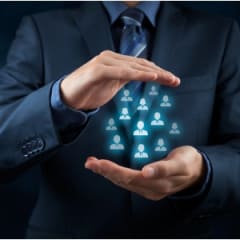
Here are the top methods to reduce your carbon footprint and lower your supply chain's emission. These include: Engaging stakeholders, Managing sustainable procurement, and addressing social responsibility. This will allow you to create a more sustainable, predictable supply chain.
Engagement of stakeholders
Engagement with stakeholders is crucial to the sustainability efforts of a company. Engaging stakeholders can help speed up your sustainability journey. With robust engagement strategies, companies can develop a collaborative culture and effectively work with multiple stakeholders. In addition to improving the supply chain, engaging stakeholders helps a company gain valuable insights on risks and opportunities.
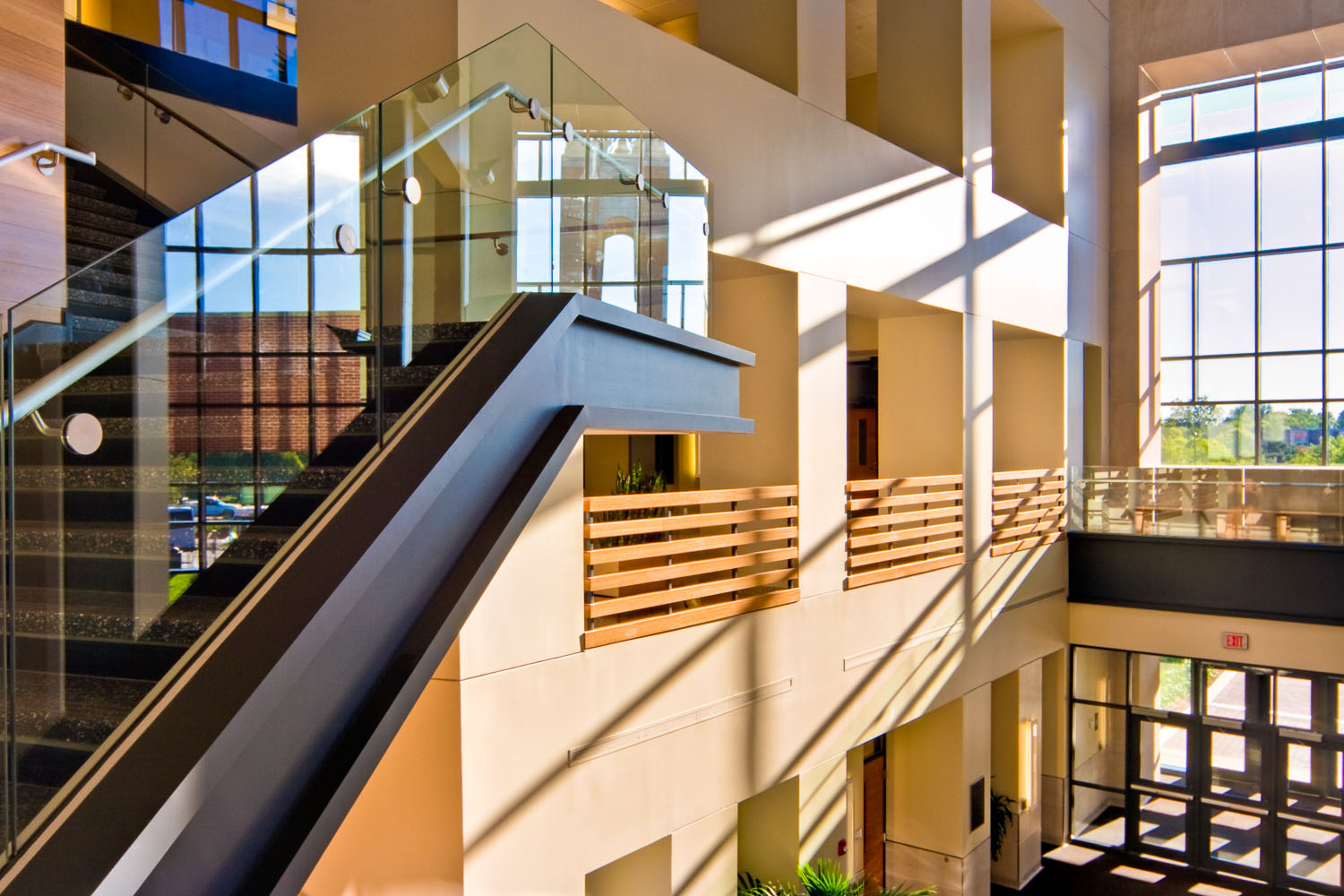
Companies should choose carefully the metrics they would like to track in order engage stakeholders in a sustainable supplier chain. A business' social and environmental dimensions must be considered when selecting metrics. Companies can have a difficult time measuring environmental and social metrics. It is also possible that many stakeholders are not aware of the company’s sustainability efforts. This makes engagement challenging.
