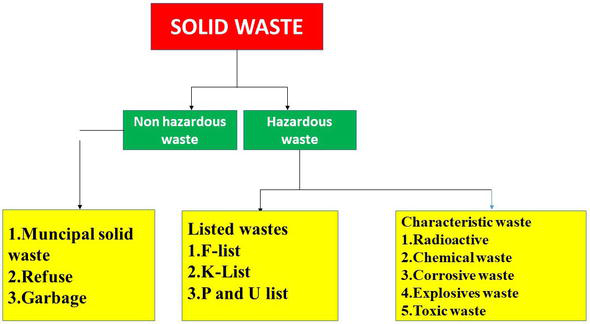
Logistics refers to the movement of goods from production to final delivery. Many people, companies, activities and information are involved in the logistics industry to make goods accessible for purchase. A logistics supply chain is a collaborative effort between multiple stakeholders. Although logistics is the main focus of many companies' operations, the process can incorporate other components such as transport and software. Here are the types of logistical system. You can read on to learn about these systems and how you can improve your company’s supply chain operations.
Logistics is the movement, storage, and distribution of goods from initial production to final delivery
Logistics is the efficient movement and storage, from product creation to delivery. Optimizing flow ensures that products reach customers at the correct time, at the right place and at the right price. These seven "rights of logistics" are listed below. One of these is the right time. Customers should receive products at the correct time and in the right conditions.
Inbound logistics concentrates on the inbound movement materials and products to manufacturers. While outbound logistics focuses more on the outbound flow goods and information from outside sources, Inbound logistics focuses on acquiring materials and arranging inbound transportation, storage, and distribution to customers. Reverse logistics deals with the return shipment of finished products and their packaging and the management of leftover inventory, and in some cases, reusable packaging and disposal of waste.
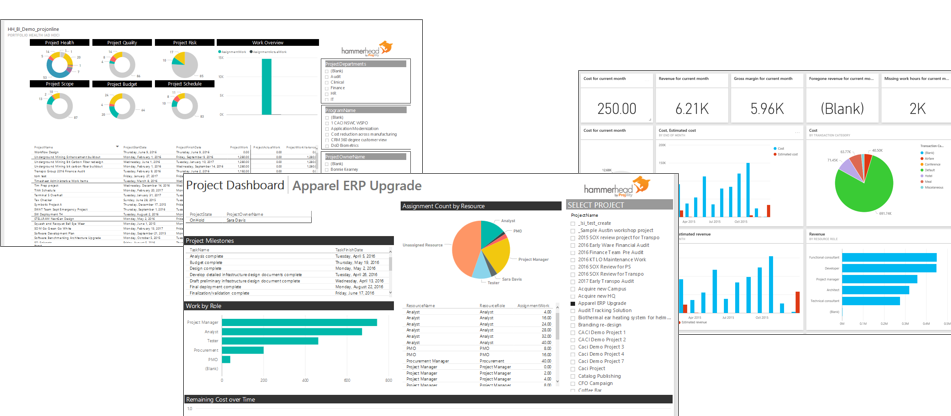
It is a risk-adjusted enterprise
A risk-adjusted investor (RAR) is a type of investment that involves capital or funds that are more risky than normal business investments. The difference between risk-adjusted investments and the yields of normal business investments is called the opportunity cost of risk. RAR can reduce investment risk and assist business owners in managing cash flows across different business functions.
It is just a part of a larger, more collaborative supply chain
A highly integrated supply chain is a highly interdependent network of suppliers that rely on timely deliveries of quality components. Failure to deliver could result in the end of the chain. Even the best logistics providers or suppliers can't avoid all disruptions. Each participant must assess the risks to the system to ensure the overall chain is efficient and smooth.
Manufacturers and retailers can collaborate to benefit both sides. A recent example is the collaboration between a retailer, and a large U.S.-based retail chain. This resulted at a lower logistic cost between the factory to the store. Collaborations in this area can also help retailers increase their sales. In this area, retailers and manufacturers can cooperate to reduce transport and labor expenses between the factory-store location.
