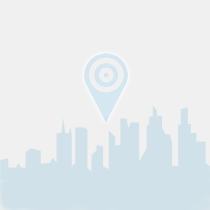
Process knowledge management can be a key tool in quality control and risk management. It is a framework that allows for the linking of past knowledge and current knowledge. It is also a foundation for continual improvement. Let's take a look at some benefits of process information management. Here are some. It might surprise you how valuable it is to your organization. It's also easy to put into practice.
Lessons learned
If possible, you will create a template to document the lessons learned for your organization and make it available to all employees. You could use a document management software to share the lessons with all your team members. Your team should find the template simple and understandable. However, you can also test different formats. The more complex your document is, the less likely it will be shared by your employees. It is therefore important to select the best format for your document and engage your employees.

Expertise location
Today, expert location is more than biographical information. It allows you to share your knowledge and find the right employees to answer your questions. For example, most people have a profile on LinkedIn, Facebook, or Google+ that includes their areas of expertise. These tools make it easy to organize information, giving people places to talk about their publications, projects and knowledge. This can help them build their reputation and increase their visibility.
Communities & Networks
The creation of virtual communities may facilitate cross-industry collaborations, and strategic knowledge management. These communities foster communication and the dissemination of new processes and methods that can help improve performance and innovation within organisations. They can improve the efficiency of meetings and help to disseminate case history. A number of industry leaders are exploring the benefits of using communities in industrial manufacturing. More information is available at Communities & networks to process knowledge management. A framework for effective knowledge control, communities and network are intended to bring together individuals from various disciplines.
Content management
A content-management software can store a 200-page training document, but it cannot replace knowledge management systems that can capture institutional or user-generated knowledge about a subject. The ideal system will be able capture information from different perspectives. This is useful for helping customers and making better decisions. If a company sells cars, the content-management software can store all sales training materials.
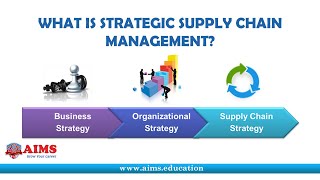
Knowledge mapping
Knowledge mapping is an excellent tool for leveraging your knowledge assets to improve the process. Knowledge mapping is a powerful way to identify knowledge gaps and find solutions for improving your process. It is also an excellent tool for increasing collaboration and engagement among departments. Once you have mapped out your knowledge, you can begin to standardize processes. Knowledge maps are a great way to capture and disseminate best practices and improve your organization's processes and operations.
FAQ
What is TQM exactly?
The quality movement was born during the industrial revolution when manufacturing companies realized they could not compete on price alone. They needed to improve quality and efficiency if they were going to remain competitive.
Management developed Total Quality Management to address the need for improvement. It focused on all aspects of an organisation's performance. It included continual improvement processes, employee involvement, customer satisfaction, and customer satisfaction.
What are the five management process?
Planning, execution, monitoring and review are the five stages of any business.
Planning means setting goals for the long-term. This includes setting goals for the future and defining what you want.
Execution takes place when you actually implement the plans. These plans must be adhered to by everyone.
Monitoring is a way to track progress towards your objectives. Regular reviews of performance against targets, budgets, and other goals should be part.
Review events take place at each year's end. They give you an opportunity to review the year and assess how it went. If not then, you can make changes to improve your performance next year.
Following the annual review, evaluation is done. It helps to determine what worked and what didn’t. It also provides feedback on the performance of people.
What does it mean to say "project management"
That is the management of all activities associated with a project.
We include defining the scope of the project, identifying the requirements, preparing the budget, organizing the project team, scheduling the work, monitoring progress, evaluating results, and closing down the project.
How can a manager motivate employees?
Motivation can be defined as the desire to achieve success.
It is possible to be motivated by doing something you enjoy.
Or you can get motivated by seeing yourself making a contribution to the success of the organization.
For example, if you want to become a doctor, you'll probably find it more motivating to see patients than to study medicine books all day.
A different type of motivation comes directly from the inside.
You might feel a strong sense for responsibility and want to help others.
Perhaps you enjoy working hard.
If you don’t feel motivated, find out why.
Next, think of ways you can improve your motivation.
Statistics
- The average salary for financial advisors in 2021 is around $60,000 per year, with the top 10% of the profession making more than $111,000 per year. (wgu.edu)
- UpCounsel accepts only the top 5 percent of lawyers on its site. (upcounsel.com)
- As of 2020, personal bankers or tellers make an average of $32,620 per year, according to the BLS. (wgu.edu)
- Our program is 100% engineered for your success. (online.uc.edu)
- The profession is expected to grow 7% by 2028, a bit faster than the national average. (wgu.edu)
External Links
How To
How can Lean Manufacturing be done?
Lean Manufacturing is a method to reduce waste and increase efficiency using structured methods. They were created in Japan by Toyota Motor Corporation during the 1980s. The primary goal was to make products with lower costs and maintain high quality. Lean manufacturing is about eliminating redundant steps and activities from the manufacturing process. It has five components: continuous improvement and pull systems; just-in time; continuous change; and kaizen (continuous innovation). Pull systems allow customers to get exactly what they want without having to do extra work. Continuous improvement is the continuous improvement of existing processes. Just-in time refers to components and materials being delivered right at the place they are needed. Kaizen stands for continuous improvement. Kaizen can be described as a process of making small improvements continuously. Five-S stands for sort. It is also the acronym for shine, standardize (standardize), and sustain. These five elements are combined to give you the best possible results.
Lean Production System
Six key concepts form the foundation of the lean production system:
-
Flow: The goal is to move material and information as close as possible from customers.
-
Value stream mapping: This is a way to break down each stage into separate tasks and create a flowchart for the entire process.
-
Five S's: Sort, Shine Standardize, Sustain, Set In Order, Shine and Shine
-
Kanban – visual signals like colored tape, stickers or other visual cues are used to keep track inventory.
-
Theory of constraints - identify bottlenecks during the process and eliminate them with lean tools like Kanban boards.
-
Just-in-time - deliver components and materials directly to the point of use;
-
Continuous improvement - incremental improvements are made to the process, not a complete overhaul.