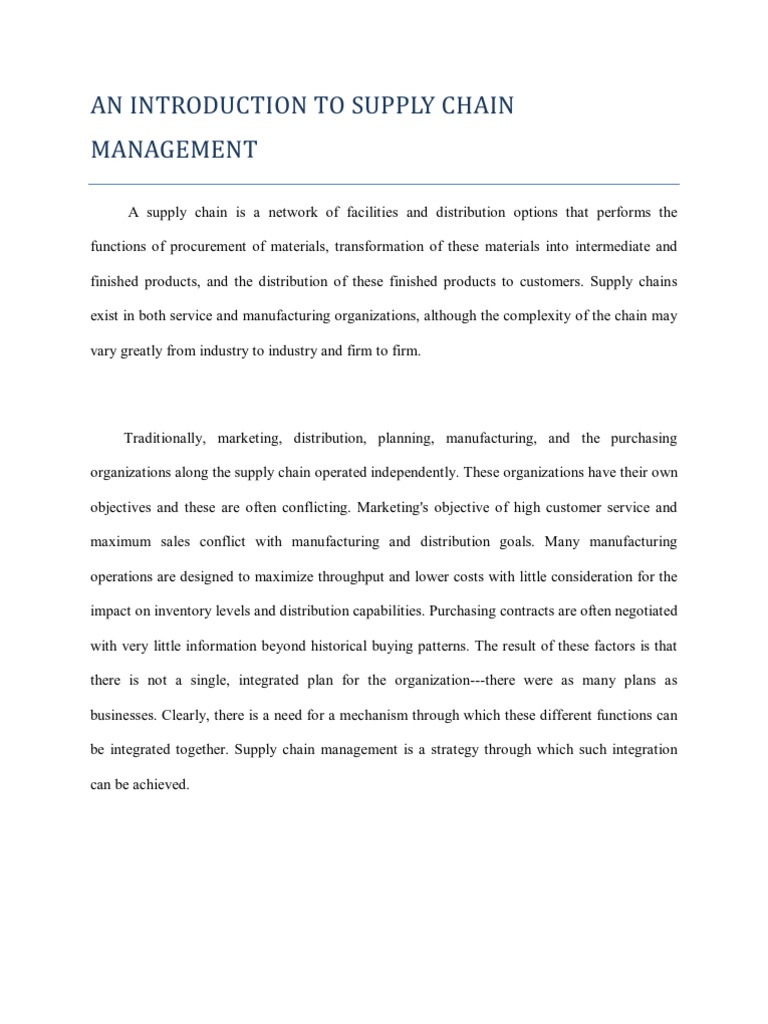
Many technologies can be used to improve the management of waste in the oilfield. These technologies include sensors that can be attached to trash cans. These sensors can be used by front-load haulers and roll-off haulers to manage their container inventory and routes. They can also use these sensors to schedule their routes, and more evenly distribute their jobs to their drivers. This technology has been developed by companies such as Compology. Its sensors can monitor the tilt of a container, which helps them better manage their inventory.
Smart waste management
The way we dispose of our waste is being transformed by smart waste management technologies. Sensors placed on trash cans and recycle bins monitor the waste level and alert authorities when a container gets full. Advanced optical sorters as well as disk screens allow for fast sorting. Natural gas is now the preferred fuel for garbage trucks, which is more fuel efficient and quieter. The mobile apps can help to streamline waste management.
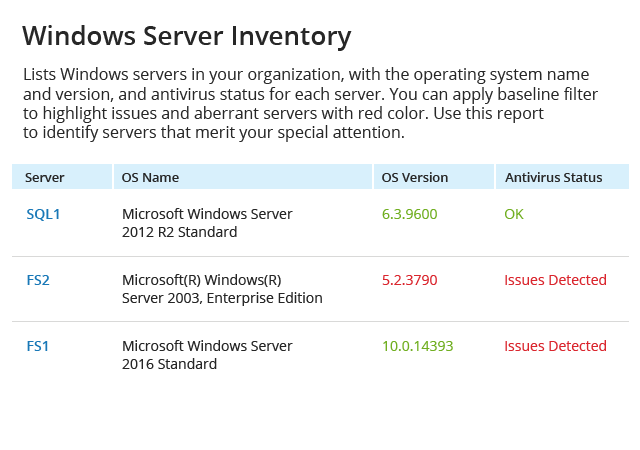
Sensors in dumpsters
The sensors in dumpsters can assist waste management companies to monitor the condition of their containers. Waste management companies can use data collected from sensors to customize pickup and deliver times for each dumpster. Machine learning can also help them sort waste according the type.