It involves software
Supply management software can help companies manage their entire supply network. Software manages every aspect of the supply chain from vendor relationships to transaction. Supply chain management software should be used regardless of whether you run a small business or large corporation. These programs help you manage inventory, supplier relationships, and flow of data across the organization. These programs can cover all stages of product development including warehousing, shipping, and distribution. These programs may include inventory management and insight on trends and customer demand.

The use of logistics software includes improving inventory management, real-time fleet management, and streamlined communication. It can also increase customer service. It automates daily tasks to turn data into actionable insights that can be used by business owners. It improves communication and inventory processes which are essential to the success of supply chain management. These applications can increase customer service and profitability. You might be curious about the benefits of purchasing software for your business.
FAQ
What role should a manager play within a company
Managers' roles vary from industry to industry.
A manager generally manages the day to-day operations in a company.
He/she makes sure that the company meets its financial obligations, and that it produces goods or services that customers desire.
He/she makes sure that employees adhere to the rules and regulations as well as quality standards.
He/she plans new products and services and oversees marketing campaigns.
What are the four main functions of management?
Management is responsible for organizing, managing, directing and controlling people, resources, and other activities. It also includes developing policies and procedures and setting goals.
Organizations can achieve their goals through management. This includes leadership, coordination, control and motivation.
Management's four main functions are:
Planning - Planning refers to deciding what is needed.
Organizing is the act of deciding how things should go.
Directing – This means to get people to follow directions.
Controlling – This refers to ensuring that tasks are carried out according to plan.
What is a basic management tool used in decision-making?
A decision matrix is an easy but powerful tool to aid managers in making informed decisions. It helps them think systematically about all the options available to them.
A decision matrix represents alternatives in rows and columns. This allows one to see how each alternative impacts other options.
We have four options in this example. They are represented by the boxes to the left of the matrix. Each box represents an alternative. The status quo (the current condition) is shown in the top row, and what would happen if there was no change?
The middle column displays the impact of selecting Option 1. This would result in an increase of sales of $2 million to $3million.
The results of choosing Option 2 and 3 can be seen in the columns below. These are good changes, they increase sales by $1million or $500,000. But, they also have some negative consequences. Option 2 increases costs by $100 thousand, while Option 3 decreases profits to $200 thousand.
Finally, the last column shows the results of choosing Option 4. This would result in a reduction of sales of $1 million.
The best part of using a decision-matrix is that it doesn't require you to know which numbers belong where. You can just glance at the cells and see immediately if one given choice is better.
The matrix already does all the work. It's as easy as comparing numbers in the appropriate cells.
Here is an example of how a decision matrix might be used in your business.
Advertising is a decision that you make. If you do, you'll be able to increase your revenue by $5 thousand per month. However, additional expenses of $10 000 per month will be incurred.
You can calculate the net result of investing in advertising by looking at the cell directly below the one that says "Advertising." That number is $15 thousand. Advertising is worth much more than the investment cost.
Statistics
- Your choice in Step 5 may very likely be the same or similar to the alternative you placed at the top of your list at the end of Step 4. (umassd.edu)
- UpCounsel accepts only the top 5 percent of lawyers on its site. (upcounsel.com)
- This field is expected to grow about 7% by 2028, a bit faster than the national average for job growth. (wgu.edu)
- 100% of the courses are offered online, and no campus visits are required — a big time-saver for you. (online.uc.edu)
- Hire the top business lawyers and save up to 60% on legal fees (upcounsel.com)
External Links
How To
How do you get your Six Sigma license?
Six Sigma is a quality management tool to improve processes and increase efficiency. Six Sigma is a method that helps companies get consistent results from their operations. Named after the Greek word for "sigmas", the name refers to the first two letters. Motorola created this process in 1986. Motorola recognized the need to standardize manufacturing processes in order to produce better products at a lower cost. Due to the different workers involved, there was a lack of consistency. To solve this problem, they decided to use statistical tools such as control charts and Pareto analysis. They would then apply these techniques to all aspects of their operation. This would allow them to make any necessary changes. There are three main steps to follow when trying to get your Six Sigma certification. Find out if you are qualified. Before you can take any tests, you will need to take some classes. After passing the classes, you will be able to take the tests. You'll need to go back and review all the information you received in class. Next, you'll be ready for the test. If you pass, you'll get certified. Finally, your certifications will be added to your resume.