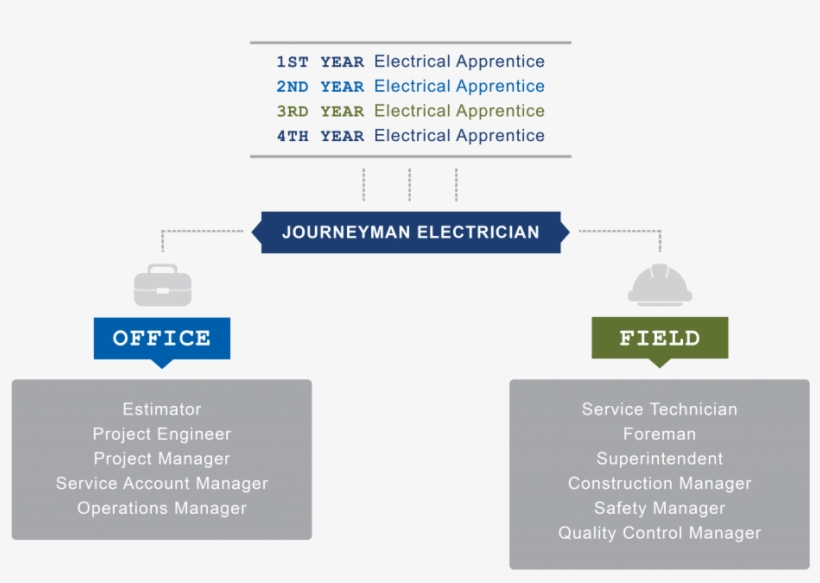
Process knowledge management can be a key tool in quality control and risk management. It is a framework that allows for the linking of past knowledge and current knowledge. It can also be used to support continuous improvement. Let's look at some of the many benefits of process knowledge management. Listed below are some of them. It's possible to be very useful for your organization. It's simple to implement.
Lessons learned
If possible, you will create a template to document the lessons learned for your organization and make it available to all employees. It is better to use a document manager system to share the lessons you have learned with your staff. Your team should find the template simple and understandable. However, you can also test different formats. The more complicated your document, the more likely your employees will resist sharing it. It's important to choose a format that is most suitable for your staff and keep them engaged.
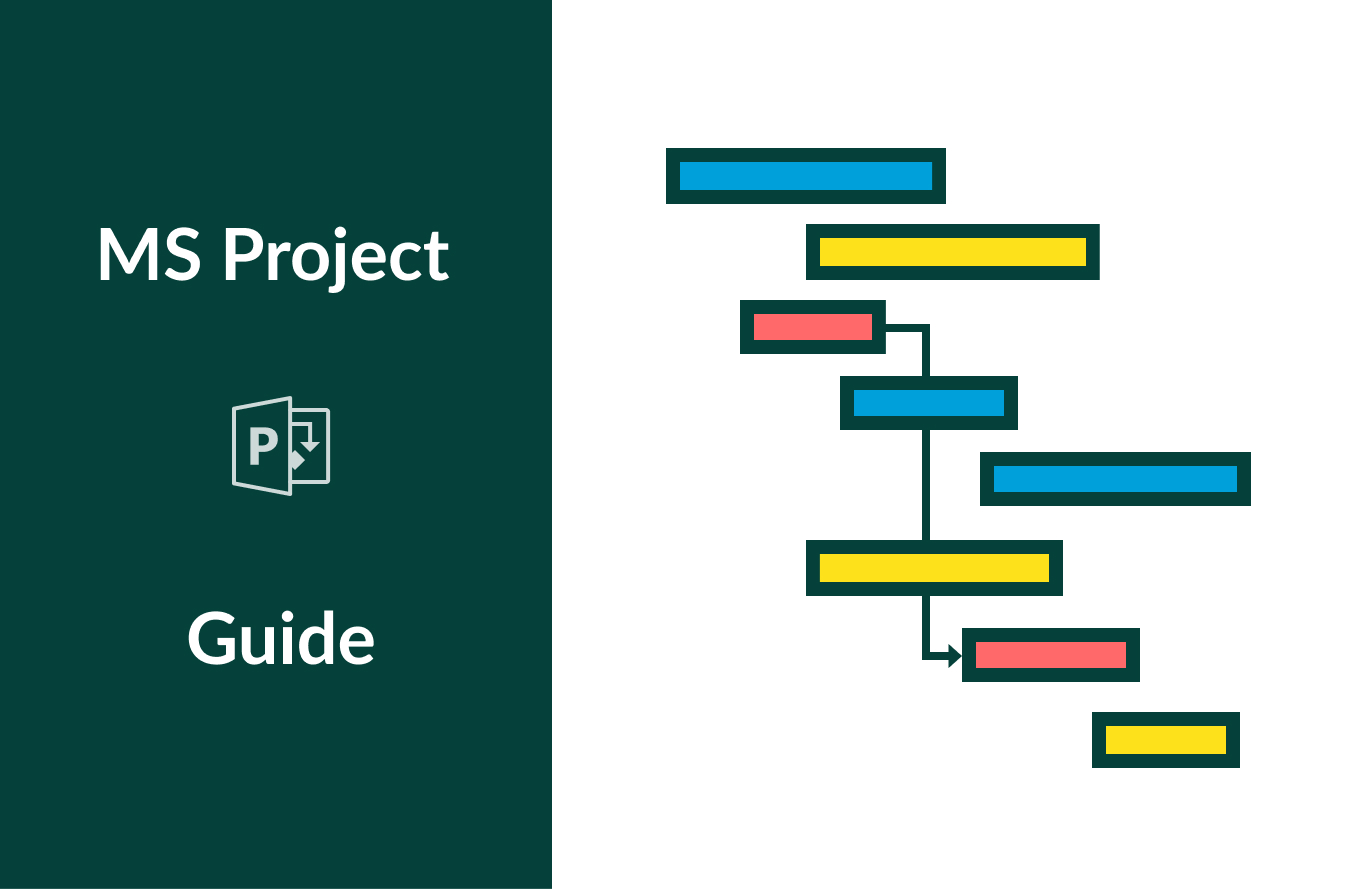
Expertise location
Today, expert location is more than biographical information. It provides tools for sharing knowledge and identifying the top employees who can answer questions. Most people have a LinkedIn, Facebook, and Google+ profile that includes their expertise. These tools can also help people organize their information by giving them places to discuss their publications, projects, or knowledge. This can help them increase their visibility and build their reputation.
Communities & networks
The development of virtual community can foster cross-industry collaborations. These communities encourage communication and dissemination to new methods, processes, tools, and approaches that improve performance and innovate in organisations. They can be used to improve the effectiveness of meetings and share case histories. A number of industry leaders are exploring the benefits of using communities in industrial manufacturing. See Communities & Networks for Process Knowledge Management: These are a framework to help you manage your knowledge. Communities and networks can be used to connect people from many different locations or disciplines.
Content management
A content-management system may be able to store 200 pages of training information but it can't replace a knowledge management program that can capture both institutional and user-generated knowledge on a topic. Ideally, such a system can capture information from various perspectives, which can be useful for making better decisions and serving customers. For example: If a particular company sells cars then a content-management platform can store all of its sales training materials.