Recycling apps
Recycling apps are a great tool to simplify recycling for individuals. These apps allow users to search for recycling centers in their local area and organize recyclable materials according to category. It is easy to track when and how much you can recycle. They provide the most current news and insight in the sector of waste and recycling.
Oil field waste management
Many technologies are used to manage oil field waste. They reduce pollution and help minimize the amount of waste produced. These technologies can be used to manage all types of oil- and gas-related wastes. Superfund liability laws have made oil and gas waste recycling more important. Some technologies are more effective than others, but their success is dependent on top management support, a comprehensive inventory of waste streams, characterization of chemical additives, and flexibility to accommodate site-specific variations.
Autoclave sterilization technology
An autoclave sterilization system can be an effective tool in waste management. This sterilization process involves removing air from the waste and using high-pressure steam for pathogen destruction. This method is very effective in eliminating a wide range of pathogens including prions. It does not require hazardous chemicals. These autoclaves are available in many sizes and can accommodate a variety of medical waste. The temperatures used are typically in the range of 250 to 300 degrees Fahrenheit.
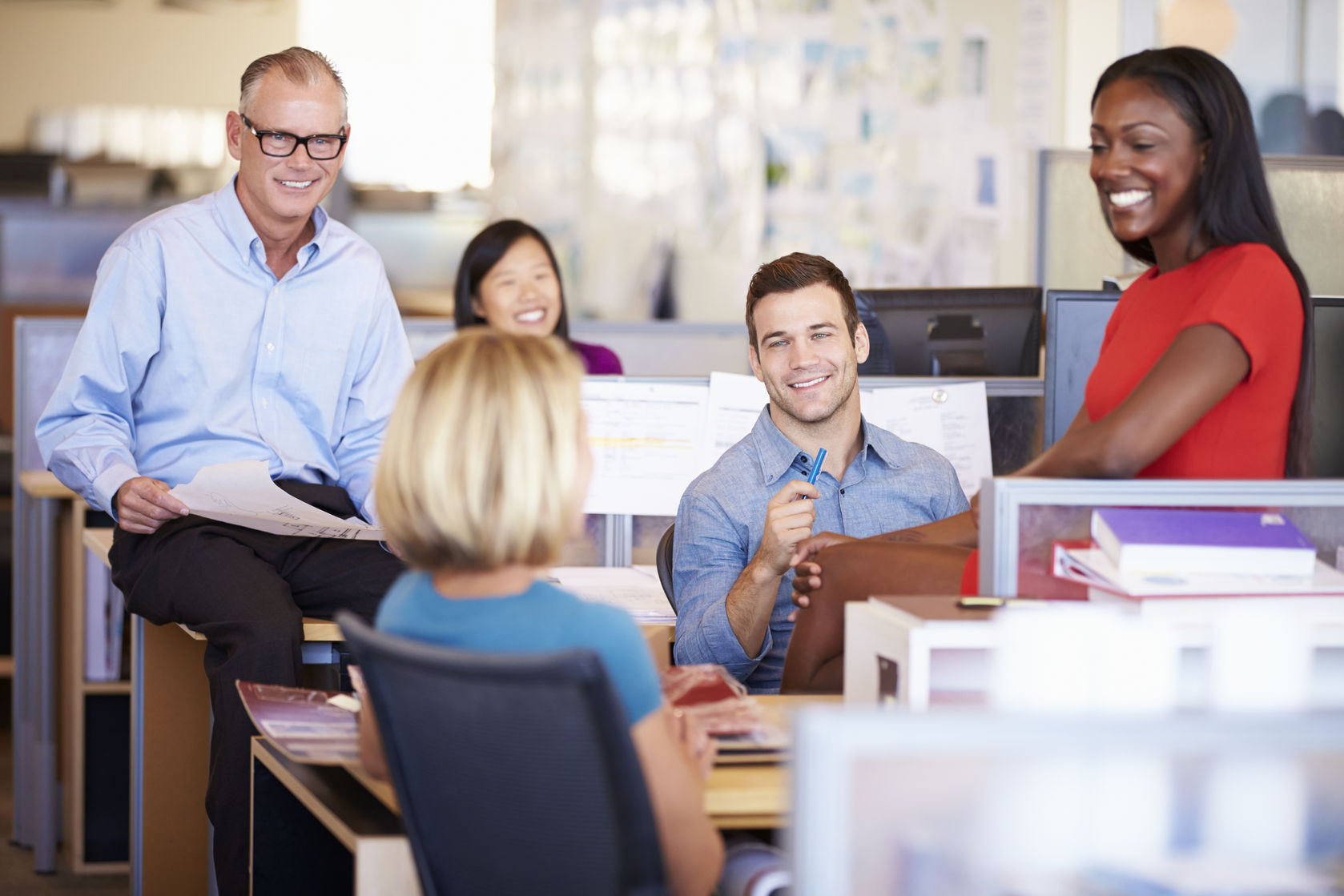
Bin-E
Bin-E's waste management system combines AI-based object detection and automatic waste detection in order to optimize waste management for every facility. It is highly accurate and can save both time and money. It eliminates the need to manually sort and collect waste by using its automated recognition and segregation process.
