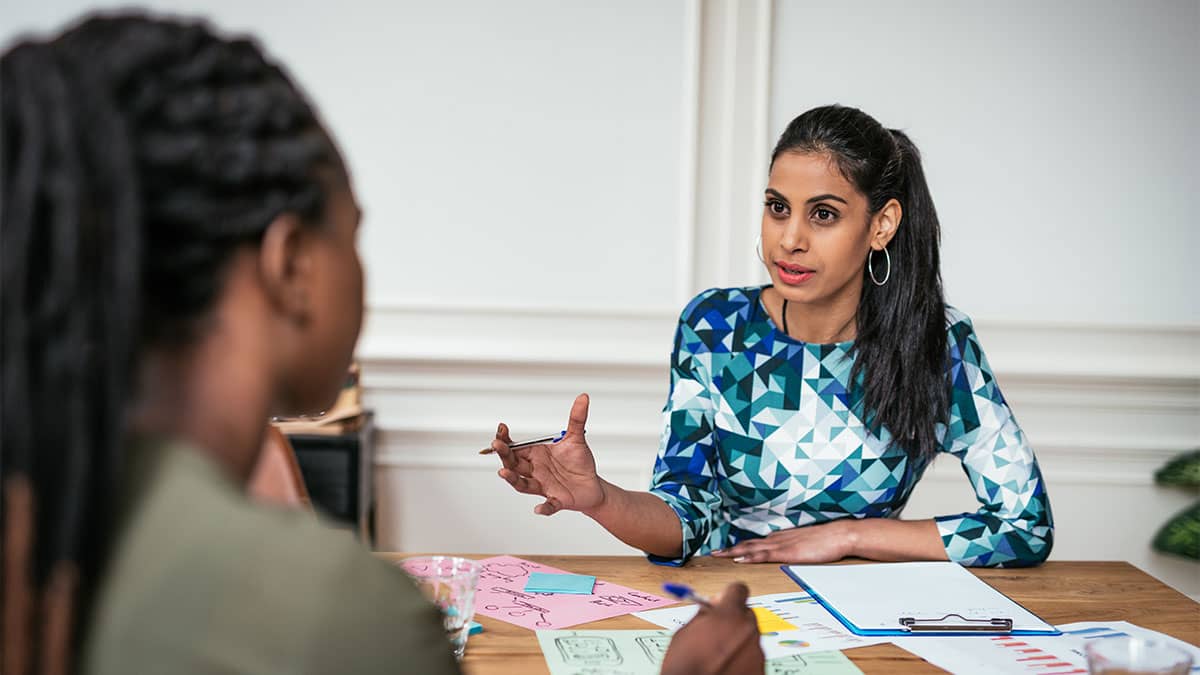
Project managers spend large amounts of their time communicating with stakeholders. As a result, leadership skills are fundamental to their success. However, there are several other key technical skills that they must possess. These are Time management, Planning, Strategic management, and Quality management. These skills will make it easier to manage projects.
Time management
Time management is a key skill that project managers need to master in order for their team to be productive and complete projects on schedule. The key is to effectively organize the project into tasks and sub-tasks and allocate a fixed time period to each task or sub-task group. This skill can be practiced using a variety of management tools and techniques.
Because it allows you to accomplish more in a shorter time, time management is crucial. It helps you avoid overwork and stress. It's important to set aside the right amount of time each job requires so you can fully focus. You will be able complete your project in a timely manner and with less stress.
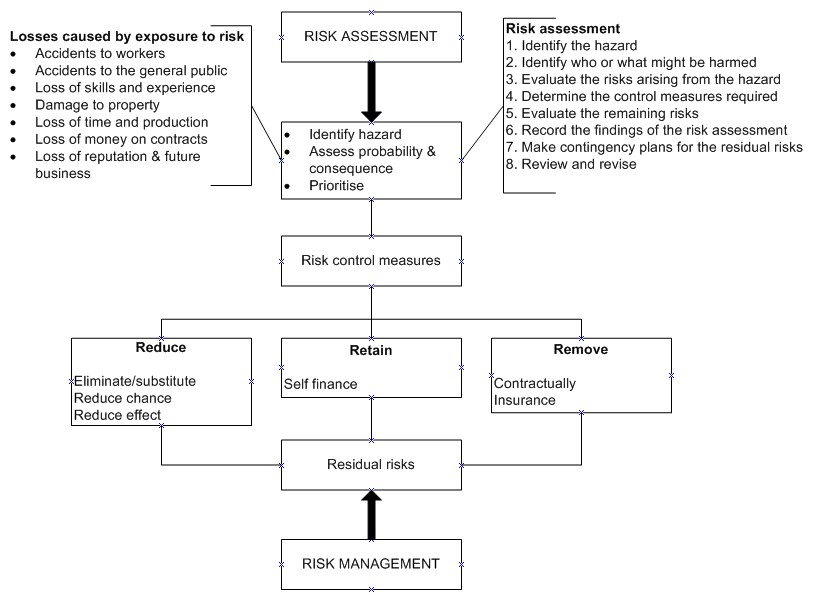
Planning
Planning is an essential part of any project. Project managers must have the right technical skills to plan effectively. Project managers should be able to comprehend project timelines and budgets. They also need to balance cost and scope. Strong writing and reading skills are essential. These skills are essential in many jobs, but they are particularly important in the project management profession. Many project managers are required to understand technical documents and translate them into briefs.
