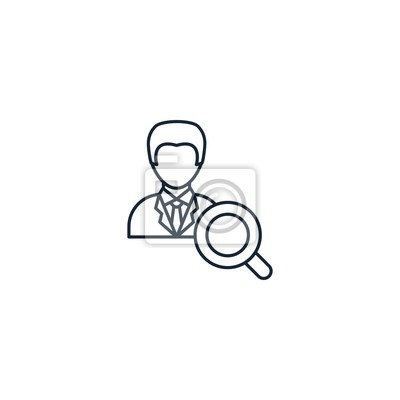
A course in estimation can help you improve your ability to estimate. An estimation course will cover topics such as overhead and profit markup, adding contingencies, adjusting for risk and inflation, determining unit prices, and identifying errors. Both conceptual and detailed estimating will be covered. Both business and industry topics will be covered in the class. It will take approximately 10 weeks to complete a full course. While it is challenging, it will give you valuable skills.
COCOMO software
COCOMO II software is designed to teach software engineers how to estimate software project costs. This course will show you how to estimate software costs, as well as scheduling and staffing levels. The course is divided into several modules, and the exercises will help you learn the theory and practice of software cost estimation. Additionally, the course includes practical exercises that will enable you to apply the techniques you will need in the future.
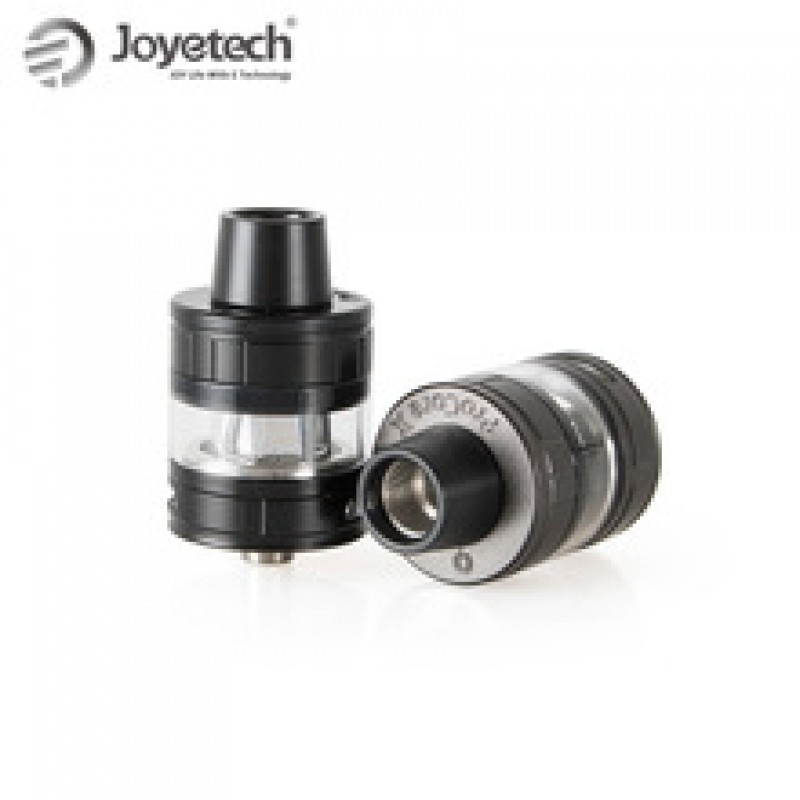
Surveying the land
The Land surveying & cost estimation course will help you learn everything about the field. It also includes a free professional certification. This course provides a comprehensive, instructor-guided overview. This course will help you gain an in-depth understanding of the Land Surveyor job and sector. You will be able to work in this industry with all the skills and knowledge you can get by taking this course. You will also learn how to use specialized software such as AutoCAD and Revit.
Cost estimation
This course focuses specifically on cost estimation and engineering. It is designed for cost estimators, cost control specialists, and project managers who have to manage large, complex projects. Delegates will learn the basics of project management, as well as how to accurately use cost estimation. To gain a deeper understanding, participants will work through practical exercises.
