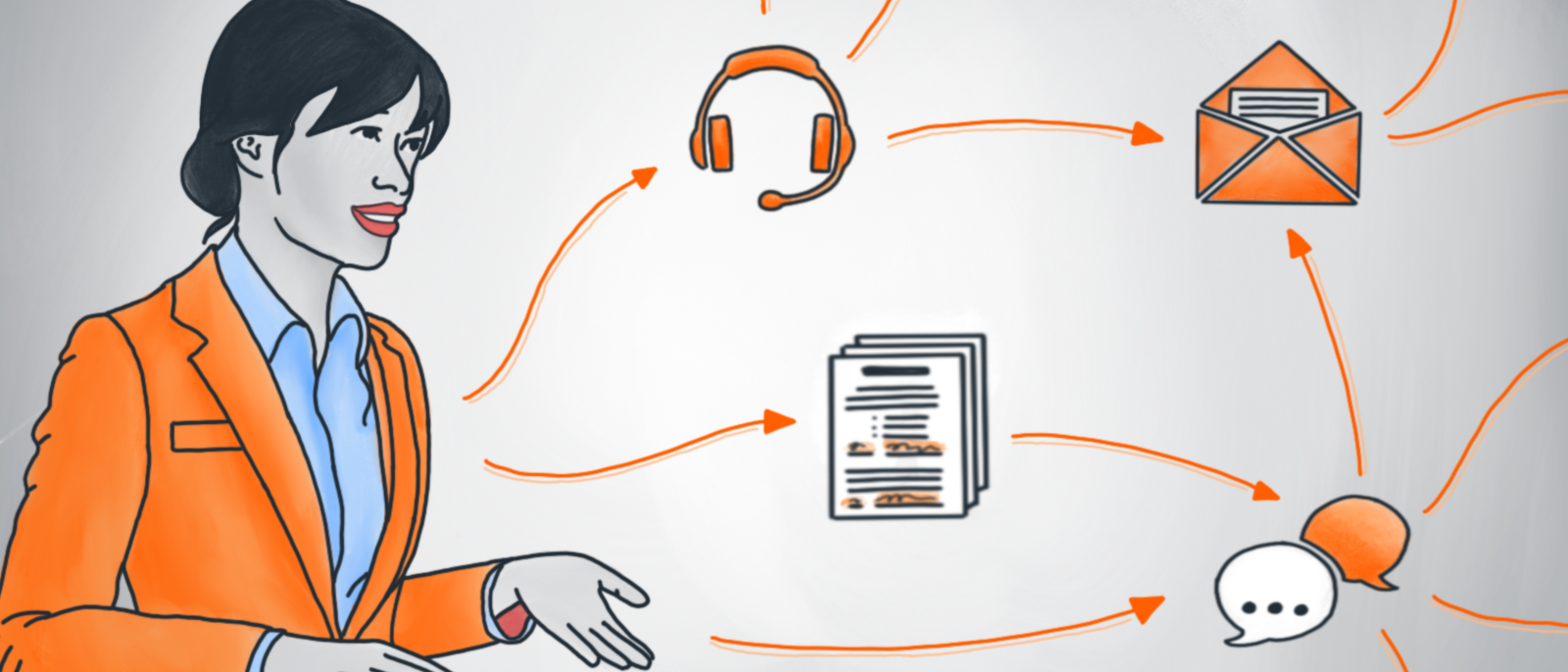
The Waste Management Expert is responsible in developing project plans and making service suggestions. The National Account Manager and this position help to build client relationships as well as new program initiatives. As part of the Waste Management Specialist's team, he or she recruits associates who are able to reach professional standards. He/she also actively participates in professional learning. To ensure clients receive the best service, they work closely with the National Account Manager. Additionally, the position supervises and leads projects.
Jim Bentley
Advanced Disposal National Accounts, a complete waste management company, is the commercial division. Jim Bentley will be responsible in developing relationships with prospective clients and strategic vendors partners. He will also oversee business development efforts with other companies in the company's extensive network of more than 7,000 environmental service providers across North America. Bentley has 21 years of solid waste experience, including a stint as a senior account executive at Green Leaf Compaction.