A project manager must also be able to plan the resources of the project. This includes mapping out resources, creating schedules, and justifying key expenses. Other skills required include problem-solving skills and the ability motivate the team.
Strategic management
Strategic management is the ability to plan and execute the results of a project. It includes creating and executing a written strategy plan to achieve the desired outcomes. It also involves the ability to assess the execution and communication of a plan. A strategic management skill that is effective includes the ability to adapt to change and continuously improve.
To be able successfully manage and control projects, project managers need to master strategic management. It is crucial that they have a thorough understanding of business strategy and how it relates to a project's objectives. Without this connection projects could go off-track, or fail.
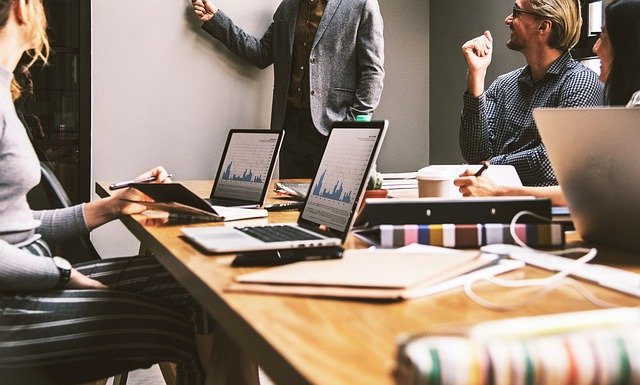
Quality management
The Quality manager's responsibility is to ensure that each project is completed as efficiently as possible. This involves being able to communicate with the team and ensure that they know exactly what their responsibilities are. This includes being able communicate the requirements and performance criteria of the project.
Also, project managers need to be problem-solving and analytical. They must be able to work with a diverse team, and they must be able to communicate with all project stakeholders effectively. They must also be able to create effective project schedules. This skill is lacking in many project managers.
FAQ
What does the term "project management” mean?
That is the management of all activities associated with a project.
Our services include the definition of the scope, identifying requirements, preparing a budget, organizing project teams, scheduling work, monitoring progress and evaluating the results before closing the project.
What is TQM exactly?
The industrial revolution was when companies realized that they couldn't compete on price alone. This is what sparked the quality movement. They needed to improve quality and efficiency if they were going to remain competitive.
Management responded to the need to improve, and developed Total Quality Management (TQM). This focused on improving every aspect of an organization’s performance. It included continuous improvement and employee involvement as well as customer satisfaction.
What are the four major functions of Management?
Management is responsible to plan, organize, direct, and control people and resources. It also includes developing policies and procedures and setting goals.
Management aids an organization in reaching its goals by providing direction and coordination, control, leadership motivation, supervision, training, evaluation, and leadership.
The following are the four core functions of management
Planning - Planning refers to deciding what is needed.
Organizing - Organization involves deciding what should be done.
Directing - Directing means getting people to follow instructions.
Controlling – This refers to ensuring that tasks are carried out according to plan.
Why is project management important for companies?
To ensure projects run smoothly and meet deadlines, project management techniques are employed.
This is because most businesses rely on project work for their products and services.
These projects must be managed efficiently and effectively by companies.
Companies could lose their time, reputation, and money without effective project management.
Statistics
- Hire the top business lawyers and save up to 60% on legal fees (upcounsel.com)
- Our program is 100% engineered for your success. (online.uc.edu)
- The profession is expected to grow 7% by 2028, a bit faster than the national average. (wgu.edu)
- The average salary for financial advisors in 2021 is around $60,000 per year, with the top 10% of the profession making more than $111,000 per year. (wgu.edu)
- This field is expected to grow about 7% by 2028, a bit faster than the national average for job growth. (wgu.edu)
External Links
How To
How is Lean Manufacturing done?
Lean Manufacturing uses structured methods to reduce waste, increase efficiency and reduce waste. They were developed by Toyota Motor Corporation in Japan during the 1980s. The primary goal was to make products with lower costs and maintain high quality. Lean manufacturing eliminates unnecessary steps and activities from a production process. It is made up of five elements: continuous improvement, continuous improvement, just in-time, continuous change, and 5S. Pull systems involve producing only what the customer wants without any extra work. Continuous improvement involves constantly improving upon existing processes. Just-in-time refers to when components and materials are delivered directly to the point where they are needed. Kaizen refers to continuous improvement. It is achieved through small changes that are made continuously. Fifth, the 5S stand for sort, set up in order to shine, standardize, maintain, and standardize. To achieve the best results, these five elements must be used together.
Lean Production System
Six key concepts form the foundation of the lean production system:
-
Flow: The goal is to move material and information as close as possible from customers.
-
Value stream mapping - break down each stage of a process into discrete tasks and create a flowchart of the entire process;
-
Five S’s - Sorted, In Order. Shine. Standardize. And Sustain.
-
Kanban is a visual system that uses visual cues like stickers, colored tape or stickers to keep track and monitor inventory.
-
Theory of constraints: Identify bottlenecks and use lean tools such as kanban boards to eliminate them.
-
Just-intime - Order components and materials at your location right on the spot.
-
Continuous improvement - Make incremental improvements rather than overhauling the entire process.