. Focusing on tasks that produce the best quality and provide the most returns is a better way to go. This rule will allow you to achieve higher standards and more energy while working on your projects.
It's important to note that the 80/20 rule does not apply in all cases. It is a general principle, based upon the Pareto Principle. It says that 80 percent results are the result of 20 percent of the causes. This rule is widely used in teaching, design and marketing.
Breaking down tasks into smaller steps
It can be easier to manage your time by breaking down tasks into smaller pieces. Divide large tasks into small manageable steps so you can concentrate on each step, and finish them in a reasonable amount time. It can be particularly helpful to break down multiple tasks into smaller tasks. These tasks may be complicated or time-consuming, and a breakup strategy can make them seem much more manageable.
Clearly defining each task in task breakdown is the first step. Determine the time required for each step by defining it. Once you've identified the steps, you can put them into your calendar and schedule them accordingly.
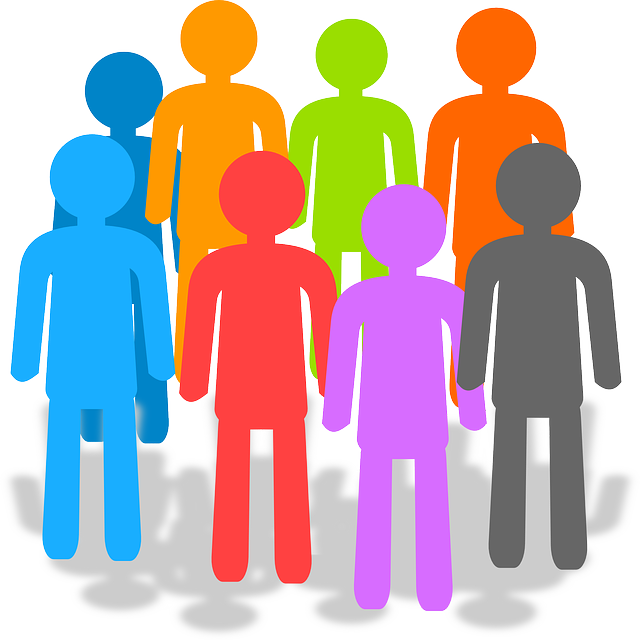
Taking regular breaks
Regular breaks are an essential part your daily life. They help you stay focused and sharp. A majority of bosses encourage their employees take frequent breaks. 86% agree that regular breaks improve their productivity. Breaks allow us to take a step back from our work and help us fight stress. You can take a break for as little as 10 minutes or as long as you want. It all depends on what you plan to do with your vacation time.
It is important to take regular breaks, but it is equally important to plan these breaks. You can even schedule each break with a time so that it's easy to remember when. Ideally, your breaks should last about 20 minutes or less, so that you can enjoy your time off.
FAQ
What is the difference in Six Sigma and TQM?
The main difference in these two quality management tools lies in the fact that six sigma is focused on eliminating defects and total quality management (TQM), emphasizes improving processes and reducing costs.
Six Sigma is an approach for continuous improvement. This approach emphasizes eliminating defects through statistical methods like control charts, Pareto analysis, and p-charts.
This method attempts to reduce variations in product output. This is achieved by identifying and addressing the root causes of problems.
Total quality management refers to the monitoring and measurement of all aspects in an organization. It also involves training employees to improve performance.
It is often used as a strategy to increase productivity.
What's the difference between leadership & management?
Leadership is about influencing others. Management is about controlling others.
Leaders inspire others, managers direct them.
Leaders inspire people to achieve success. Managers keep their workers focused.
A leader develops people; a manager manages people.
What are the steps involved in making a decision in management?
Managers face complex and multifaceted decision-making challenges. This involves many factors including analysis, strategy and planning, implementation, measurement and evaluation, feedback, feedback, and others.
Management of people requires that you remember that they are just as human as you are, and can make mistakes. You can always improve your performance, provided you are willing to make the effort.
This video will explain how decision-making works in Management. We discuss different types of decisions as well as why they are important and how managers can navigate them. The following topics will be covered.
Statistics
- 100% of the courses are offered online, and no campus visits are required — a big time-saver for you. (online.uc.edu)
- The BLS says that financial services jobs like banking are expected to grow 4% by 2030, about as fast as the national average. (wgu.edu)
- As of 2020, personal bankers or tellers make an average of $32,620 per year, according to the BLS. (wgu.edu)
- Our program is 100% engineered for your success. (online.uc.edu)
- Your choice in Step 5 may very likely be the same or similar to the alternative you placed at the top of your list at the end of Step 4. (umassd.edu)
External Links
How To
How do you apply the Kaizen method to your life?
Kaizen means continuous improvement. The Japanese philosophy emphasizes small, incremental improvements to achieve continuous improvement. This term was created by Toyota Motor Corporation in 1950. It is a process where people come together to improve their processes.
Kaizen is one the most important methods of Lean Manufacturing. This concept requires employees to identify and solve problems during manufacturing before they become major issues. This will increase the quality and decrease the cost of the products.
Kaizen is the idea that every worker should be aware of what is going on around them. Correct any errors immediately to avoid future problems. So, if someone notices a problem while working, he/she should report it to his/her manager.
Kaizen is based on a few principles. When working with kaizen, we always start with the end result and move towards the beginning. In order to improve our factory's production, we must first fix the machines producing the final product. Next, we repair the machines that make components. Then, the machines that make raw materials. Then we fix the workers, who directly work with these machines.
This approach is called 'kaizen' because it focuses on improving everything steps by step. After we're done with the factory, it's time to go back and fix the problem.
To implement kaizen in your business, you need to find out how to measure its effectiveness. There are many methods to assess if kaizen works well. One way is to examine the amount of defects on the final products. Another way is determining how much productivity increased after implementing kaizen.
If you want to find out if your kaizen is actually working, ask yourself why. Was it just because it was the law or because you wanted to save money? It was a way to save money or help you succeed.
Congratulations! You're ready to start kaizen.