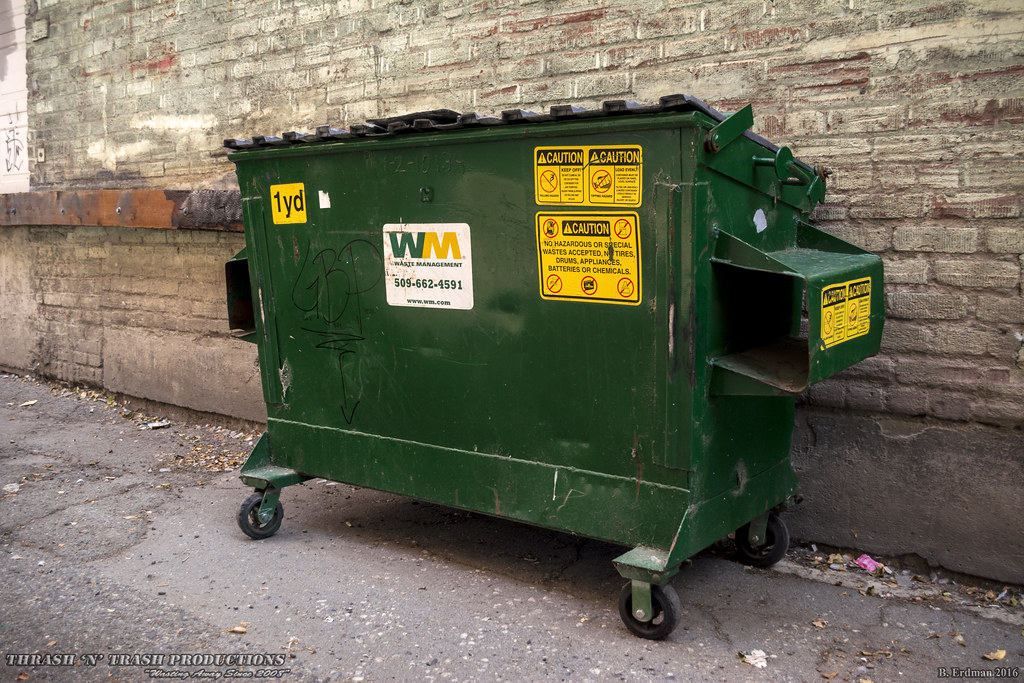
Corporate transformations are not a success story. Despite the fact that scholars and consultants have improved our knowledge of the phenomenon, most corporate transformations fail to deliver the expected benefits. These transformations are often abandoned. Here are some ways to improve change management:
Lessons learned from ASDA's Driving Test
ASDA's experience is a great example of the importance of evolution and experimentation in managing change. ASDA opened an experimental store, which was later expanded to three locations. All of these stores were declared safe zones. In this case study, the driving force redesigned ASDA's retail proposition, organizational structure, and management team, and encouraged store managers to experiment with product ranges, layout, and employee roles. This resulted in an incredibly high rate of success.
ASDA's executive were awarded stock options that were tied to company value. This helped to attract and retain key executives, and drove rapid company transformation. Stock-ownership plans offered variable compensation, based on store records and corporate performance. Despite the many challenges faced, the resultant culture of trusting and openness was a great success.
How to improve your change management
HR professionals must not only lead the change effort but also ensure that it is done smoothly and effectively. They must plan the implementation phases, define key roles, communicate key dates, and monitor results. They must also listen to employee feedback and adjust the plans as needed. Technology and education can be used by HR professionals to assist in the management of change. These are just a few ways that you can improve the HR function of change management in your company. To make your change management process efficient, you should use them.
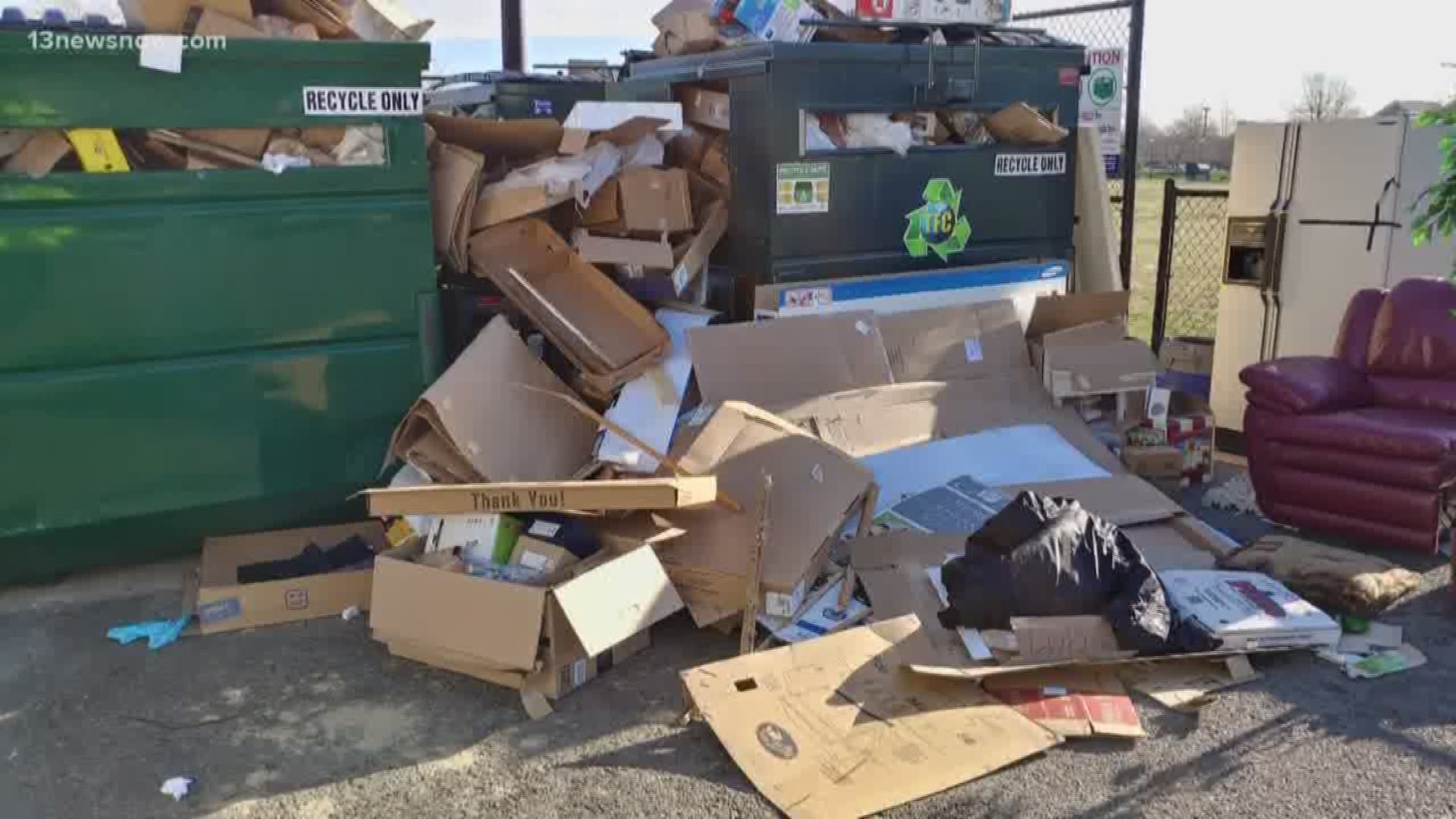
Identify the affected employees. Employees want the opportunity to contribute to the process. This is why a change channel should exist to collect employee feedback. To help managers make informed decisions about the change, invest in employee engagement and training. Employees will also benefit from the training and information managers receive about the change. To foster a positive environment, include managers as well. Recognize their contribution and encourage them to do so.
FAQ
How do you define Six Sigma?
Six-sigma will be well-known to anyone who has worked in operations research or statistics. It can be used by anyone in any business aspect.
It is a commitment-intensive task that requires strong leadership skills.
Why is it so important for companies that they use project management techniques
Project management techniques ensure that projects run smoothly while meeting deadlines.
This is because most businesses rely heavily on project work to produce goods and services.
These projects require companies to be efficient and effective managers.
Companies can lose time, money, and reputation if they don't have a good project management system.
How can a manager improve his/her managerial skills?
By practicing good management skills at all times.
Managers must monitor the performance of subordinates constantly.