Ashish Sharma
Ashish Sharma, Senior Manager of Digital for Waste Management, leads the digital solutions team and technology teams in Asset Management's business unit. He also leads the digital team working on New York's Marine Transfer Station project. He joined Waste Management as a senior leader in 2014. He previously held senior leadership roles at IBM and Deloitte & Touche, LLC. He has more than 16 years of experience in the technology industry.
Sharma has been involved in many projects while at Waste Management. Recent work includes the New York marine transfer station. It was this station that supported Waste Management's $3.3B contract with the Department of Sanitation. Sharma was also awarded the Waste360 40 Under 40 Award. This honor highlights his leadership and innovative approach to waste management. Ashish Sharma has won a number of industry awards, including the prestigious "Best New Product" award from Waste360.
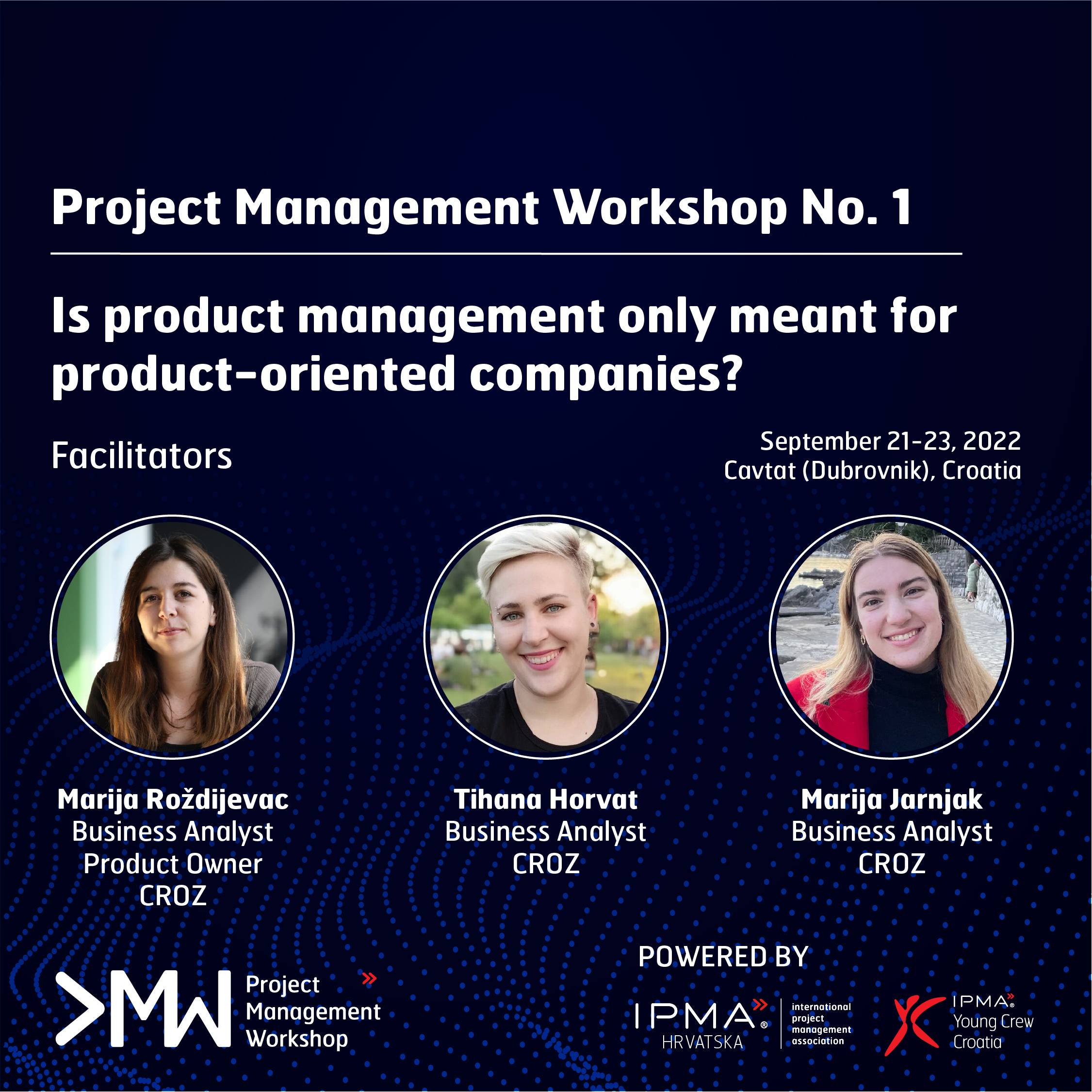
FAQ
What are the steps involved in making a decision in management?
