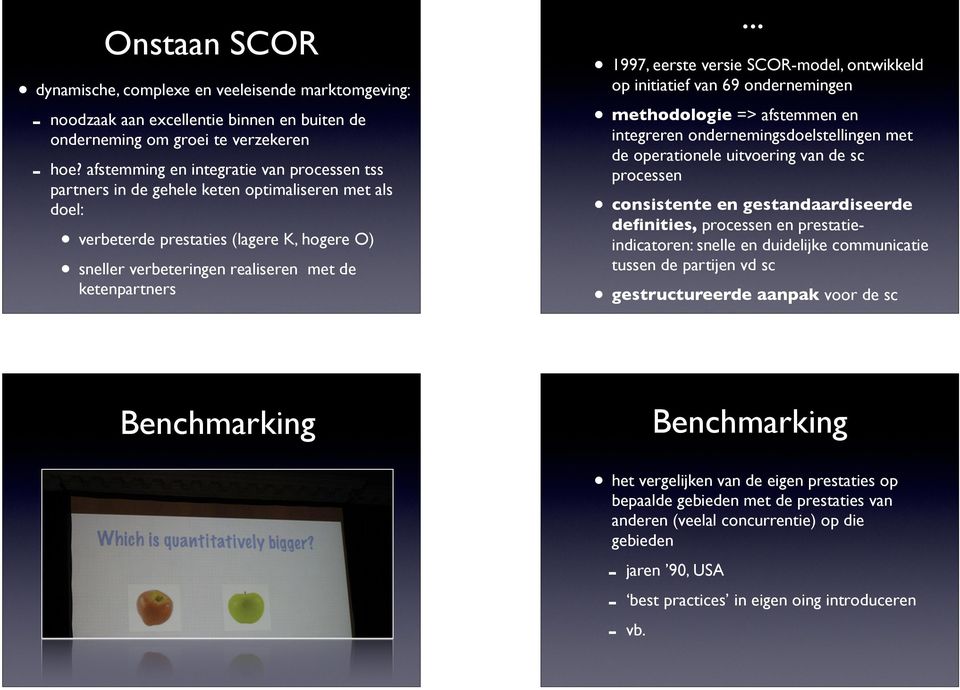
The Associate in Risk Management Program (ARM), teaches students how they can master the rapidly changing field of risk management. Graduates will be able to manage all aspects risk in their organizations confidently. Learn about operational, financial, and strategic risks while getting a global view. This program is designed with a technology-driven perspective in mind.
ARM designation
An ARM is a professional title in risk management. The candidate must demonstrate competency in risk analysis, hazard detection, and risk response. For advancement to Fellow Designation of RIMS - a non-profit organization that represents professionals in risk management around the world, an ARM designation will be required.
The ARM program prepares students with the ability to manage rapid technology-driven changes in their risk management. Graduates of this program will be able manage all forms of risk in the workplace. They will learn about managing hazard risk and financial risk. The program also provides students with a global perspective on risk management.
Courses
Associate in risk management (ARM) courses focus on educating students in the rapidly evolving field of risk management. The program provides students with the skills necessary to confidently handle all aspects of risk within an organization. Students will learn how to manage operational, financial, and strategic risk. Students are also taught how to manage global risks. Students are also equipped with the technology-driven perspective necessary to help them succeed as risk managers.
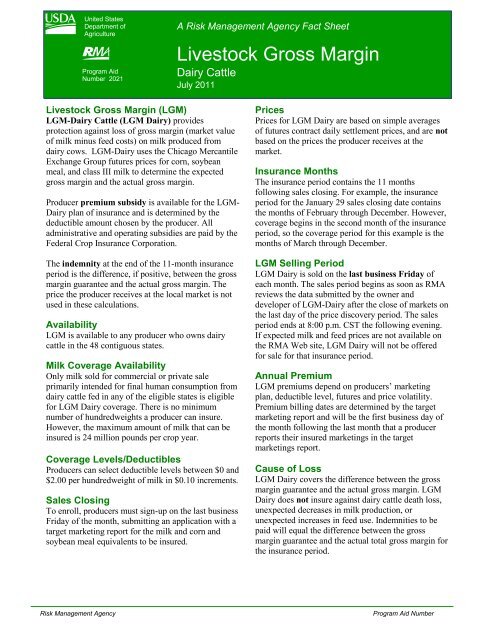
The courses offered by RISK management education institutions vary. Some courses are designed for professionals in risk management, while others can be used by business generalists. Advanced courses concentrate on strategic risk management.
Exam
The Associate exam in risk management is a professional certification, which allows you to become risk manager. This exam covers both quantitative and qualitative approaches to risk management. It helps you become more aware of risk factors and make informed decisions. It will also help you to understand risk quadrants, and their importance.
The certification requires students complete three core courses, as well as an exam in risk management ethics. The exam is comprised of approximately 15 to 40 multiple-choice question and is graded according to a pass-fail system. This exam is not for the weak of heart. Keir Educational Ressources has study materials to help you get the Associate in Risk Management certification.