Using RSMeans as a tool of choice for professional cost estimators
RSMeans can be used as a tool to estimate construction costs. You can get precise estimates right within your software. This database can provide data for over 970 locations throughout North America. This feature is very beneficial for the construction industry. You can provide more precise estimates based off current market costs. This feature can be used during the design development phase to streamline the process.
Points earned for completing each of the modules
This online course will teach you how to estimate costs using the right pricing techniques. These techniques are used to calculate costs based on a number of variable factors, including labor, materials, equipment, overhead markup, and profit. Because the course is designed in an asynchronous format you can work at your own speed within each module. There are weekly Zoom sessions as well as discussion boards. Each module has progressive content. You can complete the course in one day, or in smaller sections depending on your schedule. The online course is convenient because you can access it from anywhere and at any time.
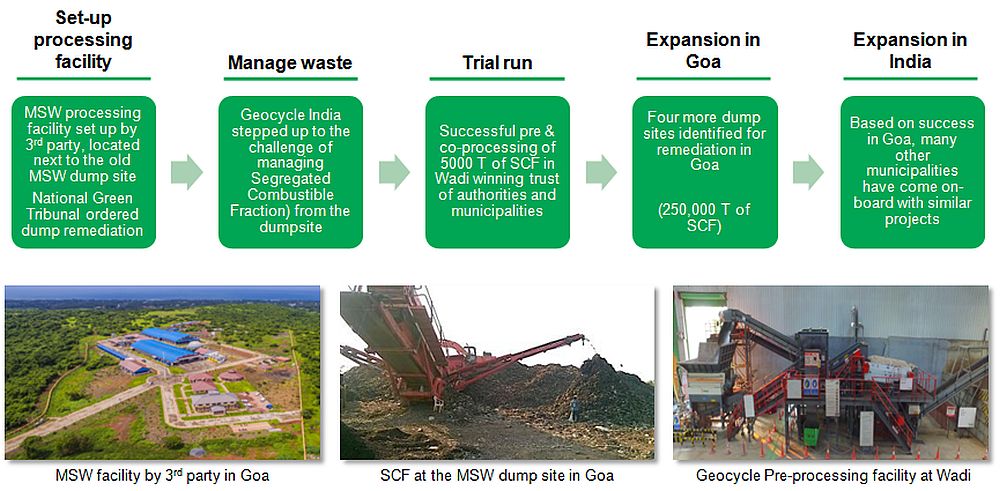
Evaluations for the course
The course gives students the ability to analyze, evaluate, and plan for construction projects. The course covers topics including capital expenditures, operating expenses, and return on investment. Students also learn how to perform a discounted cash flow analysis and net present value analysis. This course also covers methods for valuing long-term projects. The course is intended for people with various levels of experience in construction and project management. The course will teach students how to apply these techniques in real-life situations.
FAQ
What are the four main functions of management?
Management is responsible in planning, organizing and directing people and resources. It includes creating policies and procedures, as well setting goals.
Management assists an organization in achieving its goals by providing direction, coordination and control, leadership, motivation, supervision and training, as well as evaluation.
The four main functions of management are:
Planning - Planning refers to deciding what is needed.
Organizing - Organization involves deciding what should be done.
Directing - Directing is when you get people to do what you ask.
Controlling - Controlling means ensuring that people carry out tasks according to plan.
Why is it so important for companies that they use project management techniques
Project management techniques are used to ensure that projects run smoothly and meet deadlines.
This is due to the fact that most businesses rely heavily upon project work in order to produce goods, and services.
Companies need to manage these projects efficiently and effectively.
Companies may lose their reputation, time and money if they do not have effective project management.
What are some of the common mistakes made by managers?
Sometimes managers make it harder for their employees than is necessary.
They may not delegate enough responsibilities to staff and fail to give them adequate support.
A majority of managers lack the communication skills needed to motivate their team and lead them.
Some managers set unrealistic expectations for their staff.
Managers may attempt to solve all problems themselves, rather than delegating it to others.
