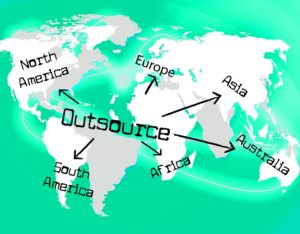
If you haven't heard of management of change (MOC), then you should. This best practice is an excellent way to avoid unwanted consequences and keep your organisation running smoothly. Read on for more information about MOC and its stages. These are the essential MOC stages. By following these stages, you'll be able to successfully manage change in your organization. What exactly is MOC? Why is this important?
MOC is a process
MOC is often overlooked within organizations. Changes are a common source of workplace accidents due to unfamiliarity and a lack of process safety information. Organizations rush to make changes and forget about the importance of managing risk. Unless they're in the process of redesigning their production processes, changes to existing systems and procedures can result in accidents. This is especially true in the case of industries that deal with dangerous substances and energy.
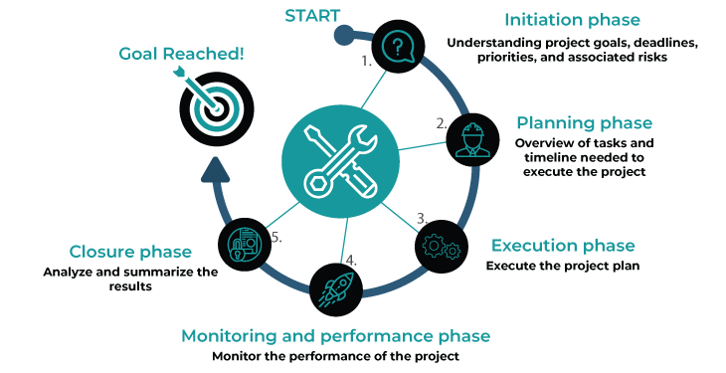
It is made up of eight stages
McKinsey's Change Management Model describes the process of change as an architectural process that includes eight stages: planning, implementation, monitoring and evaluation. It also provides a framework for sustainability. While the first three stages address the business side, the second and third stage deal with the emotional. The eighth stage should be about culture. The eighth stage is about culture. To ensure that successful change management is possible, the organization's culture should be able adapt to the changes.
It prevents unintended consequences
Unintended consequences result from people not always thinking through their actions before taking a decision. People might decide to base their decisions on past performance and not the current situation. This can result in decisions that have unintended consequences and can ultimately be counterproductive. There are many ways to manage change and minimize unwanted consequences. One example is the implementation of a new procedure that could have negative or positive unintended effects. A test group will be formed to evaluate the potential impact of new technology.
It is a best practice
The key to a brighter future is successful change management. From identifying the vision to engaging the team, this best practice can help pave the way for an organizational shift. Remember that change management also involves soft elements. It is important to consider these. These elements are crucial to any change management project's success. These elements must be taken into account in order to make the whole change process smooth.
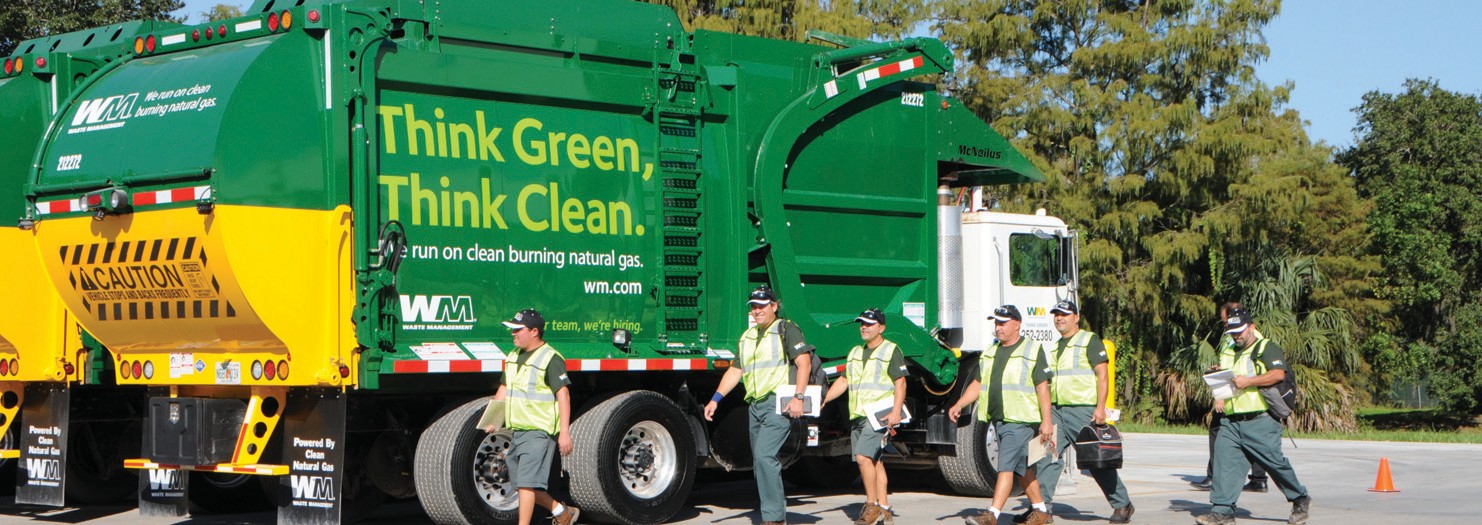
It is important to maintain regulatory compliance
Companies must track metrics and report on how they are performing to ensure compliance with regulatory requirements. These metrics can be used by organizations to monitor process compliance and determine risks/performance indicators. Metrics can also be used to determine whether regulatory changes have been made and what impact they will have on an enterprise. By monitoring change, proactive organizations can anticipate future regulatory requirements and demonstrate evidence of good compliance practices. This article will focus on the important metrics that should be monitored and reported.
