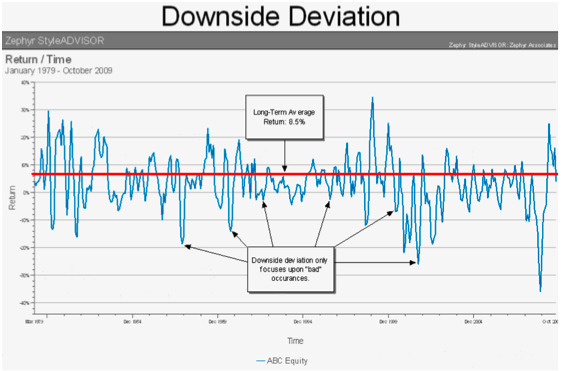
Not having an HR Department is worse than not having one. It is crucial to assess the cost and benefits of having a HR department. If you are considering outsourcing your HR functions, you need to be clear about what you are doing.
There is nothing worse than not having a HR department
Having an HR department is essential to the success of any company. It allows you to manage your employees. It also helps you make better decisions about hiring, firing, and benefits. It can help create an environment that is fair for everyone. HR can give your company a competitive edge.
The HR department can help if there is a problem at work. HR can report to the manager, for example, if someone is acting in a nonprofessional manner. This is helpful in situations where the problem is more serious.
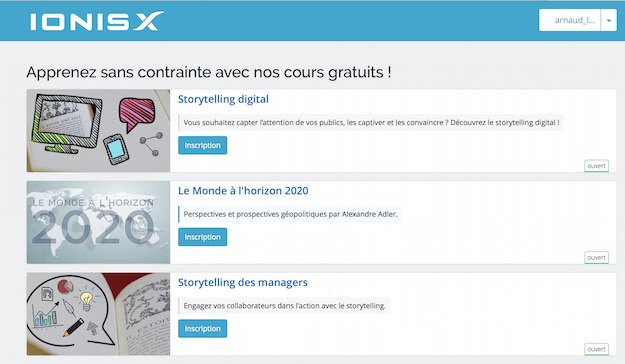
The costs of an HR department
Small businesses may find it difficult to pay for an in-house Human Resources department. A business could spend over PS12,000 annually to hire a full-time worker. It is also not efficient to hire a single HR employee. It is much better to have an HR team. This will give the company more control and can save you money in long-term. This will protect the company's data.
HR staff should have the right skills and knowledge to perform their job. There are a lot of costs associated with training and hiring. A small team is more efficient than a large department of HR. This is because smaller teams have access to better tools, training and business models. While this may require a greater budget, it will lead to a better overall cost-to–performance ratio.
Business operations are affected by having an HR department
An HR department has the primary task of hiring and keeping top talent for a company. The ultimate goal of this function, which is to ensure that the business has a happy workforce and increase profitability, is to achieve success. This is a complex task. There are many factors to consider in order to ensure that your HR department is making a positive impact on your business operations.
A key function of HR is to make sure that safety at work is maintained. HR can help reduce workplace injuries and accidents by creating risk mitigation programs and conducting site assessments. Employees are also protected by an effective workers' comp program.
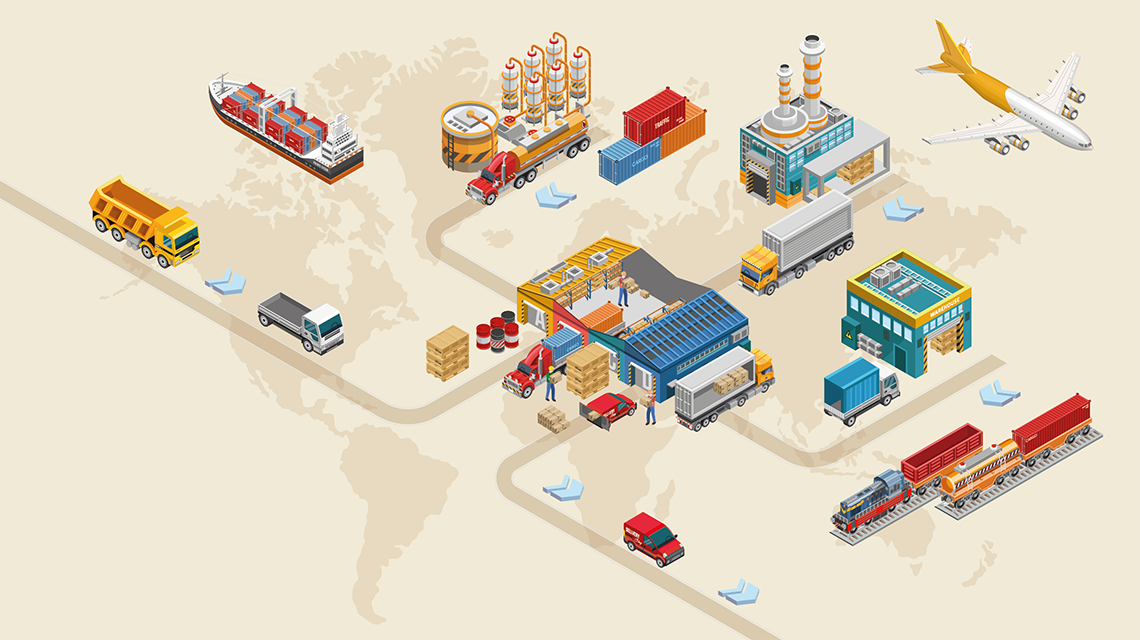
Impact of outsourcing HR functions
Outsourcing HR functions is a great way to reduce your company's payroll and other HR costs. It also allows you to maximize your resources for other business objectives. Outsourcing takes care of training, hiring, and replacing employees, freeing up valuable time for the main company to focus on other projects. Outsourcing can also allow companies to scale up or lower as needed, so they can remain competitive and accelerate productivity.
