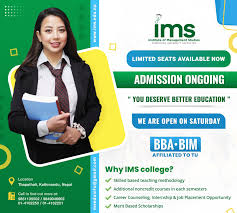
Before you can determine the acceptable level of risk for your organization, it is necessary to first identify what that level is. Then, you must control that risk to an acceptable level. This must be an ongoing process that is balanced. If the risk is manageable, there are no additional actions or control measures. If the risk is unacceptable, additional control or action must be taken. This is known as risk management.
Precautionary principle
Precautionary Principle is an idea that promotes the prevention, detection and treatment of all types of harm. This principle can be used to guide public policy development and the creation of laws. Although this principle is not without fault, it has received considerable international support. The principle emphasizes key aspects of good decisions-making that are often missed in practice or formal decision theory. It provides guidance for solving decision problems. It is also designed to reduce harm by focusing only on benefits and costs.
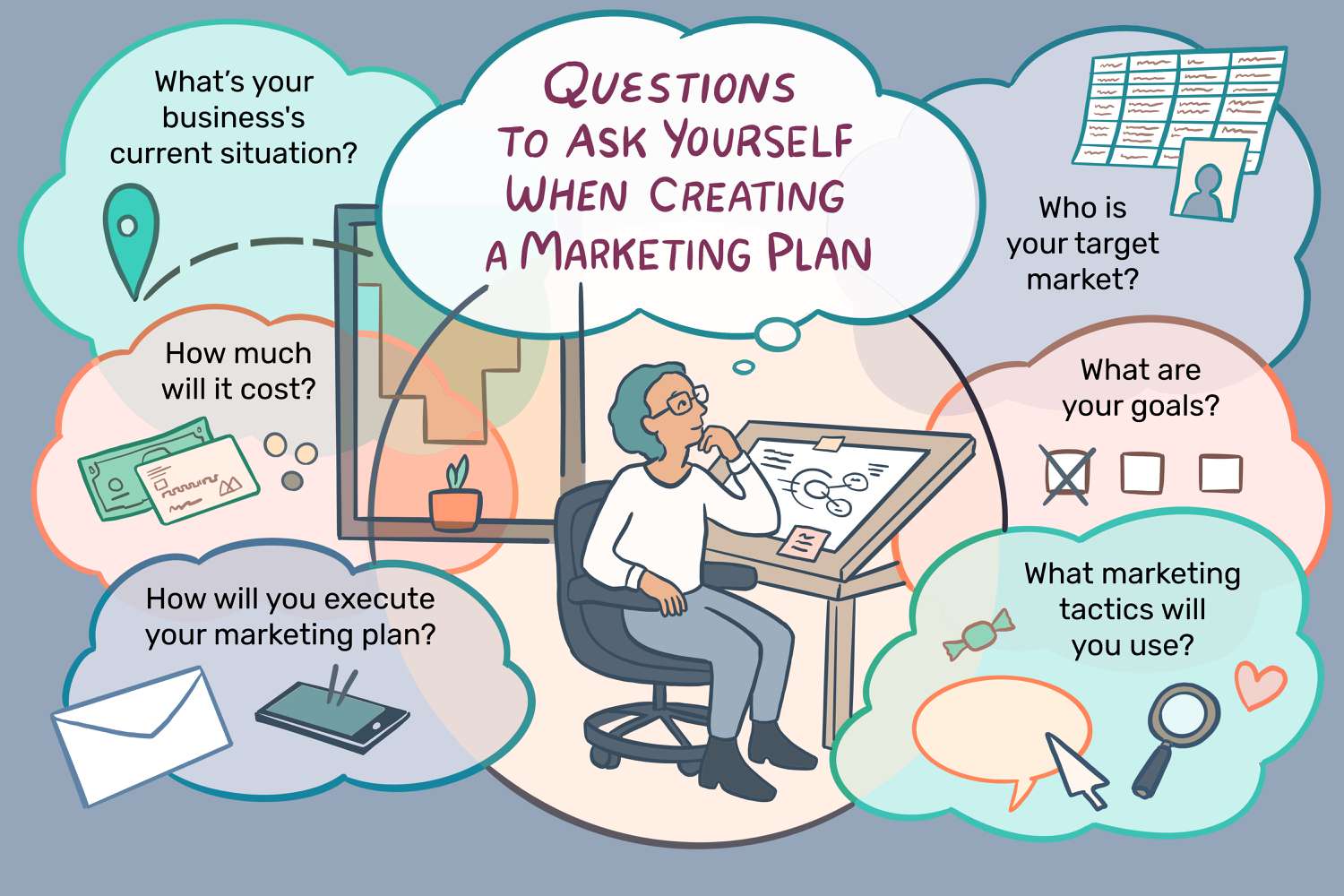
Duplication
A risk management plan must include two key elements: controlling duplication and controlling the risk. Duplication refers to the creation of duplicates or spares for an item or process. These items are not used if the primary item becomes damaged or destroyed. A police department might have a backup car or an emergency operation center. Although the goal of duplication is to reduce potential losses, it can also cause less efficiency.