Pay range
ZipRecruiter states that the average range of pay for associates working in risk management would be between $53,500 and $79,000. The highest paid associates can earn as much $90,000. However, the actual pay range can vary by up to $25,000 depending on your location, employer, and years of experience.
The salary range for an associate in risk management depends on the area where you work and the size of your organization. Higher salaries are available at larger companies and in greater cities. A university degree in a relevant field, solid knowledge of risk management and the ability to manage projects are all necessary.
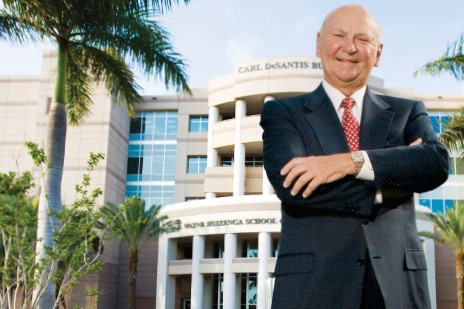
For ARM candidates, a free course is available
The Institutes offer a complimentary course that will help you become an ARM (associate risk management). The course will prepare you for the ARM exam. It is completely free and includes an online module called Ethical guidelines for insurance professionals. Candidates who complete the online course may earn up to fifty credits towards their certification.
The Insurance Institute of America has awarded the professional designation of Associate in Risk Management (ARM). It examines the science and principles involved in risk management. This includes methods for managing, minimizing, or avoiding risks. These courses are self-study courses, and candidates are expected to complete them prior to taking the exam.
FAQ
What are the steps that management takes to reach a decision?
Managers have to make complex decisions. It includes many factors such as analysis, strategy planning, implementation and measurement. Evaluation, feedback and feedback are just some of the other factors.
Management of people requires that you remember that they are just as human as you are, and can make mistakes. You can always improve your performance, provided you are willing to make the effort.
This video shows you how management makes decisions. We will explain the importance of different types decisions and how every manager can make them. You'll learn about the following topics:
What are the four main functions of management?
Management is responsible to plan, organize, direct, and control people and resources. Management also involves setting goals and developing policies.
Management aids an organization in reaching its goals by providing direction and coordination, control, leadership motivation, supervision, training, evaluation, and leadership.
Management's four main functions are:
Planning - This is the process of deciding what should be done.
Organizing – Organizing means deciding how to organize things.
Directing - This refers to getting people follow instructions.
Controlling - Controlling means ensuring that people carry out tasks according to plan.
It can sometimes seem difficult to make business decisions.
Complex systems with many moving parts are the hallmark of businesses. Their leaders must manage multiple priorities, as well as dealing with uncertainty.
To make good decisions, you must understand how these factors affect the entire system.
You must first consider what each piece of the system does and why. It is important to then consider how the individual pieces relate to each other.
Ask yourself if there are hidden assumptions that have influenced your behavior. If not, you might want to revisit them.
You can always ask someone for help if you still have questions after all of this. You might find their perspective is different from yours and they may have insight that can help you find the solution.
What kind of people use Six Sigma
Six sigma is a common concept for people who have worked in statistics or operations research. However, anyone involved in any aspect of business can benefit from using it.
It is a commitment-intensive task that requires strong leadership skills.
Statistics
- 100% of the courses are offered online, and no campus visits are required — a big time-saver for you. (online.uc.edu)
- The average salary for financial advisors in 2021 is around $60,000 per year, with the top 10% of the profession making more than $111,000 per year. (wgu.edu)
- Our program is 100% engineered for your success. (online.uc.edu)
- The BLS says that financial services jobs like banking are expected to grow 4% by 2030, about as fast as the national average. (wgu.edu)
- The profession is expected to grow 7% by 2028, a bit faster than the national average. (wgu.edu)
External Links
How To
What is Lean Manufacturing?
Lean Manufacturing techniques are used to reduce waste while increasing efficiency by using structured methods. These processes were created by Toyota Motor Corporation, Japan in the 1980s. The goal was to produce quality products at lower cost. Lean manufacturing focuses on eliminating unnecessary steps and activities from the production process. It is composed of five fundamental elements: continuous improvement; pull systems, continuous improvements, just-in–time, kaizen, continuous change, and 5S. Pull systems are able to produce exactly what the customer requires without extra work. Continuous improvement is constantly improving upon existing processes. Just-in–time refers when components or materials are delivered immediately to their intended destination. Kaizen means continuous improvement. Kaizen involves making small changes and improving continuously. Finally, 5S stands for sort, set in order, shine, standardize, and sustain. These five elements can be combined to achieve the best possible results.
The Lean Production System
Six key concepts are the basis of lean production:
-
Flow: The goal is to move material and information as close as possible from customers.
-
Value stream mapping: This is a way to break down each stage into separate tasks and create a flowchart for the entire process.
-
Five S's - Sort, Set In Order, Shine, Standardize, and Sustain;
-
Kanban - visual cues such as stickers or colored tape can be used to track inventory.
-
Theory of constraints - identify bottlenecks in the process and eliminate them using lean tools like kanban boards;
-
Just-intime - Order components and materials at your location right on the spot.
-
Continuous improvement - incremental improvements are made to the process, not a complete overhaul.