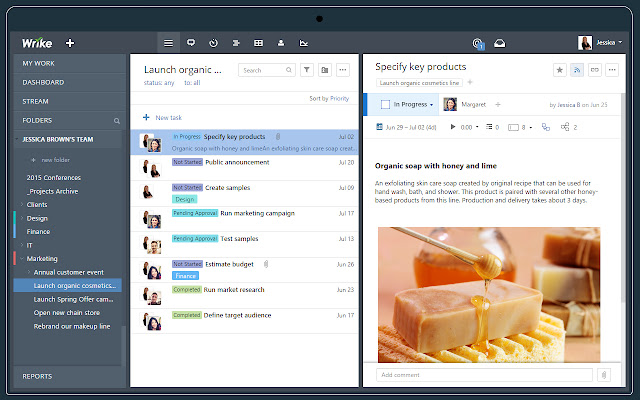
In project management, resourcing refers to identifying the resources necessary for completing a task. This includes both human and material resources. Acquiring these resources can be done through hiring workers or purchasing materials. Once these resources are acquired, they need to be allocated to various tasks. Project managers can turn to resource managers for help in allocating resources in order ensure that projects run on time and within budget.
Allocation of resource
Resource allocation is an important aspect of project management. You need to take into account many factors, including the budget, timeline and available resources. To ensure efficient resource allocation, a precise project scope is crucial. A clearly defined scope will ensure that resources are allocated according to priority and need. The scope helps to establish the budget and deadlines.
A well-planned resource allocation program will assist in project planning from start to finish. It will help identify details early in the process, preventing re-allocation of resources later. It is best to have a clear start and finish for the project. It will list high-priority tasks that must all be completed within the set time frame.
Cost resources
Cost resources are placeholders for costs of a particular type that are assigned to a task. They can be used in multiple tasks. A different airfare resource will be required for each task, such as two tasks that involve plane trips. A cost resource is entered in the task information dialog box when it is assigned. This allows a more accurate view of the costs.
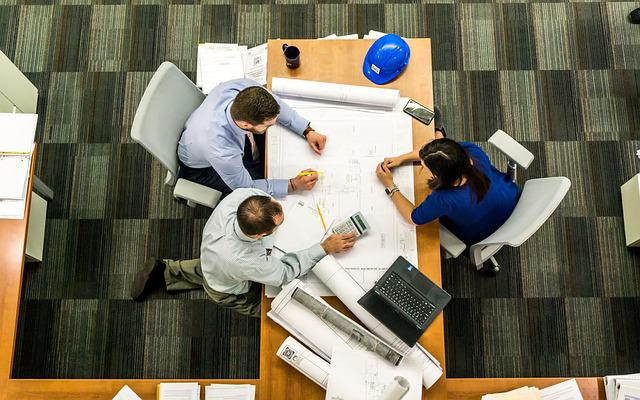
Fixed costs and variable cost are two types of cost resources. The latter can be used to help you better manage the costs associated with a task. Travel and client meetings can be included in cost resources. While project accounting systems protect these costs, their currency value does not depend on how much work was actually performed. This means that the cost resources could change as the task owner makes adjustments.
Stakeholder management
A typical project has two parts: the stakeholders and the project team. The project team includes members who will be involved in the project's creation, and the stakeholders are the people who will impact the project's success. The ResMP documents the roles and responsibilities for the team. The stakeholder register lists the types of stakeholders that the project will require.
Stakeholders must be identified early in the project and their interests and influence should be assessed. The relationships between the project team, stakeholders, and their staff must be positive and productive. During the stakeholder identification phase, the project manager should identify potential stakeholders, their roles and departments, and their interests, knowledge, and influence. Depending on their level of influence, stakeholders may be bifurcated into categories based on their authority, legitimacy, or concerns.
Automation
The modern project manager will find automation of resourcing an extremely powerful tool. This process automates repetitive tasks and allows teams to concentrate on high-value work that is cognitively stimulating. This results in higher ROI. Over the past decade, software-as-a-service tools have proliferated, making companies more efficient than ever before. The sheer number of these tools can have a negative impact on employee productivity.
Automation of work involves applying technologies, programs, and robotics to achieve specific outcomes with minimal or no human input. It is not intended to replace project managers but to free them from administrative tasks and let them focus on more valuable activities. Automation of work has many benefits, including in the creation and management new products and services.