The decision-making process for managers is complex and multifaceted. It includes many factors such as analysis, strategy planning, implementation and measurement. Evaluation, feedback and feedback are just some of the other factors.
Management of people requires that you remember that they are just as human as you are, and can make mistakes. You can always improve your performance, provided you are willing to make the effort.
This video shows you how management makes decisions. We discuss different types of decisions as well as why they are important and how managers can navigate them. You'll learn about the following topics:
Why is it important that companies use project management methods?
Project management techniques ensure that projects run smoothly while meeting deadlines.
This is due to the fact that most businesses rely heavily upon project work in order to produce goods, and services.
These projects must be managed efficiently and effectively by companies.
Without effective project management, companies may lose money, time, and reputation.
What is TQM, exactly?
The quality movement was born during the industrial revolution when manufacturing companies realized they could not compete on price alone. To remain competitive, they had to improve quality as well as efficiency.
Management realized the need to improve and created Total Quality Management, which focused on improving all aspects within an organization's performance. It included continuous improvement and employee involvement as well as customer satisfaction.
Statistics
- The BLS says that financial services jobs like banking are expected to grow 4% by 2030, about as fast as the national average. (wgu.edu)
- Our program is 100% engineered for your success. (online.uc.edu)
- As of 2020, personal bankers or tellers make an average of $32,620 per year, according to the BLS. (wgu.edu)
- The average salary for financial advisors in 2021 is around $60,000 per year, with the top 10% of the profession making more than $111,000 per year. (wgu.edu)
- UpCounsel accepts only the top 5 percent of lawyers on its site. (upcounsel.com)
External Links
How To
How is Lean Manufacturing done?
Lean Manufacturing uses structured methods to reduce waste, increase efficiency and reduce waste. They were developed in Japan by Toyota Motor Corporation (in the 1980s). The aim was to produce better quality products at lower costs. Lean manufacturing emphasizes removing unnecessary steps from the production process. It is composed of five fundamental elements: continuous improvement; pull systems, continuous improvements, just-in–time, kaizen, continuous change, and 5S. Pull systems are able to produce exactly what the customer requires without extra work. Continuous improvement means continuously improving on existing processes. Just-in-time refers to when components and materials are delivered directly to the point where they are needed. Kaizen refers to continuous improvement. It is achieved through small changes that are made continuously. Five-S stands for sort. It is also the acronym for shine, standardize (standardize), and sustain. To achieve the best results, these five elements must be used together.
Lean Production System
Six key concepts are the basis of lean production:
-
Flow - focus on moving material and information as close to customers as possible;
-
Value stream mapping is the ability to divide a process into smaller tasks, and then create a flowchart that shows the entire process.
-
Five S's, Sort, Set in Order, Shine. Standardize. and Sustain.
-
Kanban: Use visual signals such stickers, colored tape, or any other visual cues, to keep track your inventory.
-
Theory of constraints: Identify bottlenecks and use lean tools such as kanban boards to eliminate them.
-
Just-intime - Order components and materials at your location right on the spot.
-
Continuous improvement - make incremental improvements to the process rather than overhauling it all at once.