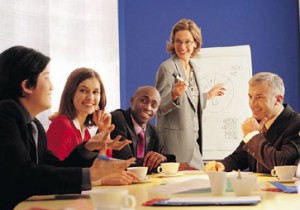
Process safety management is an organized approach to the management and integrity of all operating systems within a facility. This system is required by law in major hazard areas and must be updated at the very least every five-year. Process safety management aims to prevent accidents. If you're interested in implementing process safety management, here are some steps to get started. These steps will help you make sure your facilities are safe and prevent accidents.
Process safety management is a structured framework to manage the integrity of operating systems.
Process safety management's goal is to decrease the number of incidents. This will increase sustained value and productivity. It focuses on controlling risks within the plant and inherently safer equipment. It includes strict compliance to operating procedures and hazard assessments. It includes training, maintenance, and control of process. It is an essential component of a safety-conscious company.
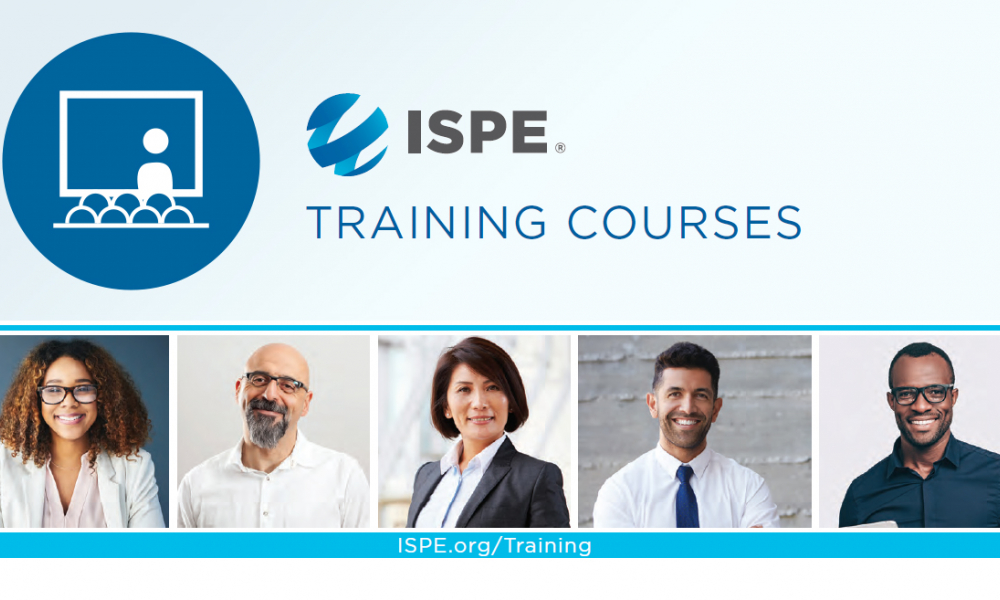
It should be renewed every 5 years
The Occupational Safety and Health Administration (OSHA) requires that processes be reviewed and updated regularly. This includes the development and updating of safety procedures and processes. All employees who are involved in the project must have this information. Written procedures and investigation reports must be kept for five years. Employees should have easy access to up-to-date process safety information. An employer can use safety risk management consultants to help them meet their requirements.
It is a requirement of law for major hazards facilities
All major hazards facilities must have a process safety management system. In addition to developing and implementing the program, employers must implement a procedure for a prompt and safe evacuation of employees. The plan must include a safety alarm which will notify employees to evacuate. It should also contain emergency procedures to aid employees who are not physically able to evacuate the hazardous zone.
It prevents incidents
A well-developed process safety management system can improve a company's profitability, safety performance, and quality. It can also help improve the company’s environmental responsibility. It reduces the likelihood of incidents. These four areas are crucial for the long-term survival of a business. Here is a quick overview of the many benefits of a process safety system. It is a system that helps companies prevent and reduce accidents, as well as improve the safety and health of employees and customers.
It takes a lot of time.
Process safety management can be complicated and time-consuming in a hazardous chemical plant. OSHA doesn’t regulate process safety management programs. However it requires that facilities have a written plan to implement them and comply with 14 minimum requirements. Some companies rely on spreadsheets and forms to collect data and compile risk assessments and other information. This can be time-consuming and exposes you to human error.