What is a basic management tool used in decision-making?
A decision matrix, a simple yet powerful tool for managers to make decisions, is the best. It allows them to think through all possible options.
A decision matrix is a way of representing alternatives as rows and columns. This allows one to see how each alternative impacts other options.
In this example, we have four possible alternatives represented by the boxes on the left side of the matrix. Each box represents one option. The top row shows the status quo (the current situation), and the bottom row shows what would happen if nothing was done at all.
The effect of choosing Option 1 can be seen in column middle. This would result in an increase of sales of $2 million to $3million.
The next two columns show the effects of choosing Options 2 and 3. These positive changes can increase sales by $1 million or $500,000. However, these also involve negative consequences. Option 2 can increase costs by $100 million, while Option 3 can reduce profits by $200,000.
The last column displays the results of selecting Option 4. This results in a decrease of sales by $1,000,000
The best thing about using a decision matrix is that you don't need to remember which numbers go where. You just look at the cells and know immediately whether any given a choice is better than another.
The matrix already does all the work. It's simply a matter of comparing the numbers in the relevant cells.
Here's an example of how you might use a decision matrix in your business.
Advertising is a decision that you make. If you do, you'll be able to increase your revenue by $5 thousand per month. You'll also have additional expenses up to $10,000.
You can calculate the net result of investing in advertising by looking at the cell directly below the one that says "Advertising." That number is $15 thousand. Advertising is worth much more than the investment cost.
What are the 5 management processes?
These five stages are: planning, execution monitoring, review and evaluation.
Planning means setting goals for the long-term. Planning involves defining your goals and how to get there.
Execution occurs when you actually carry out the plans. Everyone involved must follow them.
Monitoring is the act of monitoring your progress towards achieving your targets. This should involve regular reviews of performance against targets and budgets.
Every year, there are reviews. They allow for an assessment of whether all went well throughout the year. If not, it is possible to make improvements for next year.
After each year's review, evaluation occurs. It helps to determine what worked and what didn’t. It also provides feedback on how well people performed.
Statistics
- The average salary for financial advisors in 2021 is around $60,000 per year, with the top 10% of the profession making more than $111,000 per year. (wgu.edu)
- Your choice in Step 5 may very likely be the same or similar to the alternative you placed at the top of your list at the end of Step 4. (umassd.edu)
- UpCounsel accepts only the top 5 percent of lawyers on its site. (upcounsel.com)
- Hire the top business lawyers and save up to 60% on legal fees (upcounsel.com)
- As of 2020, personal bankers or tellers make an average of $32,620 per year, according to the BLS. (wgu.edu)
External Links
How To
What is Lean Manufacturing?
Lean Manufacturing is a method to reduce waste and increase efficiency using structured methods. These processes were created by Toyota Motor Corporation, Japan in the 1980s. The main goal was to produce products at lower costs while maintaining quality. Lean manufacturing is about eliminating redundant steps and activities from the manufacturing process. It includes five main elements: pull systems (continuous improvement), continuous improvement (just-in-time), kaizen (5S), and continuous change (continuous changes). The production of only what the customer needs without extra work is called pull systems. Continuous improvement is the continuous improvement of existing processes. Just-intime refers the time components and materials arrive at the exact place where they are needed. Kaizen stands for continuous improvement. Kaizen can be described as a process of making small improvements continuously. Last but not least, 5S is for sort. These five elements are combined to give you the best possible results.
Lean Production System
Six key concepts are the basis of lean production:
-
Flow - The focus is on moving information and material as close as possible to customers.
-
Value stream mapping - Break down each stage in a process into distinct tasks and create an overview of the whole process.
-
Five S's – Sort, Put In Order Shine, Standardize and Sustain
-
Kanban - visual cues such as stickers or colored tape can be used to track inventory.
-
Theory of Constraints - Identify bottlenecks in the process, and eliminate them using lean tools such kanban boards.
-
Just-intime - Order components and materials at your location right on the spot.
-
Continuous improvement - make incremental improvements to the process rather than overhauling it all at once.