Monitoring
Monitoring and controlling risk starts with defining and implementing a plan for managing them. Monitoring is the assessment of the plan's impact on the risks and the consequences. In some cases, monitoring may occur without a formal plan. One example is that a risk management group might discuss a weather problem while discussing the best course. This is why the monitoring process becomes so important. This will ensure that risks are managed and allow for the team's monitoring of new risks.
You should choose the control that minimizes or eliminates any hazard.
There are many types of controls that can be used to reduce the risk and hazards. The most effective are the controls that eliminate the hazard and minimise the risk. Other controls include personal protection equipment and administrative control. There are a number of controls that can be used to control a specific hazard. The best one is the one that eliminates the risk. You can combine certain controls with others. You should consider the cost of each control and how it will be used in combination.
Cost
The financial analysis of any company should include the cost to manage risk. The cost is quantified annually for each financial period, and is treated like an investment that must be returned to the company. A portion of companies' budgets is allocated to the risk management division, which has primary responsibility for managing and identifying risks. The employees of the Risk Management Department are charged with determining which risk is most expensive and how they can best be managed.
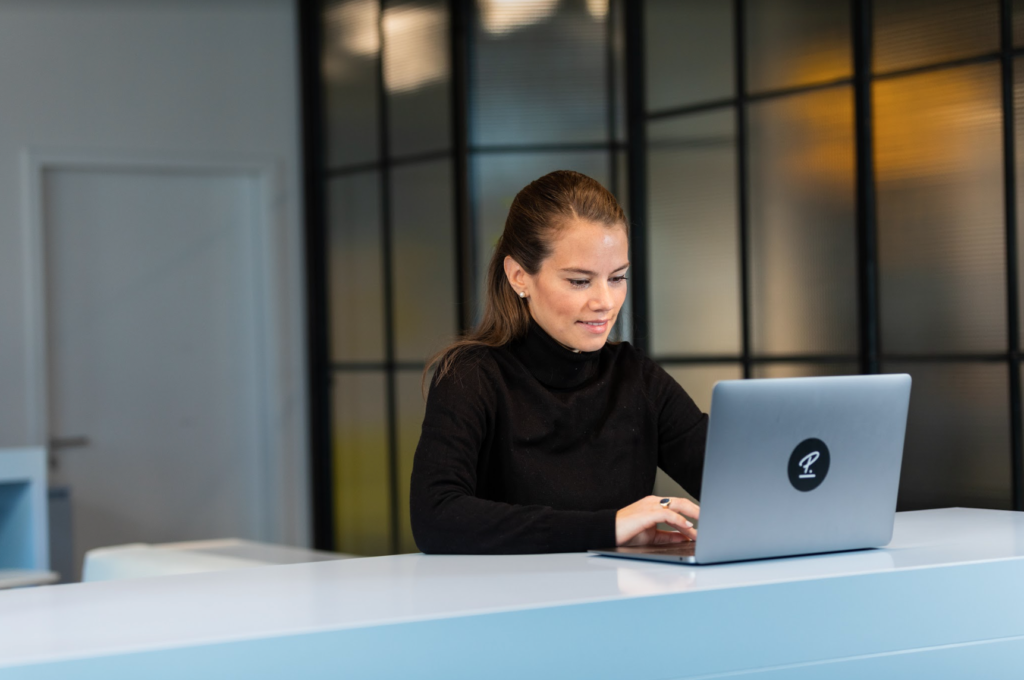
Control system internal
A robust internal control program will help to reduce risk, improve performance and prevent fraud. Internal controls must be communicated clearly to all employees, both internally and externally, in order to be effective. All employees need to be made aware of the goals and responsibilities of internal controls activities. Internal controls must be maintained consistently. Communication is key to ensuring that business owners and managers are accountable across departments and business units. It will also increase the confidence of the organization in its finances.
FAQ
What is Six Sigma?
Six Sigma uses statistical analyses to locate problems, measure them, analyze root cause, fix problems and learn from the experience.
The first step is to identify the problem.
Next, data will be collected and analyzed to determine trends and patterns.
Next, corrective steps are taken to fix the problem.
Finally, the data are reanalyzed in order to determine if it has been resolved.
This continues until the problem has been solved.
How do we create a company culture that is productive?
A successful company culture is one that makes people feel valued and respected.
It is based on three principles:
-
Everybody has something to offer.