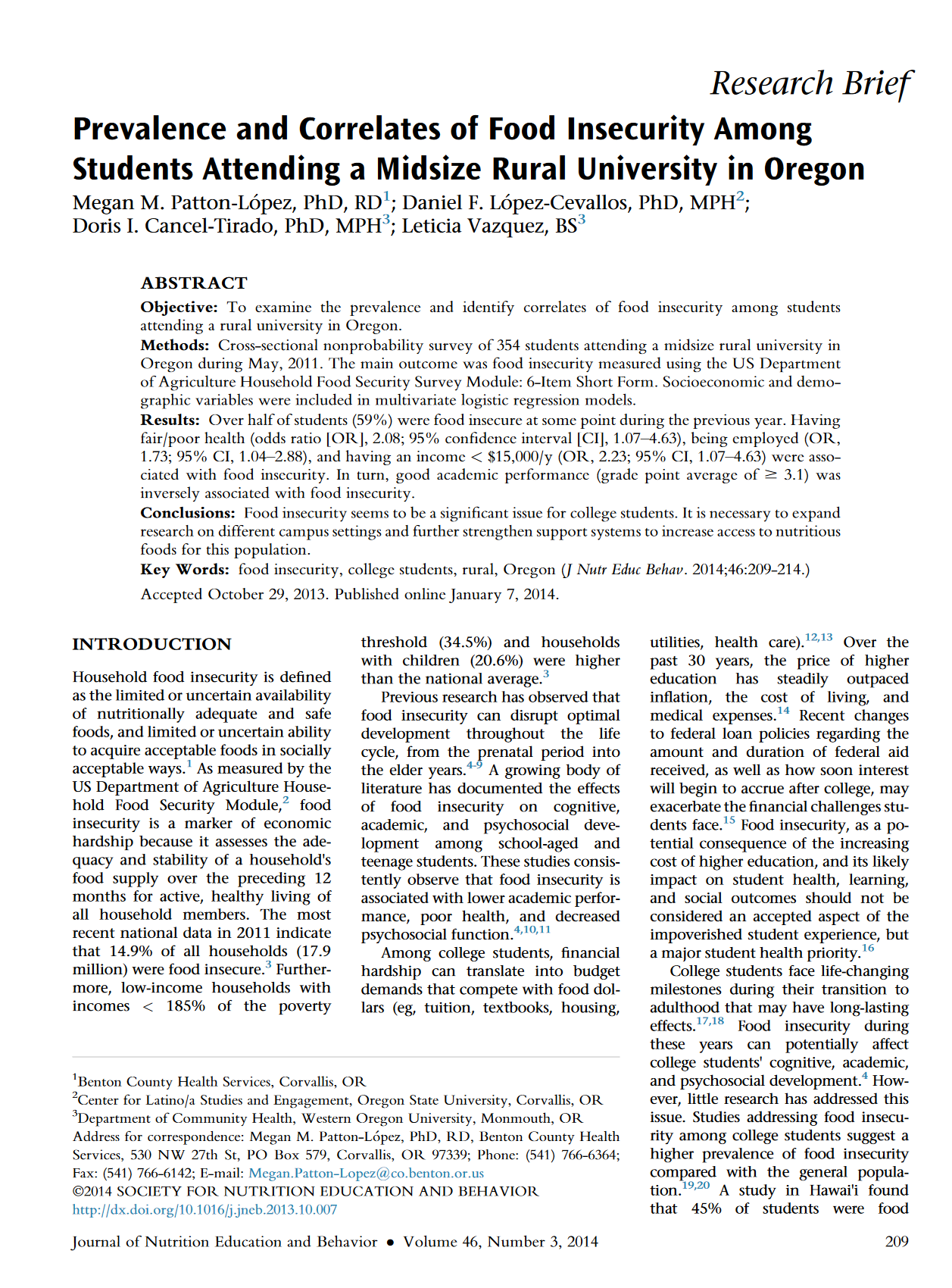
Knowledge mapping
Knowledge mapping is an excellent tool for leveraging your knowledge assets to improve the process. Knowledge mapping is a powerful way to identify knowledge gaps and find solutions for improving your process. It is also a useful tool to increase collaboration among departments. Once you have mapped out your knowledge, you can begin to standardize processes. Knowledge maps are an excellent way to collect and disseminate best practice and improve your organization’s processes.
FAQ
What is Kaizen?
Kaizen, a Japanese term that means "continuous improvement," is a philosophy that encourages employees and other workers to continuously improve their work environment.