FAQ
What are the four major functions of Management?
Management is responsible to plan, organize, direct, and control people and resources. This includes setting goals, developing policies and procedures, and creating procedures.
Organizations can achieve their goals through management. This includes leadership, coordination, control and motivation.
The four main functions of management are:
Planning - Planning involves determining what needs to be done.
Organizing is the act of deciding how things should go.
Directing - This refers to getting people follow instructions.
Controlling: Controlling refers to making sure that people do what they are supposed to.
What is Kaizen?
Kaizen is a Japanese term which means "continuous improvement." This philosophy encourages employees to continually look for ways to improve the work environment.
Kaizen is founded on the belief of everyone being able to do their job well.
Why does it sometimes seem so difficult to make good business decisions?
Businesses are complex systems, and they have many moving parts. People who manage them have to balance multiple priorities while dealing with complexity and uncertainty.
It is important to understand the effects of these factors on the system in order to make informed decisions.
It is important to consider the functions and reasons for each part of the system. Next, consider how each piece interacts with the others.
It is also worth asking yourself if you have any unspoken assumptions about how you have been doing things. You might consider revisiting them if they are not.
If you're still stuck after all this, try asking someone else for help. You may be able to see things from a different perspective than you are and gain insight that can help you find a solution.
What is a simple management tool that aids in decision-making and decision making?
A decision matrix is an easy but powerful tool to aid managers in making informed decisions. They can think about all options and make informed decisions.
A decision matrix is a way to organize alternatives into rows and columns. This makes it easy for you to see how each option affects other options.
We have four options in this example. They are represented by the boxes to the left of the matrix. Each box represents an option. The top row represents the current state of affairs, and the bottom row is indicative of what would happen in the event that nothing were done.
The middle column displays the impact of selecting Option 1. In this example, it would lead to an increase in sales of between $2 million and $3 million.
The effects of options 2 and 3 are shown in the next columns. These are good changes, they increase sales by $1million or $500,000. These changes can also have negative effects. Option 2 increases the cost of goods by $100,000. Option 3 decreases profits and makes them less attractive by $200,000.
The last column shows you the results of Option 4. This involves decreasing sales by $1 million.
The best thing about a decision matrix is the fact that you don't have to remember which numbers go with what. The best thing about a decision matrix is that you can simply look at the cells, and immediately know whether one option is better or not.
The matrix has already done all of the work. It is as simple a matter of comparing all the numbers in each cell.
Here is an example of how a decision matrix might be used in your business.
It is up to you to decide whether to spend more money on advertising. You'll be able increase your monthly revenue by $5000 if you do. However, additional expenses of $10 000 per month will be incurred.
Look at the cell immediately below the one that states "Advertising" to calculate the net investment in advertising. It's $15,000. Therefore, you should choose to invest in advertising since it is worth more than the cost involved.
How does Six Sigma work
Six Sigma uses statistical analyses to locate problems, measure them, analyze root cause, fix problems and learn from the experience.
The first step is to identify the problem.
Next, data are collected and analyzed in order to identify patterns and trends.
The problem is then rectified.
Finally, data is reanalyzed to determine whether the problem has been eliminated.
This continues until you solve the problem.
Statistics
- As of 2020, personal bankers or tellers make an average of $32,620 per year, according to the BLS. (wgu.edu)
- Our program is 100% engineered for your success. (online.uc.edu)
- Hire the top business lawyers and save up to 60% on legal fees (upcounsel.com)
- The profession is expected to grow 7% by 2028, a bit faster than the national average. (wgu.edu)
- The BLS says that financial services jobs like banking are expected to grow 4% by 2030, about as fast as the national average. (wgu.edu)
External Links
How To
What is Lean Manufacturing?
Lean Manufacturing processes are used to reduce waste and improve efficiency through structured methods. They were created by Toyota Motor Corporation in Japan in the 1980s. The primary goal was to make products with lower costs and maintain high quality. Lean manufacturing seeks to eliminate unnecessary steps and activities in the production process. It is made up of five elements: continuous improvement, continuous improvement, just in-time, continuous change, and 5S. Pull systems are able to produce exactly what the customer requires without extra work. Continuous improvement is the continuous improvement of existing processes. Just-in-time refers to when components and materials are delivered directly to the point where they are needed. Kaizen stands for continuous improvement. Kaizen can be described as a process of making small improvements continuously. Last but not least, 5S is for sort. These five elements work together to produce the best results.
Lean Production System
Six key concepts are the basis of lean production:
-
Flow - focuses on moving information and materials as close to customers as possible.
-
Value stream mapping: This is a way to break down each stage into separate tasks and create a flowchart for the entire process.
-
Five S's, Sort, Set in Order, Shine. Standardize. and Sustain.
-
Kanban - use visual signals such as colored tape, stickers, or other visual cues to keep track of inventory;
-
Theory of constraints: Identify bottlenecks and use lean tools such as kanban boards to eliminate them.
-
Just-in Time - Send components and material directly to the point-of-use;
-
Continuous improvement - incremental improvements are made to the process, not a complete overhaul.