-
People are treated fairly
-
People and groups should respect each other.
These values reflect in how people behave. They will treat others with respect and kindness.
They will respect other people's opinions.
These people will inspire others to share thoughts and feelings.
Company culture also encourages open communication, collaboration, and cooperation.
People feel safe to voice their opinions without fear of reprisal.
They know mistakes will be accepted as long as they are dealt with honestly.
The company culture promotes honesty, integrity, and fairness.
Everybody knows they have to tell the truth.
Everyone knows that there are rules and regulations that apply to them.
Nobody expects to be treated differently or given favors.
What is TQM, exactly?
The industrial revolution saw the realization that prices alone were not sufficient to sustain manufacturing companies. This led to the birth of quality. They needed to improve quality and efficiency if they were going to remain competitive.
Management realized the need to improve and created Total Quality Management, which focused on improving all aspects within an organization's performance. It included continuous improvement and employee involvement as well as customer satisfaction.
How to manage employees effectively?
The key to effective management of employees is ensuring their happiness and productivity.
It means setting clear expectations for them and keeping an eye on their performance.
To do this successfully, managers need to set clear goals for themselves and for their teams.
They should communicate clearly with employees. They must communicate clearly with staff members.
They must also keep records of team activities. These include:
-
What did you accomplish?
-
How much work did you put in?
-
Who did it all?
-
Was it done?
-
Why did it happen?
This information can be used for monitoring performance and evaluating results.
What are the most important management skills?
Managerial skills are crucial for every business owner, regardless of whether they run a small store in their locality or a large corporation. These skills include the ability of managing people, finances, time, space, and other factors.
Management Skills are also needed when you're setting goals and objectives, planning strategies, leading teams, motivating employees, resolving problems, creating policies and procedures, and managing change.
As you can see, there are many managerial responsibilities!
What does the term "project management” mean?
Management is the act of managing activities in order to complete a project.
This includes defining the scope, identifying the requirements and preparing the budget. We also organize the project team, schedule the work, monitor progress, evaluate results, and close the project.
What are the five management processes?
Each business has five stages: planning, execution and monitoring.
Planning involves setting goals for the future. Planning includes setting goals for the future.
Execution occurs when you actually carry out the plans. You need to make sure they're followed by everyone involved.
Monitoring is checking on progress towards achieving your objectives. Regular reviews should be done of your performance against targets or budgets.
At the end of every year, reviews take place. They are a chance to see if everything went smoothly during the year. If not, it is possible to make improvements for next year.
After the annual review is complete, evaluations are conducted. It helps you identify the successes and failures. It provides feedback about how people perform.
Statistics
- As of 2020, personal bankers or tellers make an average of $32,620 per year, according to the BLS. (wgu.edu)
- The BLS says that financial services jobs like banking are expected to grow 4% by 2030, about as fast as the national average. (wgu.edu)
- Your choice in Step 5 may very likely be the same or similar to the alternative you placed at the top of your list at the end of Step 4. (umassd.edu)
- The average salary for financial advisors in 2021 is around $60,000 per year, with the top 10% of the profession making more than $111,000 per year. (wgu.edu)
- 100% of the courses are offered online, and no campus visits are required — a big time-saver for you. (online.uc.edu)
External Links
How To
How is Lean Manufacturing done?
Lean Manufacturing processes are used to reduce waste and improve efficiency through structured methods. They were developed by Toyota Motor Corporation in Japan during the 1980s. The main goal was to produce products at lower costs while maintaining quality. Lean manufacturing is about eliminating redundant steps and activities from the manufacturing process. It consists of five basic elements: pull systems, continuous improvement, just-in-time, kaizen (continuous change), and 5S. Pull systems allow customers to get exactly what they want without having to do extra work. Continuous improvement is the continuous improvement of existing processes. Just-in-time refers to when components and materials are delivered directly to the point where they are needed. Kaizen means continuous improvement, which is achieved by implementing small changes continuously. Five-S stands for sort. It is also the acronym for shine, standardize (standardize), and sustain. These five elements work together to produce the best results.
Lean Production System
The lean production system is based on six key concepts:
-
Flow - focus on moving material and information as close to customers as possible;
-
Value stream mapping - Break down each stage in a process into distinct tasks and create an overview of the whole process.
-
Five S's: Sort, Shine Standardize, Sustain, Set In Order, Shine and Shine
-
Kanban – visual signals like colored tape, stickers or other visual cues are used to keep track inventory.
-
Theory of constraints - identify bottlenecks in the process and eliminate them using lean tools like kanban boards;
-
Just-in time - Get components and materials delivered right at the point of usage;
-
Continuous improvement - incremental improvements are made to the process, not a complete overhaul.