Managing sustainable procurement
Managing sustainable procurement is an important process for any company. It is crucial to ensure transparency throughout the supply chain, and that Tier 1 suppliers hold companies accountable for sustainable procurement. Some organizations have difficulty implementing sustainable practices as they lack full visibility into the supply chain. EcoVadis conducted a survey and found that half of the organizations did not have full visibility into supply chains. 28% of those surveyed didn't even have such visibility. Even though implementing sustainability measures may take years, it is possible to start small with auditing suppliers.
Making sustainable procurement a standard part the procurement process can help procurement teams minimize risks, identify incremental improvement opportunities, and ensure internal customers are informed about the impact of their purchases. To be truly sustainable, organizations must think beyond the conventional options to find and implement sustainable procurement strategies. For example, they must work with their suppliers in new ways, develop new technical skills, and make sure that they have adequate data and information to support their goals.
Social Responsibility Management
Sustainable supply chains must manage social responsibility (CSR). CSR principles should be applied at all stages of the supply chain. The environment must not be harmed by products and services provided by companies. This includes planning for the future, assessing product lifecycles, developing reuse strategies, and developing transportation capability. Companies must also consider the needs of their customers and comply with all applicable regulations.
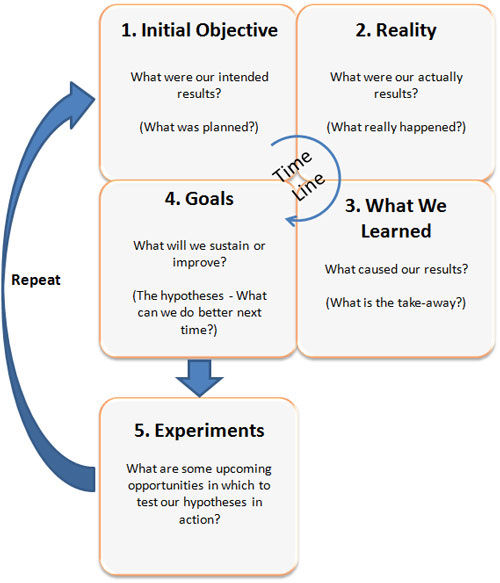
Sustainability is all about meeting current demands without compromising future needs. But it also covers social, economic and environmental concerns. Social responsibility involves a commitment by a business to conduct business ethically and to benefit its workforce, the local community, and society at large.
FAQ
Six Sigma is so popular.
Six Sigma can be implemented quickly and produce impressive results. It can also be used to help companies identify and focus on the most important aspects of their business.
How can a manager motivate employees?
Motivation refers to the desire or need to succeed.
Enjoyable activities can motivate you.
You can also feel motivated by making a positive contribution to the success in the organization.
For example, if your goal is to become a physician, you will probably find it more motivational to see patients rather than to read a lot of medicine books.
The inner motivation is another type.
You might feel a strong sense for responsibility and want to help others.
Maybe you like working hard.
If you don't feel motivated, ask yourself why.
Next, think of ways you can improve your motivation.