Outsourcing can also provide a host of other benefits. In some cases, companies can work more closely with the outsourcing company while still having the opportunity to interact with HR professionals. Other companies may have less options regarding employee benefits.
FAQ
Why does it sometimes seem so difficult to make good business decisions?
Complex systems with many moving parts are the hallmark of businesses. People who manage them have to balance multiple priorities while dealing with complexity and uncertainty.
It is important to understand the effects of these factors on the system in order to make informed decisions.
This requires you to think about the purpose and function of each component. It is important to then consider how the individual pieces relate to each other.
Also, you should ask yourself if there have been any assumptions in your past behavior. If you don't have any, it may be time to revisit them.
For help, ask someone else if you're still stumped after all the above. You may be able to see things from a different perspective than you are and gain insight that can help you find a solution.
What is TQM and how can it help you?
When manufacturing companies realized that price was not enough to compete, the industrial revolution brought about the quality movement. If they wanted to stay competitive, they needed to improve their quality and efficiency.
Management developed Total Quality Management to address the need for improvement. It focused on all aspects of an organisation's performance. It involved continuous improvement, employee participation, and customer satisfaction.
What is Six Sigma, exactly?
It's an approach to quality improvement that emphasizes customer service and continuous learning. It is a method that eliminates defects using statistical techniques.
Motorola invented Six Sigma in 1986 as part its efforts to improve manufacturing.
This idea quickly spread throughout the industry. Today, many organizations use six sigma methods for product design, production and delivery.
Statistics
- Hire the top business lawyers and save up to 60% on legal fees (upcounsel.com)
- Our program is 100% engineered for your success. (online.uc.edu)
- This field is expected to grow about 7% by 2028, a bit faster than the national average for job growth. (wgu.edu)
- The BLS says that financial services jobs like banking are expected to grow 4% by 2030, about as fast as the national average. (wgu.edu)
- The average salary for financial advisors in 2021 is around $60,000 per year, with the top 10% of the profession making more than $111,000 per year. (wgu.edu)
External Links
How To
How is Lean Manufacturing done?
Lean Manufacturing processes are used to reduce waste and improve efficiency through structured methods. They were created by Toyota Motor Corporation in Japan in the 1980s. The primary goal was to make products with lower costs and maintain high quality. Lean manufacturing seeks to eliminate unnecessary steps and activities in the production process. It is made up of five elements: continuous improvement, continuous improvement, just in-time, continuous change, and 5S. It is a system that produces only the product the customer requests without additional work. Continuous improvement is the continuous improvement of existing processes. Just-in-time is when components and other materials are delivered at their destination in a timely manner. Kaizen means continuous improvement. Kaizen involves making small changes and improving continuously. The 5S acronym stands for sort in order, shine standardize and maintain. To achieve the best results, these five elements must be used together.
Lean Production System
Six key concepts underlie the lean production system.
-
Flow - focus on moving material and information as close to customers as possible;
-
Value stream mapping - Break down each stage in a process into distinct tasks and create an overview of the whole process.
-
Five S's: Sort, Shine Standardize, Sustain, Set In Order, Shine and Shine
-
Kanban – visual signals like colored tape, stickers or other visual cues are used to keep track inventory.
-
Theory of constraints: Identify bottlenecks and use lean tools such as kanban boards to eliminate them.
-
Just-intime - Order components and materials at your location right on the spot.
-
Continuous improvement - incremental improvements are made to the process, not a complete overhaul.