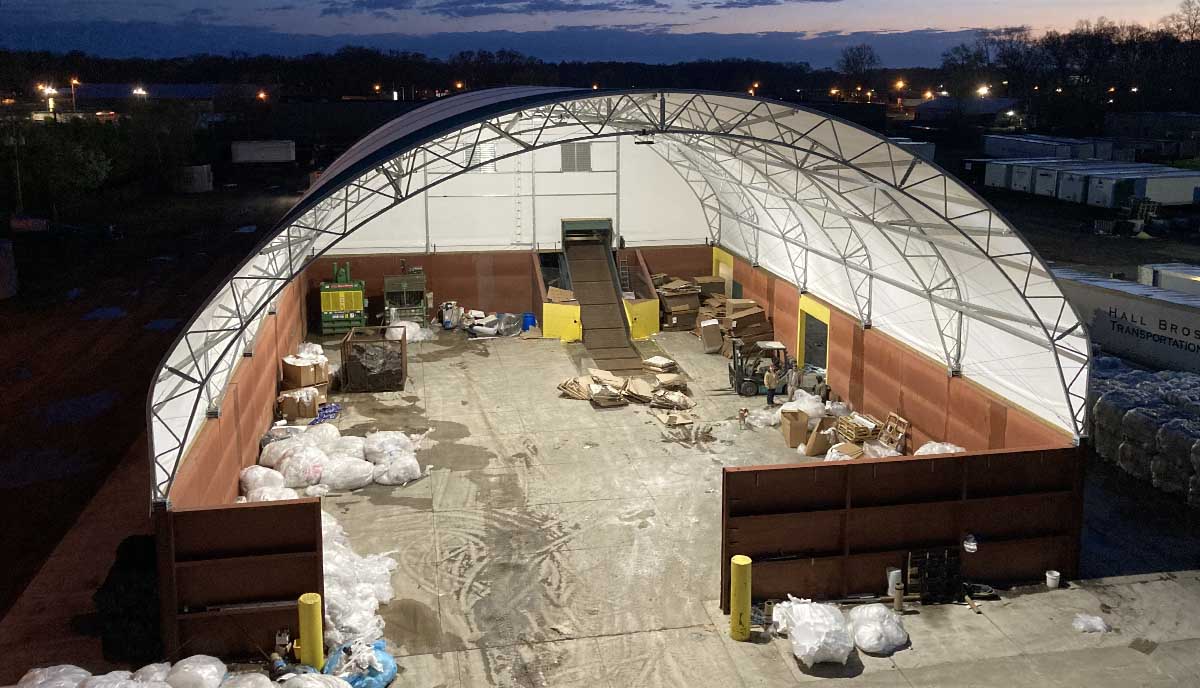
Templates
Resource management is an integral part of any project. Project managers can use templates to help plan for their resources and teams. These templates can be downloaded for free and don't require special software. These templates are compatible with spreadsheet software. They allow project managers to adjust time periods and durations for different projects, so that each resource can work on several projects at once.
You can find many templates online. You can customize them to fit the specific needs and help you see how tasks are connected. They can also be used to compare the project's progress with the original schedule. Some templates can be more complex than others. Others are made for specific tasks or phases.
FAQ
How can a manager motivate employees?
Motivation can be defined as the desire to achieve success.
You can get motivated by doing something enjoyable.
You can also feel motivated by making a positive contribution to the success in the organization.
For example, if your goal is to become a physician, you will probably find it more motivational to see patients rather than to read a lot of medicine books.
Another type of motivation comes from within.
One example is a strong sense that you are responsible for helping others.
You might even enjoy the work.
Ask yourself why you feel so motivated.
Then, consider ways you could improve your motivation.
What is the difference between leadership and management?
Leadership is about influence. Management is all about controlling others.
Leaders inspire others, managers direct them.
A leader inspires others to succeed, while a manager helps workers stay on task.
A leader develops people; a manager manages people.
What is the main difference between Six Sigma Six Sigma TQM and Six Sigma Six Sigma?
The main difference between these two quality-management tools is that six-sigma concentrates on eliminating defects while total QM (TQM), focuses upon improving processes and reducing expenses.
Six Sigma is a methodology for continuous improvement. It emphasizes the elimination of defects by using statistical methods such as control charts, p-charts, and Pareto analysis.
This method seeks to decrease variation in product output. This is done by identifying and correcting the root causes of problems.
Total quality management involves measuring and monitoring all aspects of the organization. It also includes training employees to improve performance.
It is used to increase productivity.
What is TQM exactly?
When manufacturing companies realized that price was not enough to compete, the industrial revolution brought about the quality movement. They needed to improve quality and efficiency if they were going to remain competitive.
Management realized the need to improve and created Total Quality Management, which focused on improving all aspects within an organization's performance. It involved continuous improvement, employee participation, and customer satisfaction.
Statistics
- The BLS says that financial services jobs like banking are expected to grow 4% by 2030, about as fast as the national average. (wgu.edu)
- Hire the top business lawyers and save up to 60% on legal fees (upcounsel.com)
- Our program is 100% engineered for your success. (online.uc.edu)
- The profession is expected to grow 7% by 2028, a bit faster than the national average. (wgu.edu)
- This field is expected to grow about 7% by 2028, a bit faster than the national average for job growth. (wgu.edu)
External Links
How To
What is Lean Manufacturing?
Lean Manufacturing methods are used to reduce waste through structured processes. They were created by Toyota Motor Corporation in Japan in the 1980s. The primary goal was to make products with lower costs and maintain high quality. Lean manufacturing is about eliminating redundant steps and activities from the manufacturing process. It has five components: continuous improvement and pull systems; just-in time; continuous change; and kaizen (continuous innovation). The production of only what the customer needs without extra work is called pull systems. Continuous improvement is the continuous improvement of existing processes. Just-in time refers to components and materials being delivered right at the place they are needed. Kaizen is continuous improvement. This can be achieved by making small, incremental changes every day. Fifth, the 5S stand for sort, set up in order to shine, standardize, maintain, and standardize. These five elements work together to produce the best results.
The Lean Production System
Six key concepts are the basis of lean production:
-
Flow - focus on moving material and information as close to customers as possible;
-
Value stream mapping is the ability to divide a process into smaller tasks, and then create a flowchart that shows the entire process.
-
Five S’s - Sorted, In Order. Shine. Standardize. And Sustain.
-
Kanban - visual cues such as stickers or colored tape can be used to track inventory.
-
Theory of constraints: identify bottlenecks in your process and eliminate them using lean tools, such as kanban board.
-
Just-in Time - Send components and material directly to the point-of-use;
-
Continuous improvement - Make incremental improvements rather than overhauling the entire process.