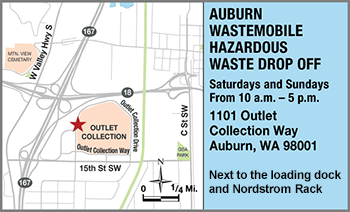
Participation by employees is necessary
Pennsylvania State University adopted PSM programs that include an Employee Participation component. This element leverages employees' knowledge, experience, and unique perspectives to improve safety. The program describes different mechanisms for employee participation and identifies minimum requirements for participation. It is important to include all employees in the process safety management process and involve them in all aspects. To avoid serious incidents, employee participation in PSM can be crucial. How do you ensure employees are fully engaged in the PSM program?
FAQ
Why is project management important for companies?
Project management techniques can be used to ensure smooth project execution and meeting deadlines.
Because most businesses depend heavily on project work to produce goods or services,
Companies must manage these projects effectively and efficiently.
Without effective project management, companies may lose money, time, and reputation.
How to manage employees effectively?
Effectively managing employees requires that you ensure their happiness and productivity.
This includes setting clear expectations for their behavior and tracking their performance.
Managers need to establish clear goals for their team and for themselves.
They need to communicate clearly and openly with staff members. They also need to make sure that they discipline and reward the best performers.
They must also keep track of the activities of their team. These include:
-
What did we accomplish?
-
How much work was done?
-
Who did it all?
-
How did it get done?
-
Why did it happen?
This information can help you monitor your performance and to evaluate your results.
What is Six Sigma, exactly?
This is a method of quality improvement that emphasizes customer service, continuous learning, and customer service. It is a method that eliminates defects using statistical techniques.
Motorola's 1986 efforts to improve manufacturing process efficiency led to the creation of Six Sigma.
It was quickly adopted by the industry and many companies are now using six-sigma to improve product design, production, delivery, customer service, and product design.
Six Sigma is so popular.
Six Sigma can be implemented quickly and produce impressive results. Six Sigma also gives companies a framework for measuring improvement and helps them focus on what is most important.
What are the 4 main functions of management?
Management is responsible for planning, organizing, directing, and controlling people and resources. It includes creating policies and procedures, as well setting goals.
Management aids an organization in reaching its goals by providing direction and coordination, control, leadership motivation, supervision, training, evaluation, and leadership.
The four main functions of management are:
Planning - Planning refers to deciding what is needed.
Organizing is the act of deciding how things should go.
Directing – This means to get people to follow directions.
Controlling - Controlling means ensuring that people carry out tasks according to plan.
What are management concepts?
Management concepts are the fundamental principles and practices that managers use when managing people and their resources. These include topics such as human resource policies and job descriptions, performance assessments, training programs and employee motivation.
What is TQM and how can it help you?
The quality movement was born during the industrial revolution when manufacturing companies realized they could not compete on price alone. They had to improve efficiency and quality if they were to remain competitive.
To address this need for improvement management created Total Quality Management (TQM) which aimed to improve all aspects of an organization's performance. It included continuous improvement processes, employee involvement, and customer satisfaction.
Statistics
- Hire the top business lawyers and save up to 60% on legal fees (upcounsel.com)
- UpCounsel accepts only the top 5 percent of lawyers on its site. (upcounsel.com)
- Your choice in Step 5 may very likely be the same or similar to the alternative you placed at the top of your list at the end of Step 4. (umassd.edu)
- This field is expected to grow about 7% by 2028, a bit faster than the national average for job growth. (wgu.edu)
- The profession is expected to grow 7% by 2028, a bit faster than the national average. (wgu.edu)
External Links
How To
How do I get my Six Sigma certification?
Six Sigma can be used to improve quality and efficiency. It is a process that helps businesses achieve consistent results in their operations. The name comes from the first two letters of the Greek word "sigmas" which mean "six." Motorola was the first to develop this process. Motorola recognized that they had to standardize their manufacturing processes to produce faster and more affordable products. They had been having problems with consistency because of the many different people who were doing the work. They decided to use statistical tools like control charts and Pareto analysis to solve the problem. They would then apply these techniques to all aspects of their operation. After applying the technique, they could make improvements wherever there was potential. The Six Sigma certification process involves three major steps. First, you need to determine if your qualifications are valid. Before you take any exams, you'll need to take some classes. You can then start taking the tests once you have completed those classes. The class material will be reviewed. Once you have completed the class, you will be ready for the test. If you pass, then you will become certified. Final, your certifications can be added to you resume.