Kaizen is based upon the belief that each person should be capable of doing his or her job well.
What are management concepts, you ask?
Management concepts are the principles and practices used by managers to manage people, resources. They cover topics such as job descriptions and performance evaluations, human resource policies, training programs, employee motivation, compens systems, organizational structure, among others.
What are some of the common mistakes made by managers?
Managers can make their jobs more difficult than necessary.
They may not be able to delegate enough responsibility to staff or provide adequate support.
A majority of managers lack the communication skills needed to motivate their team and lead them.
Managers can set unrealistic expectations for their employees.
Managers may attempt to solve all problems themselves, rather than delegating it to others.
What's the difference between Six Sigma and TQM?
The main difference between these two quality-management tools is that six-sigma concentrates on eliminating defects while total QM (TQM), focuses upon improving processes and reducing expenses.
Six Sigma stands for continuous improvement. This method emphasizes eliminating defects using statistical methods such p-charts, control charts, and Pareto analysis.
This method has the goal to reduce variation of product output. This is done by identifying root causes and rectifying them.
Total quality management is the measurement and monitoring of all aspects within an organization. It also includes the training of employees to improve performance.
It is frequently used as an approach to increasing productivity.
Why is project management so important?
To ensure projects run smoothly and meet deadlines, project management techniques are employed.
This is because most businesses rely heavily on project work to produce goods and services.
These projects are essential for companies.
Companies may lose their reputation, time and money if they do not have effective project management.
Why is it so hard to make smart business decisions?
Businesses are complex systems, and they have many moving parts. The people who run them must juggle multiple priorities at once while also dealing with uncertainty and complexity.
Understanding the impact of these factors on the system is crucial to making sound decisions.
It is important to consider the functions and reasons for each part of the system. You then need to consider how those individual pieces interact with each other.
You need to ask yourself if your previous actions have led you to make unfounded assumptions. You might consider revisiting them if they are not.
Asking for assistance from someone else is a good idea if you are still having trouble. You might find their perspective is different from yours and they may have insight that can help you find the solution.
Statistics
- The profession is expected to grow 7% by 2028, a bit faster than the national average. (wgu.edu)
- Our program is 100% engineered for your success. (online.uc.edu)
- The BLS says that financial services jobs like banking are expected to grow 4% by 2030, about as fast as the national average. (wgu.edu)
- Your choice in Step 5 may very likely be the same or similar to the alternative you placed at the top of your list at the end of Step 4. (umassd.edu)
- UpCounsel accepts only the top 5 percent of lawyers on its site. (upcounsel.com)
External Links
How To
How does Lean Manufacturing work?
Lean Manufacturing is a method to reduce waste and increase efficiency using structured methods. They were developed in Japan by Toyota Motor Corporation (in the 1980s). The primary goal was to make products with lower costs and maintain high quality. Lean manufacturing seeks to eliminate unnecessary steps and activities in the production process. It has five components: continuous improvement and pull systems; just-in time; continuous change; and kaizen (continuous innovation). Pull systems involve producing only what the customer wants without any extra work. Continuous improvement means continuously improving on existing processes. Just-in-time refers to when components and materials are delivered directly to the point where they are needed. Kaizen refers to continuous improvement. It is achieved through small changes that are made continuously. The 5S acronym stands for sort in order, shine standardize and maintain. To achieve the best results, these five elements must be used together.
Lean Production System
Six key concepts form the foundation of the lean production system:
-
Flow is about moving material and information as near as customers can.
-
Value stream mapping - break down each stage of a process into discrete tasks and create a flowchart of the entire process;
-
Five S’s - Sorted, In Order. Shine. Standardize. And Sustain.
-
Kanban - visual cues such as stickers or colored tape can be used to track inventory.
-
Theory of constraints - identify bottlenecks during the process and eliminate them with lean tools like Kanban boards.
-
Just-in time - Get components and materials delivered right at the point of usage;
-
Continuous improvement - incremental improvements are made to the process, not a complete overhaul.