What are the 3 main management styles?
The three major management styles are authoritarian (left-faire), participative and laissez -faire. Each style has its own strengths and weaknesses. Which style do YOU prefer? Why?
Authoritarian – The leader sets a direction and expects everyone follows it. This style works best if the organization is large and stable.
Laissez faire - Each individual can decide for himself/herself. This style is best when the organization has a small but dynamic group.
Participative - The leader listens to ideas and suggestions from everyone. This style works best in smaller organizations where everyone feels valued.
What is a simple management tool that aids in decision-making and decision making?
A decision matrix, a simple yet powerful tool for managers to make decisions, is the best. It helps them to think strategically about all options.
A decision matrix is a way of representing alternatives as rows and columns. This allows one to see how each alternative impacts other options.
This example shows four options, each represented by the boxes on either side of the matrix. Each box represents an alternative. The top row represents the current state of affairs, and the bottom row is indicative of what would happen in the event that nothing were done.
The effect of choosing Option 1 can be seen in column middle. In this example, it would lead to an increase in sales of between $2 million and $3 million.
The effects of options 2 and 3 are shown in the next columns. These positive changes can increase sales by $1 million or $500,000. They also have negative consequences. Option 2, for example, increases the cost by $100 000 while Option 3 decreases profits by $200 000.
The final column shows the results for Option 4. This will result in sales falling by $1,000,000
The best thing about a decision matrix is the fact that you don't have to remember which numbers go with what. The best thing about a decision matrix is that you can simply look at the cells, and immediately know whether one option is better or not.
The matrix has already done all of the work. It's as easy as comparing numbers in the appropriate cells.
Here's an example showing how you might use a Decision Matrix in your business.
You want to decide whether or not to invest more money into advertising. You'll be able increase your monthly revenue by $5000 if you do. You'll also have additional expenses up to $10,000.
The net result of advertising investment can be calculated by looking at the cell below that reads "Advertising." It is 15 thousand. Advertising is a worthwhile investment because it has a higher return than the costs.
Statistics
- The profession is expected to grow 7% by 2028, a bit faster than the national average. (wgu.edu)
- Your choice in Step 5 may very likely be the same or similar to the alternative you placed at the top of your list at the end of Step 4. (umassd.edu)
- Our program is 100% engineered for your success. (online.uc.edu)
- 100% of the courses are offered online, and no campus visits are required — a big time-saver for you. (online.uc.edu)
- UpCounsel accepts only the top 5 percent of lawyers on its site. (upcounsel.com)
External Links
How To
How does Lean Manufacturing work?
Lean Manufacturing processes are used to reduce waste and improve efficiency through structured methods. They were created by Toyota Motor Corporation in Japan in the 1980s. The primary goal was to make products with lower costs and maintain high quality. Lean manufacturing seeks to eliminate unnecessary steps and activities in the production process. It consists of five basic elements: pull systems, continuous improvement, just-in-time, kaizen (continuous change), and 5S. Pull systems involve producing only what the customer wants without any extra work. Continuous improvement refers to continuously improving existing processes. Just-in-time is when components and other materials are delivered at their destination in a timely manner. Kaizen means continuous improvement. Kaizen involves making small changes and improving continuously. Fifth, the 5S stand for sort, set up in order to shine, standardize, maintain, and standardize. These five elements can be combined to achieve the best possible results.
Lean Production System
Six key concepts make up the lean manufacturing system.
-
Flow: The goal is to move material and information as close as possible from customers.
-
Value stream mapping- This allows you to break down each step of a process and create a flowchart detailing the entire process.
-
Five S's - Sort, Set In Order, Shine, Standardize, and Sustain;
-
Kanban - visual cues such as stickers or colored tape can be used to track inventory.
-
Theory of Constraints - Identify bottlenecks in the process, and eliminate them using lean tools such kanban boards.
-
Just-in time - Get components and materials delivered right at the point of usage;
-
Continuous improvement: Make incremental improvements to the process instead of overhauling it completely.