You must act quickly if you notice that your subordinate isn’t performing to their standards.
You must be able to spot what is lacking and how you can improve it.
What is Six Sigma?
This is a method of quality improvement that emphasizes customer service, continuous learning, and customer service. This is an approach to quality improvement that uses statistical techniques to eliminate defects.
Motorola's 1986 efforts to improve manufacturing process efficiency led to the creation of Six Sigma.
The idea spread quickly throughout the industry, and today, many organizations are using six sigma methods to improve product design, production, delivery, and customer service.
Statistics
- The BLS says that financial services jobs like banking are expected to grow 4% by 2030, about as fast as the national average. (wgu.edu)
- 100% of the courses are offered online, and no campus visits are required — a big time-saver for you. (online.uc.edu)
- Our program is 100% engineered for your success. (online.uc.edu)
- Your choice in Step 5 may very likely be the same or similar to the alternative you placed at the top of your list at the end of Step 4. (umassd.edu)
- This field is expected to grow about 7% by 2028, a bit faster than the national average for job growth. (wgu.edu)
External Links
How To
How can you use the Kaizen method?
Kaizen means continuous improvement. The term was coined in the 1950s at Toyota Motor Corporation and refers to the Japanese philosophy emphasizing constant improvement through small incremental changes. It's a process where people work together to improve their processes continuously.
Kaizen is one of Lean Manufacturing's most efficient methods. This concept requires employees to identify and solve problems during manufacturing before they become major issues. This way, the quality of products increases, and the cost decreases.
The main idea behind kaizen is to make every worker aware of what happens around him/her. If something is wrong, it should be corrected immediately so that no problem occurs. Report any problem you see at work to your manager.
When doing kaizen, there are some principles we must follow. When working with kaizen, we always start with the end result and move towards the beginning. To improve our factory, for example, we need to fix the machines that produce the final product. First, we fix machines that produce components. Next, we fix machines that produce raw material. Then we fix the workers, who directly work with these machines.
This is known as "kaizen", because it emphasizes improving each step. Once we have finished fixing the factory, we return to the beginning and work until perfection.
To implement kaizen in your business, you need to find out how to measure its effectiveness. There are many ways to tell if kaizen is effective. One method is to inspect the finished products for defects. Another way is to see how much productivity has increased since implementing kaizen.
If you want to find out if your kaizen is actually working, ask yourself why. Is it because the law required it or because you want to save money. You really believed it would make you successful?
Congratulations! You're now ready to get started with kaizen.