FAQ
What is Kaizen?
Kaizen is a Japanese term for "continuous improvement." It encourages employees constantly to look for ways that they can improve their work environment.
Kaizen is built on the belief that everyone should be able do their jobs well.
What is Six Sigma?
It's an approach to quality improvement that emphasizes customer service and continuous learning. It is a method that eliminates defects using statistical techniques.
Motorola's 1986 efforts to improve manufacturing process efficiency led to the creation of Six Sigma.
The idea quickly spread in the industry. Many organizations today use six-sigma methods to improve product design and production, delivery and customer service.
What are the five management methods?
Each business has five stages: planning, execution and monitoring.
Planning involves setting goals for the future. Planning involves defining your goals and how to get there.
Execution takes place when you actually implement the plans. Everyone involved must follow them.
Monitoring is the act of monitoring your progress towards achieving your targets. This should involve regular reviews of performance against targets and budgets.
Every year, there are reviews. They allow for an assessment of whether all went well throughout the year. If not there are changes that can be made to improve the performance next year.
Following the annual review, evaluation is done. It helps to identify what went well and what didn’t. It also provides feedback on the performance of people.
Statistics
- The average salary for financial advisors in 2021 is around $60,000 per year, with the top 10% of the profession making more than $111,000 per year. (wgu.edu)
- As of 2020, personal bankers or tellers make an average of $32,620 per year, according to the BLS. (wgu.edu)
- Hire the top business lawyers and save up to 60% on legal fees (upcounsel.com)
- Your choice in Step 5 may very likely be the same or similar to the alternative you placed at the top of your list at the end of Step 4. (umassd.edu)
- The BLS says that financial services jobs like banking are expected to grow 4% by 2030, about as fast as the national average. (wgu.edu)
External Links
How To
How can Lean Manufacturing be done?
Lean Manufacturing is a method to reduce waste and increase efficiency using structured methods. They were created in Japan by Toyota Motor Corporation during the 1980s. The primary goal was to make products with lower costs and maintain high quality. Lean manufacturing emphasizes removing unnecessary steps from the production process. It is made up of five elements: continuous improvement, continuous improvement, just in-time, continuous change, and 5S. The production of only what the customer needs without extra work is called pull systems. Continuous improvement means continuously improving on existing processes. Just-in–time refers when components or materials are delivered immediately to their intended destination. Kaizen is continuous improvement. This can be achieved by making small, incremental changes every day. Last but not least, 5S is for sort. These five elements can be combined to achieve the best possible results.
Lean Production System
Six key concepts form the foundation of the lean production system:
-
Flow - focuses on moving information and materials as close to customers as possible.
-
Value stream mapping is the ability to divide a process into smaller tasks, and then create a flowchart that shows the entire process.
-
Five S's - Sort, Set In Order, Shine, Standardize, and Sustain;
-
Kanban - use visual signals such as colored tape, stickers, or other visual cues to keep track of inventory;
-
Theory of constraints - identify bottlenecks in the process and eliminate them using lean tools like kanban boards;
-
Just-in time - Get components and materials delivered right at the point of usage;
-
Continuous improvement: Make incremental improvements to the process instead of overhauling it completely.