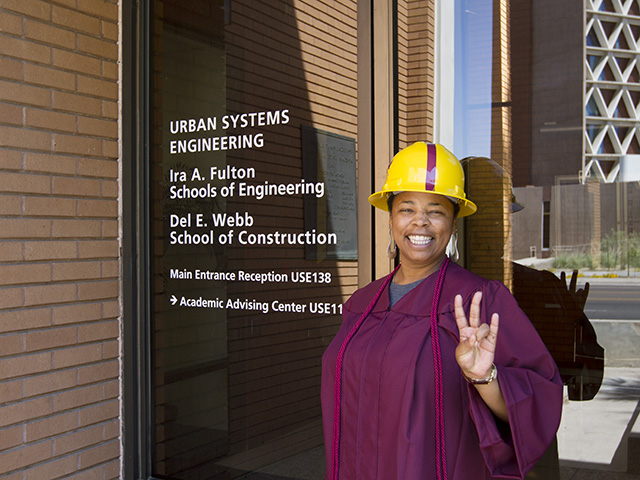
Generally speaking, a project is a collection of tasks designed to achieve a specific objective. This could be a new product/service or technological innovation. A project is usually a part or a component of a larger program. There may be defined boundaries and end dates. However, a project may be an independent, self contained effort.
Typical projects include new product development, construction, office shifting and technological change. These initiatives enable companies to clarify their goals, provide learning opportunities, and demonstrate how work contributes in the bigger picture. These initiatives are crucial to the success of a company. They can help lower costs of running a company and can save you money in the long term if done right.
Projects are typically task-oriented and depend on a team of people in order to achieve the desired results. These projects typically have short-term goals and limited budgets. These projects can be risky but can provide a competitive edge for companies.
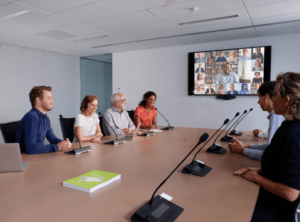
Projects are often organized in five phases. Each phase contains specific tasks and activities. Each phase has its own milestone. The project's WBS (Work Breakdown Structure) is also important, as it provides a clear picture of the work in progress.
Sometimes a project can be a step-stone to other activities. A relief effort following a natural disaster could help increase sales to a new market. This is a great way to show employees how they are part of a larger mission.
A project is an ongoing, multi-faceted process that seeks to accomplish a particular goal. The goal could be to improve customer service, increase business efficiency or create a new product. The project could include a new website, office relocation, or technological change. You can have a group of people from different companies work on the project. It can also be performed manually, or by using project management software.
One project might be a good technical solution but may not work with the workforce. A different project might have similar goals but be more well managed. A project can also be viewed as a test environment for an IT system. Projects can be used to demonstrate creativity, in addition to being a test.
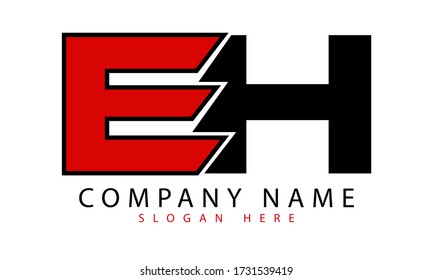
The most important function of a project is to achieve a specific goal. This can be achieved through a well-planned project plan or the transfer of the right learning to all the right people. The project's success depends on coordinating the efforts of the team and tracking the project's progress. A project's biggest risk is the lack of definition and focus. It is important that people lack the tools, training and knowledge necessary to manage projects effectively.
Projects are often referred to as stepping stones to corporate strategy. These projects are meant to be short-term, but can have an impact upon the company's overall performance. A company's greatest stepping stone is a successful project.
FAQ
Which kind of people use Six Sigma
People who have worked with statistics and operations research will usually be familiar with the concepts behind six sigma. But anyone can benefit from it.
Because it requires a high level of commitment, only those with strong leadership skills will make an effort necessary to implement it successfully.
Why is it so hard to make smart business decisions?
Complex systems with many moving parts are the hallmark of businesses. People who manage them have to balance multiple priorities while dealing with complexity and uncertainty.
It is important to understand the effects of these factors on the system in order to make informed decisions.
To do this, you must think carefully about what each part of the system does and why. Next, consider how each piece interacts with the others.
Ask yourself if there are hidden assumptions that have influenced your behavior. If you don't have any, it may be time to revisit them.
Asking for assistance from someone else is a good idea if you are still having trouble. They might see things differently than you and may have some insights that could help find a solution.
What does "project management" mean?
It refers to the management of activities related to a project.
We help you define the scope of your project, identify the requirements, prepare the budget, organize the team, plan the work, monitor progress and evaluate the results before closing down the project.
Statistics
- The BLS says that financial services jobs like banking are expected to grow 4% by 2030, about as fast as the national average. (wgu.edu)
- This field is expected to grow about 7% by 2028, a bit faster than the national average for job growth. (wgu.edu)
- Hire the top business lawyers and save up to 60% on legal fees (upcounsel.com)
- The profession is expected to grow 7% by 2028, a bit faster than the national average. (wgu.edu)
- As of 2020, personal bankers or tellers make an average of $32,620 per year, according to the BLS. (wgu.edu)
External Links
How To
How is Lean Manufacturing done?
Lean Manufacturing techniques are used to reduce waste while increasing efficiency by using structured methods. They were developed in Japan by Toyota Motor Corporation (in the 1980s). The primary goal was to make products with lower costs and maintain high quality. Lean manufacturing focuses on eliminating unnecessary steps and activities from the production process. It consists of five basic elements: pull systems, continuous improvement, just-in-time, kaizen (continuous change), and 5S. The production of only what the customer needs without extra work is called pull systems. Continuous improvement means continuously improving on existing processes. Just-in–time refers when components or materials are delivered immediately to their intended destination. Kaizen is continuous improvement. This can be achieved by making small, incremental changes every day. Five-S stands for sort. It is also the acronym for shine, standardize (standardize), and sustain. To achieve the best results, these five elements must be used together.
Lean Production System
The lean production system is based on six key concepts:
-
Flow is about moving material and information as near as customers can.
-
Value stream mapping- This allows you to break down each step of a process and create a flowchart detailing the entire process.
-
Five S’s - Sorted, In Order. Shine. Standardize. And Sustain.
-
Kanban - use visual signals such as colored tape, stickers, or other visual cues to keep track of inventory;
-
Theory of constraints - identify bottlenecks during the process and eliminate them with lean tools like Kanban boards.
-
Just-in time - Get components and materials delivered right at the point of usage;
-
Continuous improvement is making incremental improvements to your process, rather than trying to overhaul it all at once.